Affordable Options: Ceramics & 3D Printing
University of Washington's homemade ceramics mix democratizes 3D printing and offers extended range of printable objects.
Latest News
July 27, 2009
By Susan Smith
![]() After printing, loose powder falls away from the printed ceramic objects. These cups were created using the University of Washington recipe, which costs about three percent as much as commercial 3D printing powders. Images courtesy of M. Ganter / University of Washington |
Making do with less has become a recurrent theme that has surfaced as a result of the global economy. Yet University of Washington (UW) mechanical engineering professor and longtime practitioner of 3D printing, Mark Ganter, has been addressing the high cost of commercial materials and experimenting with his own material formulas for some time now.
Five years ago, with the help of his graduate students, he developed a home-brewed material, using a mix of artists’ ceramic powder blended with sugar and maltodextrin, a food additive. “Normally ]3D printing] supplies cost $30 to $50 a pound. Our materials cost less than a dollar a pound,” says Ganter.
For the past 15 years, Ganter has taught an engineering course that introduces students to 3D printing, attracting not only engineering students but those from art and architecture as well.
“When powders are $30 a pound, I can’t let students try something new or experimental,” Ganter said. “But when it’s $1 a pound, I don’t care. I encourage them to try new things.”
The search for a low-cost alternative for creating complex shapes began four years ago when the Solheim Rapid Manufacturing Laboratory group at UW got a grant from the National Science Foundation to print custom dental implants. Ben Utela, a former doctoral student, began to experiment with different materials and processes and published papers describing how to 3D print in given materials.
The research was spurred by cost realities: lab fees are high and somewhat intractable, but materials can be made more cheaply. The lab can use $4,000 of materials per quarter, Ganter said. In the 15 years of the lab’s operation, bills for materials easily overshadow the purchase price of one printer of approximately $20,000.
The UW group has published results and formulas using three different ceramic powders, now sold by the 50-pound bag at local pottery and craft stores. Users can purchase most other supplies at local restaurant supply stores or grocery stores.
“We can fix our own printers, so we’re not worried,” Ganter said. “And most of our materials are so close to what’s being used that the risk of damaging the machine is small. In the worst-case scenario, if we can’t fix the machine ourselves, we would have to pay for a repair.”
![]() These vertabrae models show the level of detail achieved using the ceramic powder. |
From this work, ceramic (i.e., alumina) printing derived. At this time, 3D printing was already possible for engineering-grade ceramics with high firing temperatures, yet artist-grade ceramics fire at lower temperatures. Suppliers do not provide art-ceramic powder as an option, said Ganter.
The actual experimental process involved selecting a ceramic powder and choosing appropriate additives, plus settling on a printing fluid. The single powder-and-binder combination was decided upon by graduate student Ian Blanch.
Students had been experimenting with casting metal into a low fire (cone 06) slip available from Seattle Pottery Supply, locally known as Xtra-White. The printer was loaded with this Xtra-White slip powder, and an existing alcohol-water solution was used as binder. After some rather unsuccessful first starts, the group decided on a combination of PVA (polyvinyl alcohol) and extra-fine sugar as powder additives with the Xtra-White slip powder, along with an alcohol-water binder.
The resulting test runs produced parts that could be successfully removed from the printer bed and depowdered. Once the parameters for printing and firing had been established, the group moved on to a higher firing slip, Redart TerraCotta. Using the same powder additives and 3DP setup, they printed terra cotta clay, which worked without a glitch.
Other tests included experimenting with firing temperature and how it affects shrinkage and flexural strength. The resulting fired objects are quite light and porous, and experiments continue in postprocessing to reduce porosity with infiltration processes. Other experiments include applying glazes. For their 3D printing process, UW uses any CAD package that can generate an STL file.
Ganter wants the material recipes distributed for free so that students and others will be able to expand their range of materials and creative print possibilities.
More Info:
Solheim Rapid Manufacturing Laboratory
University of Washington
Seattle, WA
Susan Smith is a contributing editor for Desktop Engineering magazine. She has been an editor and writer for the technology industry for more than 15 years and resides in Santa Fe, NM. Send e-mail about this article to [email protected].
Subscribe to our FREE magazine,
FREE email newsletters or both!Latest News
About the Author

DE’s editors contribute news and new product announcements to Digital Engineering.
Press releases may be sent to them via [email protected].
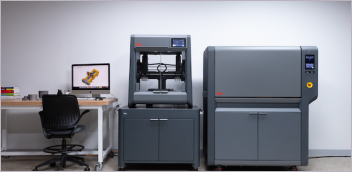
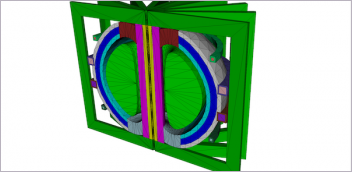
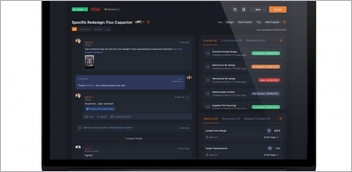
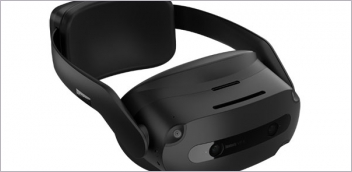