Latest News
June 1, 2006
By David Prawel and Wolfgang Geist
PLM is an intriguing vision indeed. Marketing departments worldwide buzz with the latest claims of the virtues and value of their software and the brave new world of productivity and profit enabled by the PLM vision. But successful PLM has proven elusive. Not only are the processes embodied in the vision highly complex, but successful PLM depends in large part on effective communication and collaboration, which is proving quite hard for manufacturers to do well.
A recent survey of 650 manufacturing executives by Industry Week highlights the mission-critical nature of collaboration. A full 62% of purchasing executives listed supplier collaboration as the most effective contributor to increased profitability and reduced cost. More than 97% of product development executives selected collaboration with customers as the most effective strategy for meeting customer requirements and bringing innovative products to market. And, more than 35% chose collaboration with customers as the key strategy to reducing product development time to market. It is interesting that these business objectives match exactly those touted for PLM. Coincidence? Not so.
Effective collaboration is one of the keys to winning in the business of manufacturing and innovation. Enterprise PLM and PDM business processes are built on 3D product data. And it remains extremely difficult for the various constituents of a modern manufacturing value chain to share product data. Little wonder then that collaboration is so difficult to get right.
Built for CAD Users, Not Everyone
Much has been written about problems sharing CAD data. Studies have estimated that billions of dollars each year are wasted in the automotive business alone due to poor CAD data interoperability. A large portion of the blame goes to geometry problems relating to the CAD modelers themselves. CAD translation software provides many good solutions to these problems, including capability to search out problematic geometry and topology, and automatically repair it. Spatial Corp. takes a slightly different approach by providing software libraries that are built into solutions by other software vendors.
International standards like IGES and STEP have emerged to help alleviate interoperability problems, but these standards are often limited in scope and slow to evolve. International standardization committees, such as ISO (International Standards Organization) or Germany’s DIN, need years to define and approve standards and therefore lag behind many industrial needs.
An additional limitation of existing solutions is that they are built for CAD people. Many interoperability problems have nothing to do with CAD models themselves, but present a huge impediment to effective collaboration. People can’t work together if they can’t access and share their product data.
A typical manufacturing organization has many professionals in the value chain that could make use of their company’s 3D product data assets, but simply can’t work with the data. The 3D data is often available in their PDM system, but the tools either aren’t available or aren’t usable by people who aren’t trained in CAD. CAD software is too complex and too expensive for these non-CAD professionals to use.
In a recent study, Daratech Inc. showed the impact of 3D-product data generation in downstream engineering and manufacturing processes. The company found that a single 3D CAD authoring tool may generate 3D data that could be used by more than 100 additional users in the enterprise. These numbers are likely much higher if one accounts for the extended enterprise, such as suppliers and customers.
|
This Actify image shows 3D CAD data embedded in a Microsoft Word file. |
Manufacturers spend a lot of money creating valuable 3D product data assets, but the clear advantages of using 3D can’t be realized if the data isn’t available to anyone who could benefit from it.
Many multi-format CAD model “viewers” are available to help non-CAD professionals access and use their 3D product data. Actify and Informative Graphics, for example, provide multi-format viewing products that enable non-CAD users to access, view, and mark up dozens of 3D formats.
In addition to the 3D format and business process problems, many companies have created significant internal barriers to better interoperability and reuse of 3D product data. Some of the biggest of these lie in the business process and have to do with how RFQs are bundled with 3D models and other documents and then submitted, whether an organization’s business processes are mature enough to leverage 3D product data, and so on. Efficient collaboration requires the right data be available to the right people at the right time, in a form they can use.
For example, very few companies have standardized their design methodologies so all designers use the same design principles, making it easier for their models to be shared and understood by their fellow designers and engineers. Most companies have experienced CAD designers who have developed their favorite best practices, but investigation always reveals 50 best practices for every 50 designers.
The C-Level Needs to Lead
Corporate managers must exert more leadership to solve this problem. They need to take a page or two from Toyota’s Production System, and understand that one of the biggest reasons Toyota is doing so well today is because it standardized its complete operation. This allows Toyota to then continuously improve its operations and enables its people to work together more effectively.
Also, Delphi Steering developed and standardized its design methodology. Delphi now makes its design methodology available to third parties in the form of training and certification programs, much like how Six Sigma methodology is available from different service providers worldwide.
Another strategy for improving collaboration is making the data more broadly available and useful to more people in the organization. New formats are now available that greatly expand the availability of 3D product data throughout the extended engineering factory, value chain, and supply chain.
In Part 2 of this article we will take a look at some of the new formats and individual solutions that unlock collaboration throughout the enterprise and extended enterprise. The solutions and formats we intend to discuss will come from such companies as Adobe Systems, Autodesk, Dassault Systemes, and UGS Corp.
David Prawel is the founder and president of Longview Advisors Inc., a consulting firm serving manufacturers. His career spans 25 years in high-tech businesses and he has published many articles covering 3D MCAD, product design, and related subjects. Wolfgang Geist is general manager of Conweb GmbH, a European provider of products, solutions, and services aimed at the reuse and downstream application of heterogeneous 3D product data. Send your comments about this article through e-mail by clicking here. Please reference “Lightweight Data,” July 2006” in your message.
Company Information
Actify, Inc.
San Francisco, CA
Daratech Inc.
Cambridge, MA
Delphi Corp.
Troy, MI
Informative Graphics Corp.
Phoenix, AZ
Subscribe to our FREE magazine,
FREE email newsletters or both!Latest News
About the Author

DE’s editors contribute news and new product announcements to Digital Engineering.
Press releases may be sent to them via [email protected].

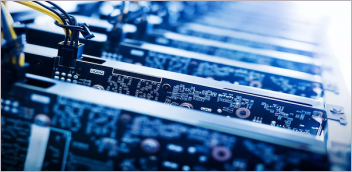
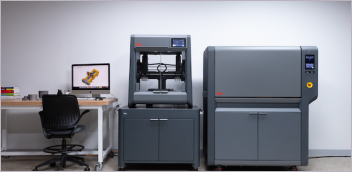
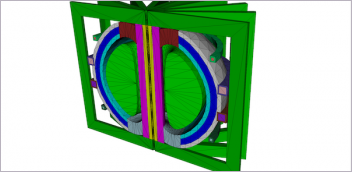