Latest News
March 1, 2005
By Louise Elliott
The automotive industry relies on a variety of analysis tools to avoidbuilding a prohibitively large number of prototypes for physicaltestingeach of which may take months to build at costs up to $200,000.Constantly under pressure to release new models frequently, as well asto provide good handling, comfort, and safety, automotive manufacturerstry to reduce the amount of time spent on any particular analysis andto perform as many of them as possible early in the design process.
More powerful computers along with easier to use, smarter software nowhelp manufacturers save time by getting design engineers involved insimulation early in the gameaided by dedicated analysts who used toperform analysis only at the end of the design cycle. Both designersand analysts also use tools such as motion simulation to do parts ofcomplex studies and to provide data for loads that can be applied tofinite element analysis (FEA), acoustic, and related analyses. Motionsimulation models have a tiny fraction of the number of degrees offreedom (DOF) involved in FEA. As each DOF represents a specificequation that has to be solved simultaneously with all the others, thefewer the DOF the shorter the analysis time.
Two images of the US Army’s Family of MediumTactical Vehicles (FMTV) in MSC.ADAMS. The simulation was created byRadian to develop an armor kit, which took less than a year from startto installation. Radian modeled the full vehicle and variouscomponents, including the suspension system to test mobility, braking,lane changes, and cornering, without a physical prototype.
For example, says Cristoph Ortmann, business development director forthe Global Automotive Industry for MSC.Software, “A full finite elementmodel, including acoustic components, for noise, vibration, andharshness (NVH) analysis might possibly contain between six and eightmillion DOF. It makes sense to start with a motion model that will onlyhave a few hundred DOF, and which can be used alone to determinevibration and harshnessand then do the acoustic analysis separately.”
This is a COSMOSMotion screenshot of a car’s steering mechanism for a study ofits orthotropic bushings.
Auto-Motion Alternatives
The acquisition of Mechanical Dynamics by MSC.Software a few years agohas not changed the fact that ADAMS motion simulation software is usedfor the majority of NVH studieswhether as part of the MSC toolkit, oras incorporated into UGS’ Scenario analysis interface. The results ofMSC.ADAMS simulations can be used to provide loads for FE-basedflexible body studies and additional analyses by many different FEAsystems.LMS CAE’s Virtual.Lab Motion, which now incorporates all of the motionsimulation capabilities of its original DADS program, in associationwith acoustic and fatigue analysis tools, tends to be used mostly forpower-train and drive-train analyses, as well as durability/fatiguestudies (see “FEA in Motion,” DE, January 2005).
COSMOSMotion from the SRAC division of SolidWorks Corp. uses what usedto be called Dynamic Designer, a design engineering subset of ADAMS toperform rigid body motion studies inside SolidWorks.
An auto on a test stand modeled inMSC.ADAMS. The simulation shows the exhaust and steering systems beingstudied by engineers as part of an acoustic analysis and NVH simulation.
Putting Design Engineers into Motion
“In car development, engineers decide the configuration and then builda template model of the basic configuration,” says Richard Bush,product marketing manager, NX Simulation for UGS. “With this frameworkin place, the designer can run his own analyses and motion simulationfor a number of factors, including clearance tests for doors andwindows, pin forces for hinges and other moving parts, and also get theloads required for stress analyses. If he had to wait for an analyst,it would waste a lot of time.”
Such studies run by design engineers are not meant for finalvalidation, Bush says, but rather for qualitative purposes throughoutthe design cycle. “UGS OEMs ADAMS motion within the Scenario interface,where users also have access to NX Nastran and I-deas analysis modulesfor such purposes as NVH studies, and generating flexible body data.”
Bush also points out that tests of subsystems and geometric sections,such as the examples mentioned above, shorten the design cycle andbring pretested overall geometry into play when crash testing takesplace late in the design cycle. “Precrash analysis mostly means usingpast knowledge, to make sure few surprises will occur in crashanalysis,” Bush says. “Early studies let you change a lot of thedesign, but those done at the end leave no more than 20% wiggle room.”
Scott Ziemba, CAE product manager for DASI Solutions(dasi-solutions.com), a SolidWorks reseller in the Detroit area, saysthat automotive manufacturers use COSMOSMotion to study rotating parts,including transmission gears, high-speed spindles, and vibration.Although the program uses rigid body motion only, it can communicatewith ADAMS for more complex motion studies.
Visteon Steering Systems (visteon.com) has been a customer since 2000,and its experience underscores the value of bringing motion simulationand analysis to design engineers. John Crossman, engineering managersays, “In the past, we would have a two-hour meeting to define thecustomer concerns and wants, spend several hours processing work ordersto our CAD and CAE departments, and three weeks later provide the firstiteration of the analysis results at a
customer review. The combination of SolidWorks, COSMOSMotion, andCOSMOSWorks make ‘real-time’ engineering possible. By doing the workthis way, the customer leaves the first meeting with results. As itstands today, we have cut our iterative analysis cycle time down fromthree weeks to approximately four days. Additionally, the work is doneby a single engineer, rather than a coordinated effort between anengineer, designer, and CAE analyst.”
NVH and Ride Comfort
Whether or not a particular customer will buy a particular car oftendepends on whether the driver finds the ride comfortable. The “H” inNVH refers to harshness of ride. Ortmann of MSC.Software says thatexisting virtual prototypes developed for handling-related simulationscan be used for predictive NVH engineering, and for ride and comfortsimulation. “The MSC.ADAMS/Car Ride system simulates ride and comfortearly in the design process. It uses a handling model together with itsdatabase implemented for low frequency (from 10 to 15 Hz) vehicledynamics. The low frequency corresponds to handling issues, but it canbe updated to be representative for ride and comfort engineering, forwhich response must be reliable up to 90-100 Hz,” he says.
| ||
|
By swapping the rigid bodies in the virtual prototype with FE-basedflexible bodies that represent the same componentssuch as suspensionarms, exhaust systems, etc.engineers can improve the reliability ofsimulation at the higher frequencies.
Manufacturers for various segments of the US military have used LMSproducts for truck and other vehicle studies. These include OEMs andmanufacturers of mechanisms such as door latches and flip-open doorsfor interior compartments. “Most automotive users perform power-trainand drive-train studies,” says Jason Wayman, senior account executivefor LMS North America. “These simulate crankshaft and block interactionto see where the energy they produce goes, and how it affects the bodystructure regarding vibration and acoustics in particular. Of course,these factors tie into NVH. The same data can be used to computefatigue in components as well as providing input for stress and strainanalysis.”
Crash is a logical extension of such simulations, says Wayman. “If wecan find out the initial conditions and orientation of the vehicle frommotion simulation, it should simplify crash analysis.”
Clearly, the range of possible automotive system and performancecharacteristics is almost limitless. Each analysis provides informationfor the nextwhether geared to the comfort of the ride, the handling ofthe vehicle, or whether it will survive impact.
Tier One automotive supplier ArvinMeritor (arvinmeritor.com) verifiesits MSC.Software computer analyses with field tests performed with aninstrument-carrying truck. Usually the computer model comes within5%-10% of analysis results. The company uses a model initially preparedfor crash analysis or handling for NVH and fatigue analysis, andreports that by performing such a full range of analyses, it can save agreat deal of time and between $100,000 and $1,000,000 per system.
Contributing Editor Louise Elliott is a freelance writer based inCalifornia. Offer Louise your feedback on this article through [email protected].
Companies mentioned in this article:
COSMOS/SolidWorks Corp.
Los Angeles, CA
cosmosm.com
LMS International
Troy, MI
lmsintl.com
MSC.Software Corp.
Santa Ana, CA
mscsoftware.com
UGS Corp.
Plano, TX
ugs.com
Subscribe to our FREE magazine,
FREE email newsletters or both!Latest News
About the Author

DE’s editors contribute news and new product announcements to Digital Engineering.
Press releases may be sent to them via [email protected].
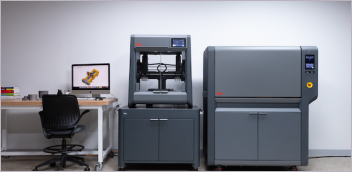
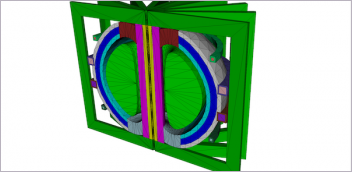
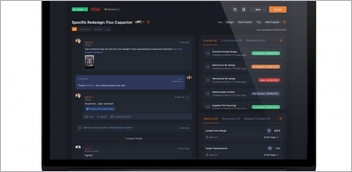
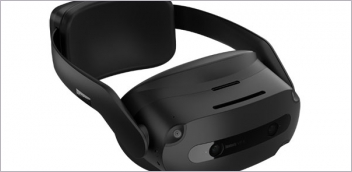