Latest News
June 1, 2008
By Al Bunshaft
![]() Al Bunshaft IBM PLM Solutions |
Win or lose. These are the twosimple outcomes for companiesthat want to sell to customersaround the world. Inrecent years, winners have been companiesthat value and implement concepts of flexibility,agility, and perfectionism. They developa set of best practices and processesthat integrate product planning, design,and manufacturing into the core business issues of an enterprise.
Product lifecycle management (PLM),historically a set of software applicationsfor designing a product, is no longer a topicreserved for product designers and engineers.
Companies can effectively manageproduct innovation by following a setof proven models in the PLM space. From concept to customer satisfaction, managingproduct lifecycles is becoming a boardroomdiscussion for companies planninggrowth.
While cost reduction has been the impetusfor optimizing a dispersed and globalsupply chain, quality and safety remainparamount. Other concerns, such as the environmentalimpact of manufacturing, haveled to governmental regulations. Managingall these complex pieces effectively dictatesthe need for an integrated practice tomanage PLM. Companies remain exposedto costly mistakes unless they have the toolsto establish and monitor product developmentfrom planning to maintenance.
Consider medical devices. Last year theFDA issued 20 recalls of medical devices. Itissued six recalls in 2003 and just three in2001. This upward trend is alarming, reflectingmore than one recall per month involvingproducts like life-saving defibrillatorsand the daily blood-glucose teststrips critical to millions living with diabetes.
While the FDAregulates the safety ofmedical devices, it is the manufacturerswho are responsible for quality as they arein most industry sectors from auto and defenseto retail and consumer goods. And itis the manufacturers who absorb the cost ofthese often-expensive errors.
Small design changes create the samemayhem that recalls do. Changes usuallymake the product better, but at what cost?
How many inventory parts will becomeobsolete? How will customers respond?
Will the product still meet environmentalbenchmarks expected by customers? Inshort, is there more risk than reward inmaking the change? Such questions ariseat every company that is continuously innovating.
The answers can be found in collaborationthat helps businesses makefaster, more precise decisions.
Companies will avail themselves ofthese answers by leveraging all their technologyinvestments. Business intelligencesystems recognize customers’ buying patternsto dictate inventory flows and productenhancements, maintenance systemslinked to user portals automatically generateservice requests or warranty information,inventory management and maintenancesolutions can limit waste andpromote part re-use and recycling, and unifiedcommunications platforms link expertsaround the world to share best practiceswhile avoiding common mistakes. PLM touches all divisions of a company.
Today’s PLM tools go beyond traditionalMCAD, CAM, and CAE products. APLM-savvy organization will weave traditionaldesign-centric PLM systems into acommon enterprise-wide solution to seamlesslylink engineering and business systemsto make information accessible to all key disciplines in the extended enterprise.
Manufacturers who harness their collectiveknowledge with that from suppliers and partners will be tomorrow’s winners.
Al Bunshaft is vice president of IBMProduct LifecycleManagement (PLM) Solutions. Send feedback to [email protected].
Subscribe to our FREE magazine,
FREE email newsletters or both!Latest News
About the Author

DE’s editors contribute news and new product announcements to Digital Engineering.
Press releases may be sent to them via [email protected].
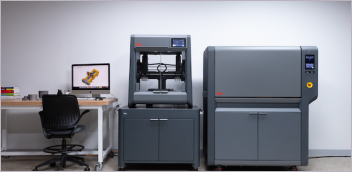
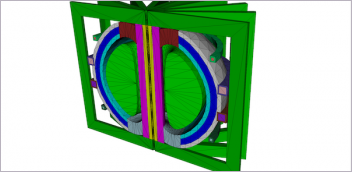
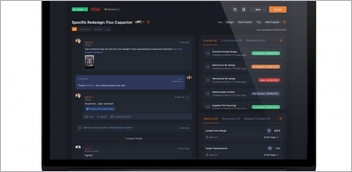
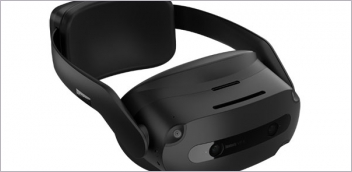