Latest News
July 30, 2010
By DE Editors
A sizeable proportion of the coaxial RF connector business is for custom parts, and the strong competition in this sector means that success relies heavily on a connector vendor’s responsiveness to customer requests. For one manufacturer, San-tron, around 70% of its business is producing custom parts. San-tron will typically design a new connector within three working days, thanks in part to an automated design process using the Concerto high-frequency electromagnetic design software, from Cobham Technical Services.
Requests for custom parts are often driven by a need for improvements in cost or performance, and often both. By using Concerto software, with its built-in automatic parameter optimization program, San-tron is often able to find the best connector geometry in a single simulation-optimization stage. From there, the company typically fabricates a small number of prototypes, based on the optimized design, but with minor mechanical variations. The results of electrical tests on the prototypes allow San-tron to assess the effects of tolerances in manufacture and material properties. The final design is then realized in finished samples for customer evaluation.
The complete design stage of this process is usually performed within three working days. This includes a full three-dimensional simulation and multi-parameter optimization exercise that takes between 30 minutes and a couple of hours, depending on the complexity of the product. Concerto can perform this on a standard office laptop.
Before this design process was introduced, San-tron employed analytic computer software to estimate the VSWR (voltage standing wave ratio) of a proposed connector design. Designing a new connector using this approach typically necessitated three or four physical prototyping iterations.
This approach became impractical as San-tron’s business grew, and as it became involved in higher frequency applications. San-tron designs several hundred connectors every year. Many of these are mechanical variations on connectors in its standard range, and do not require electrical changes. But, in-depth design and analysis of a new concept using Concerto is typically needed for two or more products each month.
One recent Concerto-aided design project involved a panel-mounting connector for operation up to 40 GHz, following a customer request to lower the costs of an existing connector that it used. Concerto’s ability to optimize a design helped San-tron’s Chief Engineer Fred Hull to prototype an idea virtually that reduced the bill of materials from five component parts to four, while still matching performance.
“It would be extremely difficult and expensive to produce a high-frequency connector like this without design automation,” says Fred Hull of San-tron. “I would probably need to machine and test a dozen prototypes before I could lock in a reasonable performance optimum, and that process would be far too slow and too expensive for today’s marketplace. Concerto gives us the means to obtain the optimum geometry in a matter of a couple of hours.”
For more information, visit Cobham Technical Services.
Sources: Press materials received from the company and additional information gleaned from the company’s website.
Subscribe to our FREE magazine,
FREE email newsletters or both!Latest News
About the Author

DE’s editors contribute news and new product announcements to Digital Engineering.
Press releases may be sent to them via [email protected].
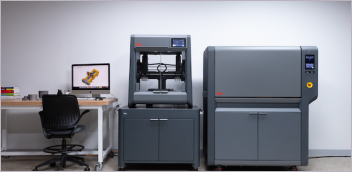
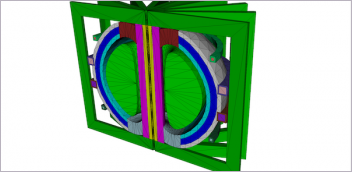
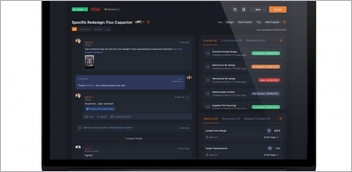
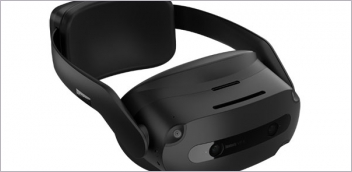