A Model of Efficiency
Top manufacturers who regularly meet cost, revenue, launch date, and quality goals, require fewer physical prototypes than their competitors.
Latest News
August 30, 2007
By Amy Bunszel
Cut one physical model from your development cycle and you can save thousands of dollars — possibly millions — on product development. That might seem like a flippant remark, but this worthwhile goal could be the answer to a serious question faced by product design and R&D managers at every budget review.
![]() Marine Advanced Research used Autodesk Inventor to prototype the Proteus spider boat, a catamaran that glides on the water’s surface.The digital prototype ensured that springs in the frame would allow it to bend properly as the twin hulls skim across the water. |
In “The Digital Product Development Benchmark Report” (March 2007), research firm Aberdeen Group reported that top-performing manufacturers — those that met their revenue, cost, launch date, and quality targets for the overwhelming majority of their products — produced an average of 5.1 physical prototypes as compared to 6.1 for the rest of the industry. As a result, these companies reduced time to market anywhere from several weeks to more than three months, and saved anywhere from $7,600 to more than $1 million, depending on product complexity.
How did these manufacturers trim one physical prototype out of the development cycle? The Aberdeen report reveals several answers. More top manufacturers ran simulations in every phase of development than average performers. All the best performers ran tests in the design phase and 88 percent gauged performance in the test phase. Once designs were released to manufacturing, 72 percent of best performers continued to simulate performance, while little more than half of average manufacturers did so.
What’s more, 22 percent of top performers used digital prototypes for simulations. As the Aberdeen report shows, that’s a subtle distinction from solid models, and it takes more than 3D modeling to engage in digital prototyping.
![]() No physical prototype was required for Marin Bike’s Quad XC bike. The frame and its swingarm were designed and calibrated in Autodesk Inventor software for precise interaction when in motion. |
Building a Conduit for Efficiency
For one thing, best-in-class firms’ engineering and manufacturing departments are more likely to communicate electronically. Top performers are 34 percent more likely to deliver production documentation electronically. Also, 33 percent of top performers notify stakeholders electronically, i.e., with electronic change order and design release forms (not just e-mail), vs. 20 percent of average performers and 23 percent of laggards.
Rather than rely on a paper trail, top performers create “digital pipelines” that carry information freely in both directions throughout all the major phases of design and production. This affords instant electronic access to design and manufacturing information and feedback among all teams.
The flow of digital information also helps manufacturers take advantage of a closed-loop cycle of efficiency. Take change orders: While Aberdeen found that the time to make changes didn’t vary, a manufacturer’s ability to address design issues upfront meant fewer change orders downstream. And that results in less overall time spent on revising a product.
Connecting Major Functions
With a digital pipeline in place, though, there is still potential for bottlenecks because the conventional ways that designs are conceived and communicated at the ideation, engineering, and production phases of manufacturing can interrupt the flow of information. Top manufacturers take steps to clear those obstacles in each of these phases.
![]() For Marin Bikes, virtual prototyping has dramatically increased the rate at which it introduces new models. Since the company started using digital prototyping software two years ago, it’s gone from releasing three new bikes a year to as many as 24.The frame design process that once involved up to six physical prototypes now requires only one or two. |
White boards and paper are still prevalent when products are first conceived. But data on paper isn’t easily integrated into spreadsheet, word processing or other applications for capturing the information that precedes form and substance. Industrial designers often turn to clay models for the tactile experience of their ideas. It is difficult to convert that analog information into data that can be used by others who will create the product’s structure and systems.
Even when industrial designers use digital styling and visualization tools, the data may or may not be compatible with the applications used by product engineers. Aberdeen found that best-in-class manufacturers documented engineering deliverables electronically and early on, making them “portable” across divisions. Manufacturers can take steps to start and sustain the flow of information between ideation and engineering by factoring software interoperability into their selection of tools for ideation, or through some other means of integration.
In addition to grappling with incompatible data from the industrial design team, design engineers often must use tools that aren’t quite suited to the task. That’s because most solid-modeling software focuses on 3D geometry; form and fit, but not function. It’s an important distinction: Unable to model the physics that impact motion, many engineers tackle these issues with one set of tools and then work with CAD specialists to translate their functional solutions into geometry.
The research shows that successful manufacturers equip their engineers with applications that don’t require them to adapt their problem solving to suit their tools. They use software that automates model creation and then tests designs throughout development. These simulations make it possible to replace physical prototypes with digital prototypes to assess performance. That, in turn, enables engineers to spend time — time they might have spent on making physical prototypes — on releasing the design early or further enhancing the product’s performance.
This is where solutions such as Autodesk Inventor come in, helping to address this disconnect and other issues that follow. Autodesk Inventor provides a foundation for digital prototyping with 3D virtual models that are complete and accurate, enabling engineers to validate design and engineering data as they work. These 3D digital prototypes eliminate the need for multiple physical models and help reduce costly engineering changes that often are discovered after a design is sent to manufacturing.
Here, the Aberdeen report shows that software-generated models benefit manufacturing as well. Once designs reach manufacturing, production teams typically rely on e-mail or paper communication to clarify questions with design teams and use physical prototypes for insight. Simply capturing more information digitally at this point and making it available eases a typical logjam.
![]() |
Aberdeen found that the benefits of model-creation software flow both ways. Not only does manufacturing move more smoothly, but industrial engineers take advantage of production teams’ insight into manufacturability. It’s no wonder that top performers are four times more likely to use design models for manufacturing documentation — and the advanced simulation tools used earlier provide answers to manufacturing-team questions.
Aim for Less and Gain More
What leads best-in-class manufacturers to digital prototyping in the first place? Pressure to develop more products on a dime — that is, both quickly and at lower cost. That goal has prompted more than half of Aberdeen’s study group to strive toward increasing engineering efficiency and throughput, and streamline product development processes.
Digital prototyping similar to that enabled by Autodesk Inventor is one such step toward efficiency. It also reflects the premise that digital documentation can be the “source of truth” for manufacturing, a philosophical and cultural shift that Aberdeen found to be a major challenge for half of manufacturers surveyed. The good news is that the path to digital prototyping is paved with solid changes in process and technology that can help manufacturers formalize a shift in organizational mindset and perhaps save significant time and money in the bargain.
For More Information:
Aberdeen Group
Boston, MA
aberdeen.com
Autodesk
San Rafael, CA
autodesk.com
Amy Bunszel is director of the Inventor product line for Autodesk Manufacturing Solutions. To send comments about this article, you can send an e-mail to DE-Editorsmailto:[email protected].
Subscribe to our FREE magazine,
FREE email newsletters or both!Latest News
About the Author

DE’s editors contribute news and new product announcements to Digital Engineering.
Press releases may be sent to them via [email protected].
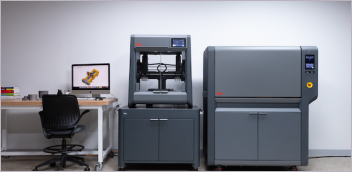
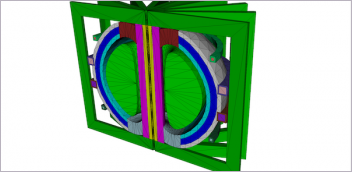
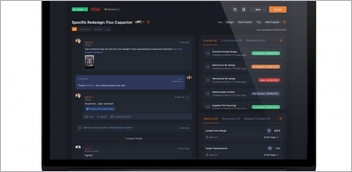
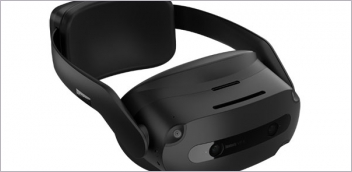