Add Value with Methodology, Part II
Standardized design methodologies improve CAD and CAM on-time performance, leadingto greater innovation and improved profits.
Latest News
December 1, 2004
By Gary Patelski and Jeffrey Solash
It was within this context that Delphi Corporation of Troy, Michigan, developedHorizontal Modeling (HM) and Digital Process Design (DPD). The methodologies letengineers break away from traditional vertical feature-based design. In short,without forcing users to change their preferred CAD system, they provide greaterflexibility in design, detailing, creation, and editing of CAD data.

Less Costs in Product and Process Design
HM allows simple editing of features and parameters. Simply put, instead of placingand positioning features to other features, HM places and positions features todatum planes. In this way, the minimum number of feature dependencies is created.Since few, if any, dependencies exist, designers can easily suppress, delete,or change parameters or features. There’s no longer a need to “hack and whack"in other features to make these changes.
DPD further enables users to closely associate process sheets to in-process models.This association makes it possible to reorder or change processes and have theprocess sheets updated instantly. Since original product models are now createdusing HM, engineering change orders affecting the product are automatically transmittedto the process sheets.
Greater Balance and Delivery
The principle behind HM (and DPD) is simple. The great strength of Delphi’s methodlies in a standardized approach to all its projects. We have applied these methodologiesto literally thousands of parts and have developed an approach that works everytime. Since all our designers use the same method, our product development efficiencyhas increased dramatically.
In the past, Delphi’s process designing was accomplished mainly using contractors.Prior to using HM and DPD, a substitute designer would often redesign the productand proceed to make changes after completing a new design. Since adopting HM andDPD, we have brought process and product design functions in house.
At the Delphi Steering facility in Saginaw, Michigan, where HM and DPD were born,the methods resulted in a significant reduction in creation and revision timecompared to traditional methods. But the real savings were realized in the timeneeded to make changes. These days, the division routinely experiences 90 percenttime reductions in editing designs.
In addition to productivity increases, HM and DPD provide another very significantadvantage: any one designer can easily step in and pick up where another leftoff. Now all designers in a group can easily discern the design structure andefficiently make any required changes. The new ability gives team directors moreoptions when balancing workloads, making meeting delivery goals more efficient.
Productivity Studies
In addition to the productivity results discussed in Part I, Delphi conductedseveral studies to measure the productivity of HM and DPD compared to standard3D methods, including the time a given number of designers (both product and process)required when using standard methods versus HM and DPD methods. As shown in thetables to the left, these tests resulted in a 20 percent savings in time dedicatedto product creation and 65 percent in product editing using HM. The savings areeven more dramatic in process design where time spent creating processes was cutin half.
Implementing Success
HM and DPD methods have helped make the life of a CAD supervisor much easier.First, operators are more productive and happier because they do not have to recreatewhole designs to make simple changes. The group, as a whole, delivers better designsthat are easier to edit, and faster than ever before.
Considering all the factors that conspire against efficient CAD/CAM design, HMand DPD are useful tools for removing those barriers to success and to enhancingperformance.
Horizontal Modeling and Digital Process Design are available to manufacturersvia a training and certification program from Delphi Technologies. Gary Patelskiis the engineering systems manager for Information Technology at Delphi Steering.Jeffrey Solash, Ph.D., is the licensing executive for Delphi Technologies. Tocontact either one of them about this article, send e-mail to [email protected].
This is the second in a series of articles about how new methodologies offerbenefits over technology-based innovation. In the first (DE, October 2004), David Prawel and Michael Richardson discussed how global enterprise communicationrepresents the first step in real, integrated PLM.
Product Information
Delphi Technologies
Troy, MI
delphi.com
Subscribe to our FREE magazine,
FREE email newsletters or both!Latest News
About the Author

DE’s editors contribute news and new product announcements to Digital Engineering.
Press releases may be sent to them via [email protected].
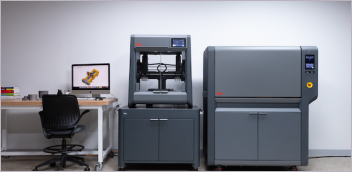
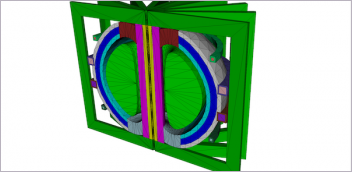
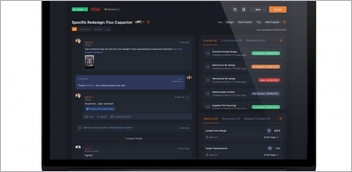
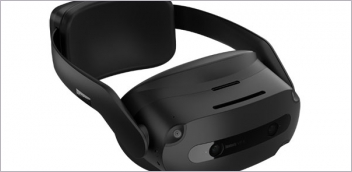