Latest News
November 1, 2010
By Mike Hudspeth
There was a time when flying was an adventure full of fun and excitement. You could get on a plane and expect a certain amount of prestige. It wasn’t something people did every day. Not anymore.
![]() In 2006, Gulfstream partnered with NASA to test their “Quiet Spike.” The thought was to push the shockwave far out in front of the plane. |
Nowadays we are herded into coach (because the company won’t spring for any better) and left to sit in uncomfortable seats while very nice flight attendants try to make the best of an unpleasant few hours. Flying across the country is one thing, but try going to Europe or Asia. Many people think planes don’t need a lounge, but if you’ve ever spent more than eight hours aboard a plane you can appreciate the need. So how do we fix our flying dilemma? Well, we could build bigger planes. That’s what Boeing and Airbus are doing. But that is only going to mean more people on the same multi-hour flight. No, we need a different solution. Go faster then. There are companies working on that too. Remember the Concorde? One problem has been that as we increase the speed of our aircraft, we create sonic booms. If we could find a way to reduce or eliminate those, we might see a new era in air travel.
![]() These images show the changes in off-body pressures around a wing by altering its shape. At the top are pressures on the surface of the wing. In the middle is a graph of off-body pressure below the wing. On the bottom are off-body pressures surrounding the wing. The image on the left shows before the changes. The image on the right shows the wing after its shape has been changed. (Images courtesy of Tecplot, Inc. Test case data provided by Optimal Solutions Software, LLC.) |
The “Federales” have all but outlawed commercial supersonic air travel over the continental United States back in the 1970s because people don’t like sonic booms disrupting their lives. That means we are limited to flying slower than the speed of sound (761 mph) to get where we’re going. So how do we have the best of both worlds—going faster without rattling everyone on the ground?
NASA and several aerospace companies are on a grand quest to create a supersonic plane without a sonic boom. A lofty goal to be sure (pun intended). They have researched such things as wing shape and fuselage design. They found that the longer and pointier you make a plane’s fuselage, the lower the turbulence around the plane. They flew several prototypes to test their theories. See figure 1. As technology advances, more and more powerful tools are brought to bear on the problem. Computational fluid dynamics (CFD) has been around for many years. It examines the flow of a liquid around an obstacle. In the ’60s it was all done by hand (with slide rules) on paper. Then, they progressed to 2D software. It was faster and more accurate, but the problem was much too complex to solve that way. They needed to go 3D. One company that is involved in the quest is Tecplot, makers of Tecplot 360 software. They have studied the problem from new and more complex angles.
![]() This image shows a shock wave coming off the surface of a delta wing moving at supersonic speeds. (Image courtesy of Tecplot.) |
Liquid Air
Air is basically a fluid. It flows and eddies much like water. To see what that’s like, just look at a wind tunnel. This is where aerodynamic studies have traditionally been done. The process is simple. Create a model of your plane, put it up on a stick, blow high-speed air at it, and for some fun, add smoke. (We’ve all seen those car commercials.) The problem with this approach is that you can really influence or destroy your results if you’re not careful. Your model’s accuracy has to be spot on. Any rough surfaces on the model will blow your drag numbers. The scale of the model has to be just right. The pylon the model sits on can introduce its own effects (something a real plane wouldn’t do). Even the wind tunnel walls can make a big difference.
What CFD does is similar to a wind tunnel, but it’s all done inside the computer. It brings some very definite advantages to the table. You don’t have to have a pylon. Your model can truly float in the air. You can simulate any speed you want, without limit. If you see something interesting, you can run it again and again, varying the numbers to “zero in” on the results.
“Computational Fluid Dynamics is widely used in any industry that involves fluid flow problems,” says Tecplot CEO Mike Peery. “This includes aerospace and defense, shipping, turbines and engines, piping, air conditioning, medicine, environmental (rivers, dams, estuaries, glaciers), weather forecasting, climate modeling, oil and gas, etc. Tecplot has a case studies page on our website that showcases a number of different industry applications. Computational fluid dynamics’ roots are in defense and aerospace, having first been used in the Manhattan Project primarily to study blast wave pressures.”
If you’ve used mold flow analysis, you’ve used CFD.
Until recently, CFD software could give you questionable results. It’s like FEA software was in its early days. “Garbage in/garbage out,” explains Peery. You had to know what you were doing. The casual user would seldom get reliable results. You needed an expert.
Bothersome Booms What exactly is a sonic boom and why does it happen? Put simply, when a vehicle (even a car or bicycle) moves, it must displace the air in front of it to the space around and behind it. As a plane flies, the air spreads out around it and compresses in front of it. As the plane goes faster, it exceeds the speed that the air can easily get out of the way. The air stacks up on itself and forms waves around the vehicle. The air forms a cone behind the plane. These waves are really just rapid pressure changes. When a plane flies over your house, its shockwave will follow and you will experience it as a very sudden rise then fall off of air pressure, followed by another rise as the displaced air tries to fill in the low-pressure zone. These pressure changes can trip car alarms, break windows, annoy neighbors, etc. Why are they called sonic booms? Because, as we all know, sound is merely vibration. If the air vibrates, a sound is heard. As the pressure waves change from average to high to low and back to high, all that vibration makes a deep and powerful sound. |
“The accuracy of CFD depends upon many variables: the difficulty of the flow, the computer resources available, and the physics models that are being used. It is extremely easy to be accurate if you’re looking at lift, but drag is more difficult.”
Nowadays, the software is much easier to use. Tecplot uses its software in conjunction with Sculptor, from Optimal Solutions Software). Sculptor takes a 3D model and deforms it to simulate all kinds of conditions (see my reviews of Sculptor and Back2CAD in the November 2009 DE). It’s a tool for shape optimization. CFD can save you a lot of money in testing.
“CFD replaces lab experiments,” says Peery. “It can replace or minimize the use of wind tunnels, water tunnels, lab set-ups, and models. Today, CFD is on equal footing with experiments, but you typically will need some experimental data (just less of it) and you generally want to compare or ‘spot check’ your CFD data against your experimental data to verify that it’s right.
“What CFD does do better than physical experiments,” continues Peery, “is that it gives you a detailed look at what’s going on in the flow. It is much, much easier to look at velocity, temperature and pressure with CFD. It is also easier to identify separations and vortices with CFD than with physical experiments.” See figure 2.
Aerospace companies aren’t throwing away their wind tunnels just yet though. There’s always a danger in relying on computer simulation if you don’t understand the problem or the data being used, Peery says. Computer simulation is one component of product design. Products and designs still require extensive testing before being released to the public.
The Boomless Boon
So what would be the impact of “boomless” supersonic jets?
“The ability to reduce sonic booms can pave the way for new business-class supersonic jets and help lift the FAA ban on overland supersonic travel for civil aircraft,” Peery says. “It would also help minimize disruptions on the ground caused by military jets traveling at supersonic speed.”
Think 2½ hour flights from New York to Los Angeles or 6 hours to Tokyo. Challenges include the need for more computer resources, speed, and bigger data sets. These are challenges that can be overcome. There are two conditions we’ll need to see for supersonic cruising: aerodynamic control when transitioning to and from supersonic speeds, and regulatory cooperation. Ultimately then, it’ll be up to the researchers and engineers. All they have to do is find the optimum geometry to reshape not only the shockwaves, but the flying world itself.
More Info:
Tecplot
Mike Hudspeth, IDSA, is an industrial designer, illustrator, and author who has been using a wide range of CAD and design products for more than 20 years. He is DE’s expert in ID, design, rapid prototyping, and surfacing and solid modeling. Send him an e-mail about this article to [email protected].
Subscribe to our FREE magazine,
FREE email newsletters or both!Latest News
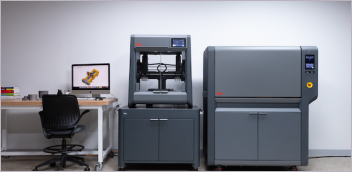
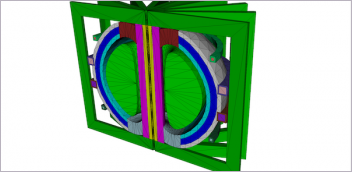
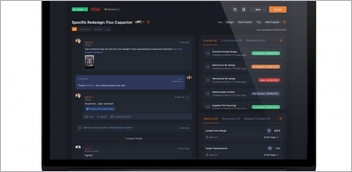
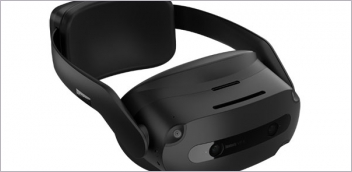