Camshaft Cover for Ilmor 4 Stroke MotoGP Engine
Latest News
May 1, 2008
By CRP Technology
![]() |
CRP has been instrumental in the success of many winning racing teams, from F1 to American Le Mans Series and Paris -Dakar. They offer a high level of support throughout the entire project, including the manufacturing process. What makes this company different are indeed the partnerships they form with the different teams.
The innovative approach to the use of new materials and technology is widely recognised and Ilmor exploited it for the 2007 MotoGP project.
CRP and Ilmor have known each other for a number of years, being both protagonists in F1 world, as well as hi-tech partners and suppliers.
![]() |
The Project
For the development of this MotoGP project Windform XT, a high performance material of CRP’s development and ownership, applied to the Rapid Prototyping, was very useful.
The CAMSHAFT COVER is the structural part that supports the bearing of the camshaft (camshafts seats, the camshaft usually runs at more or less 19000 rpm), directly applied on the 4 stroke 800cc engine head. Inside there is also the lubricant oil.
Average working temperature: 130-140 °C. Every material has a temperature limit over which it is recommended not to go. The recommended limit for Windform XT is 150-160 °C. The limiting factor comes from the thermoplastic base that melts around 180 °C.
At a track like Bahrain or Dubai, even if the ambient temperature is significantly higher than the average at other circuits, the working parameters of the engine (i.e. water and oil temperature) must remain under the limits imposed by the manufacturer, that is usually lower than 150°C. There are usually specific radiators and special aero configurations to ensure a better cooling of the engine.
The improvements this project achieved were:
- Lightness of the engine head cover. Being on top of the engine, each saved gram means better rideability of the bike, allowing to lower the centre of mass (- 31%)
- Reliability
- Fast modifications and production (the possibility to change during the season some features of the part)
- Better cooling of the engine.
The result is a composite part where the different materials have a specific function or structural competence.
Around a main-frame in metal-ceramic matrix, a shell made by carbon fibre filled Windform XT was created. The shell is therefore sintered using high performing material, directly from a mathematic model in a few hours. The main areas of the part (camshaft seats) are made by a series of simple cutting and welding processes, while the prototype shell has the complex shape. In fact, being made by selective laser sintering, any complex shape can be obtained without undercut problems (a typical limit of CNC machining process) or supports (a typical limit of other Rapid Prototyping technologies).
After some dyno test, the first notes coming from Ilmor engineers about the innovative project were:
Ian Watson (Ilmor Senior Designer):
“The engine ran with the cam cover and it was all full speed power run testing: no problem at all: no leaks, no performance difference, no sign of any distress and judged to be a complete success. The bond between the aluminium bearing straps and the WindForm has failed, but I am not too disappointed by the glue failure. We have enough evidence to say that it is possible to consider designing ‘major constructional components’ with both the material and the process.”
Contact Details
Project developed by:
- Ing. Gabriele Tredozi, Former CRP Racing Special Projects Senior Technical Director, former Minardi F1 and Scuderia Toro Rosso Technical Director.
- Ing. Ian Watson, Ilmor Senior Designer
- Ing. Franco Cevolini, CRP Technology Technical Director
Information:
CRP Technology s.r.l.
Via Cesare Della Chiesa, 21
41100 Modena Italy
crptechnology.com
for North America, South America and Australia
Mr. Stewart Davis
(+1) 562-458-4036
[email protected]
for Europe and other countries
+ 39 059 821135
[email protected]
Subscribe to our FREE magazine,
FREE email newsletters or both!Latest News
About the Author

DE’s editors contribute news and new product announcements to Digital Engineering.
Press releases may be sent to them via [email protected].
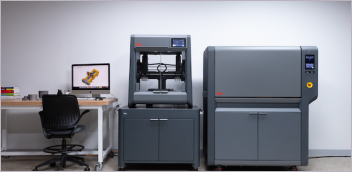
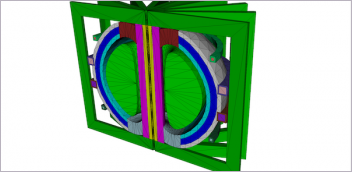
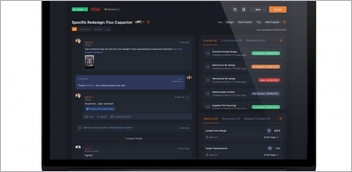
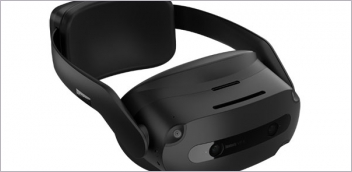