A Mill for Every Desktop
Roland's new MDX-540 SRP desktop machine produces high-resolution models in virtually any prototype material.
Latest News
December 1, 2006
By Mike Hudspeth
There’s nothing like holding a physical prototype in your hand for getting the feel for a product. You can model in 3D all day, but until you actually handle the object, you won’t know how its curves, dimensions, corners and recesses, even its weight will feel. There are so many aspects of a model that have to be experienced by touch to be fully appreciated, and until you have a physical model in hand, you just can’t be sure. So how do you get that model?
For years now the top dog in rapid prototyping (RP) has been stereolithography (STL). It is an additive process where layers of plastic resin are cured, typically with ultraviolet light. There’s also fused deposition modeling (FDM), there’s laminated object modeling (LOM), there are 3D printing technologies, the list goes on and on. But there is just something about good old-fashioned milling that none of those other technologies can surpass.
![]() |
Roland MDX-540 |
> > It may not be as sexy as the Enterprise or as detailed as the Millennium Falcon, but this little freighter model can still show you a few things about the Roland MDX-540 SRP. Notice the overhang above the front window.
Roland Advanced Systems has a new 3D mill called the MDX-540 SRP (see photo below). It is billed as a desktop unit that is suitable for the office environment. Unlike the aforementioned RP systems, this one uses a subtractive technology. Subtractive rapid prototyping (SRP) starts with a block of the material you want the final model to be made of and removes what isn’t part of your model. That’s right, you get to choose the material. But don’t go crazy—steel is not an option.
Materials that will work include wax, all kinds of plastics, tooling board, foam, even aluminum, brass, and copper. Using actual engineering materials means more accurate prototype testing. STL systems absorb moisture and can warp in humid conditions. FDM parts are far more porous than an injection-molded or machined part. Because you can machine non-ferrous metals with the MDX-540 SRP you can create actual tooling. It would be ideal in situations using aluminum molds for short-run tooling. You can even create EDM electrodes.
![]() |
Roland MDX-540 |
< < The Roland MDX-540 SRP is a fairly compact yet powerful computer-controlled rapid-prototyping machine.
I put together a fun little model of a toy space freighter to illustrate the capabilities of the MDX-540 SRP (see the opening image above). This is what I found.
Finish Precision and Price
Resolution has always been an issue for additive RP modelers. The MDX-540 SRP will raise your expectations. You’re not going to believe the surface finish. There is no stair-stepping like you find in additive systems. You get silky-smooth finishes like—well you get the idea. To get a finish like this on an additive machine, you’ll have to do a lot of secondary finishing work. Sanding, filling, sanding again, all before you’re ready to start thinking about painting. That will take time—lots of it. Not that there isn’t secondary work with the MDX-540 SRP.
![]() |
Roland MDX-540 |
Figure 1: Notice the surface finish on this part. You’re not going to get that from an additive system without shelling out some big bucks.
There are small supports around the periphery of the finished model that you’ll have to take care of, but they are minimal (see figure 1, above). You gotta hold onto it somehow. While the control software can maintain a resolution of 0.00004, the actual model’s best resolution tops out somewhere around 0.002. The smaller the part, the more important this becomes, and the brighter the MDX-540 SRP shines. It uses a standard eighth-inch shank cutter so the bits you can use are readily available. The machine is used by some jewelry companies for cutting in fine detail. Some of their wax cutters go down to 0.003 diameter. If that’s too big for what you do, you’ve probably already skipped over the additive systems.
Another great advantage the MDX-540 SRP has over most of the other rapid prototyping systems on the market is price. The MDX-540 starts at around $19,000 for the base model. You can then start adding options from there. (More about the options later.) The maximum model size you can build is 19.68 inches x 15.74 inches x 6.10 inches. That’s bigger than most other rapid prototyping machines near its price range.
Undercuts Uncut and Flying Chips
Undercuts aren’t an issue for additive RP machines. That’s where they shine. But subtractive RP modelers are limited in the same way a standard machine shop would be. If you look at the front of my little space toy, you’ll notice the window has an overhang. It’s small but I wanted to see what the MDX-540 SRP would do with it. The way the model was set up was as a two-sided job. When the software came to the top, it was basically looking straight down on it and naturally didn’t even see the undercut. It merely cut out a notch. If you absolutely have to have an undercut, you will need to get more creative with it. You could perhaps model in an opening that can be milled from the other side. You would end up with the same sort of thing that you would see when you went to build an injection mold.
![]() |
Roland MDX-540 |
Figure 2: I left several sharp edges in the computer model. The MDX-540 SRP of necessity cut the edges with a radius.
Interior sharp edges require special attention. Because the cutter used for this sample was a ball-end mill, the edges ended up with small radii on the inside (see figure 2, above). Outside edges could be cut directly and made absolutely sharp. Of course you could always use a flat-end mill to get some of the inside edges.
I would think flying chips would be a problem in an office environment, especially using smaller cutters. There is an optional dust cover available to keep the mess to a minimum. Optional? If this machine were used in a closed room like a machine shop I could see maybe not needing a cover. But who would want it in the cube next to them throwing dust and junk into the air to be sucked into their PC’s fans? Roland might want to think about making that cover standard equipment.
Accessories Complete the Picture
There is a 4th axis “Rotisserie” option (figure 3, below) that makes for more automated production and faster speeds. It goes for $4995 in addition to main machine. When one side is finished it can automatically turn the model over and mill another. It can also be used as a lathe, continuously shaping your model all the way around. The automatic tool changer ($9995) means the MDX-540 SRP can operate unattended. It will finish working with one tool and go grab the next until the piece is complete. It can hold up to four different tools. You tell the software what tools you‘re loading into the changer and it will choose the appropriate one for the job. Obviously, you would want to use a bigger cutter to rough cut the model and go down to a finer bit for detail work and final finishing.
![]() |
Roland MDX-540 |
Figure 3: The rotary axis option gives you a lot of additional capability. It also cuts down your maximum build size somewhat.
A hand-held controller comes standard with the MDX-540, and it lets you control the machine from a discrete distance. Though the MDX -540 SRP is safe enough for an office environment, if you didn’t buy the optional dust cover you might find yourself covered in flying chips. You can also control things from your computer through the included control software (see figure 4, below). It lets you generate tool paths, scale the model, select finish levels, etc.
Compact and Efficient
The relatively small size of the MDX-540 SRP means you could roll the unit around to different locations to share the wealth. (I don’t know about you, but in my office, once a two hundred plus pound machine comes through the door it pretty much stays put.) The whole unit is somewhat less than three cubic feet in size and weighs between 225 and 250 lbs. Noise will be a minor consideration. Just sitting there with the power on the MDX-540 SRP is whisper quiet at 40 decibels. When it’s running, that number climbs to around 65db. That’s the equivalent of a casual chat with someone from a foot away. The MDX-540 SRP runs off of a standard 110 VAC, 7-Amp outlet. Just to put things in the proper perspective, that’s less power than your average oven uses to bake cookies.
|
Roland MDX-540 |
Figure 4: The software interface is very simple to navigate and gives you enough capability to cut all kinds of models.
Build time for each of my pieces (which includes programming time) was a little under 17 hours. They were just over six inches long and three-quarters of an inch tall. Most RP machines would fall into the same ballpark.
I was so impressed with the Roland MDX-540 SRP that I forwarded information on to my company’s decision makers to see if we would be interested in buying one. I highly recommend you check the MDX-540 SRP out for yourself.
Mike Hudspeth is a senior designer for a global medical company and has been using a wide range of CAD products for 20 years. He, his wife, two daughters, and their cats live outside of St. Louis, MO. Send your comments about this article through e-mail by clicking here. Please reference “Roland MDX-540 Review, December 2006” in your message.
Roland MDX-540 SRP
Roland ASD
Lake Forest, CA
Subscribe to our FREE magazine,
FREE email newsletters or both!Latest News
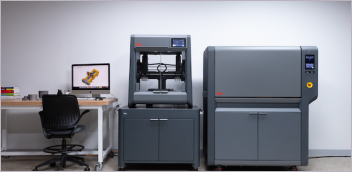
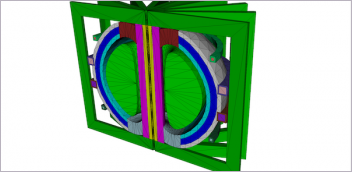
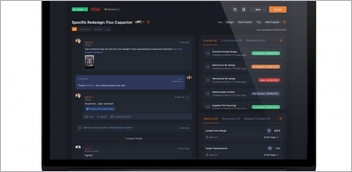
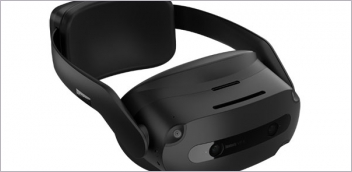