Can PLM Make You Lean? 2 of a Series
Part 2: Lean engineering and manufacturing requires a holistic implementation of PLM aimed at greater process effectiveness.
Latest News
December 1, 2006
By Nancy Rouse-Talley
Successful execution of a lean manufacturing program requires assessing processes, recognizing bottlenecks, and making improvements that not only eliminate holdups but improve efficiency. Simply automating existing processes is not the best way to implement product lifecycle management (PLM) programs. In fact, it might be a recipe for disaster because computerization could simply speed up unproductive processes without improving them, leading to an endless cycle of ineffective changes. (To see Part One of this article, click here.)
Software that manages design data, moves it to the factory, and promotes factory automation should be used once processes are streamlined and improved. Programs such as UGS Corporation’s Teamcenter, PTC’s Windchill, Agile Software Corporation’s PLM products, Centric Software’s Product Intelligence Software, and Dassault Systèmes’ Enovia Virtual Product Lifecycle Management (VPLM), Smarteam, and MatrixOne make it easier to share complex engineering data across the enterprise. Digital manufacturing programs such as UGS’ Tecnomatix and Dassault’s Delmia, on the other hand, help manufacturing engineers validate production processes.
Companies that in the past were primarily concerned with lean manufacturing now also focus on lean product development. Lean methods have formed the foundation of Japanese automobile manufacturer Toyota’s factory processes for more than 50 years, for example, but today the company also uses PLM to perpetuate lean product development processes.
PTC’s Windchill PLM system is used in several ways in Toyota’s powertrain division, for example. A library of templates that represent the best designs for various engine components such as piston rings or cylinders is maintained in a Windchill repository. Toyota’s design processes are also defined in specific workflows, or process descriptions. Workflows ensure that design processes are synchronized and that specific events such as approvals are triggered at the appropriate times.
“The workflows don’t take away design flexibility because they don’t specify how engineers should perform tasks,” says Brian Shepherd, PTC’s division vice-president of product management. “They standardize the approach taken to design, freeing the engineer from having to think about how to prioritize tasks.”
Shepherd said that having easily accessible information available in Windchill also helps Toyota bring its suppliers into the design process earlier. “The Web front-end allows suppliers to connect to the design process and ensures that they have access to the correct information,” adds Shepherd.
Transferring design information efficiently and effectively between engineering and manufacturing in formats that make sense is challenging. In fact, the old term “tossing designs over the wall” between engineering and manufacturing has become an accepted analogy for this outmoded process.
PLM systems can make it easier to communicate design intent, making processes more efficient and lean. The right PLM systems can communicate the bill of material (BOM), design geometry, and various documents directly to the factory.
Dassault Systemes’ recent purchase of MatrixOne illustrates its commitment to supporting manufacturing processes. While Dassault’s Enovia VPLM and Smarteam products focus on managing CAD files and data, the Matrix program can bring together information from diverse programs and expose it to other areas of the enterprise. That’s one reason Matrix is widely used in Tier 1 and 2 automotive and aerospace suppliers that work with multiple CAD formats produced by manufacturers.
> > Dassault’s Robot Task Definition product allows design and optimization of manufacturing workcells. It has a library of more than 700 standard robots for simulated reach analysis and feasibility studies.
“Engineers use mechanical and electrical CAD,” says John Gable, vice-president of project management for Enovia MatrixOne, “do semiconductor design and software design, and perform process planning with virtual manufacturing tools. All that data has to come together, and Matrix is typically an aggregation point for collecting it and preparing the cross-functional bill of material.”
Another company that specializes in managing the BOM is Agile Software. When Agile first introduced its product, it specialized in managing manufacturing and outsourced BOMs in high-tech companies, but the company more recently expanded its product line to handle information produced in industrial manufacturing firms. It also offers a specialized product for managing data such as recipes and packaging information for the food and beverage industry.
Agile’s core products include Agile 9 and e6. Agile 9 is the current version of the company’s software for high-tech, electronics, and life sciences applications. The e6 software focuses on automotive and industrial manufacturing and was acquired when the company purchased German PLM firm Eigner several years ago. Although the two products are separate at this time, Agile is investing in an SOA approach to provide common cross-industry features together across product lines.
< < Engineers using Agile Software’s PLM solutions can share visuals with manufacturing personnel as well as the bill of material for a product. Autovue from
Cimmetry Systems
, which Agile recently acquired, can bring together geometry generated by mechanical and electronic CAD programs in a single view.
Agile’s Engineering Collaboration software is available in both Agile 9 and e6, for example. The software incorporates Agile in mechanical or electronic CAD programs so that engineers can create the BOM and push it from the design software into the PLM system. In addition, the program allows engineers to produce visuals and review designs with other team members, including marketers, purchasing personnel, and suppliers. The results of design reviews are stored in Agile.
PLM in ManufacturingPLM programs such as UGS’ Tecnomatix and Dassault’s Delmia enhance lean manufacturing by enabling users to simulate and optimize production processes before they are implemented. UGS’ recently announced Tecnomatix Production Management program, for example, helps ensure that products are properly manufactured by allowing comparison of as-designed, as-planned, as-built, and as-maintained configurations.
> > UGS’ Tecnomatix Production Management stores design and manufacturing information in a single repository, where it can be accessed when needed. For instance, a work instruction can be paired with a 3D part view from a CAD system.
Toyota Motor Engineering & Manufacturing of North America uses Delmia DPM Assembly and IGRIP for robotics simulation in conjunction with its own in-house process planning solution. The company’s digital manufacturing strategy is to first confirm that part structures are good and can be installed in a feasible order. Then assembly processes are evaluated and confirmed. Factory ergonomics checks are finally performed to ensure there are no tooling issues, visibility problems, or that Toyota team members don’t have to operate in awkward postures or conditions that might pose health or safety problems.
“PLM products add extensive value in facilitating lean processes by allowing us to create unlimited scenarios without the expense and resources needed to create physical models,” says Philip Ryan, assistant manager of digital engineering planning and development at Toyota. “Through these virtual processes we are able to shed several months from our development process.
“With PLM programs we now have the luxury of unlimited ‘what-ifs.’ We can anticipate manufacturing scenarios without having to wait for prototypes or other physical methods,” Ryan adds. “One of the most significant benefits ]of PLM] is the ability to recreate past problems and confirm that we have identified effective countermeasures.”
It is often difficult for the engineering and manufacturing divisions at many companies to share information because the groups use different terminology. Yet PLM systems operate using vaults, which keep information secure but can only be accessed by using the specific terminology and workflows that are fixed in the system.
“Implementing PLM suggests constant discussion about how data are organized in the vault,” says Chris Groves, CEO of Centric Software, a vendor of vault-free PLM.
Another problem is that most companies do not store all their key files and data in a single location. Plus, companies often have to exchange design information with suppliers who manufacture their products. The suppliers may have their own ways of managing files and data. “Centralized PLM does not work when you have a supply network,” says Groves.
< < Users set up forms that help them use and review data from various locations that are indexed by Centric Software’s program. For example, users can record their responses to action items.
Centric avoids the data-exchange difficulties of PLM systems because the company’s solution does not rely on a vault. The company’s technology indexes files where they are stored, much in the same way that Google search-engine technology categorizes information found in various locations on the Web. The software looks at files, the descriptive data related to them, and the information inside the files. Indexed files and data are stored in XML (extensible markup language) format and the program is configured so that users can access it in various ways.
The software employs programs that the company calls connectors to link to the repositories. The connector software maintains the security provisions of the PLM-managed databases to prevent access to stored XML-formatted data unless the user has proper permission.
Companies that use Centric’s software can expect to reduce the time it takes to collect information from various sources. Remy International, Inc., a leading manufacturer and distributor of starters and alternators, diesel engines, locomotive products, and hybrid power technology, uses Centric software to collect from multiple PDM systems the data necessary to complete engineering change orders (ECOs). Remy ECOs are configured in online forms and managed through new release alerts, approval tracking, and e-mail notifications. Centric’s software helped the company reduce the time it took to complete an ECO by 50 percent, resulting in a return on investment of eight months.
Whether vault-free or vaulted, today’s PLM programs can make it easier for designers and engineers to share files and data, leading to shortened design cycles. What’s more, newer programs allow users to set up processes that take into account differences between manufacturing and design, improving the chances that information is provided in a form that makes sense.
Nancy Rouse-Talley is a freelance writer who focuses on technology subjects, including product lifecycle management, computer-aided design, and engineering. You can send Rouse-Talley your thoughts on this article through e-mail by clicking here. Please reference “Lean PLM, Part 2” in your message.
Agile Software Corp.
San Jose, CA
Centric Software, Inc.
San Jose, CA
Dassault Systemes
Suresnes, France
PTC
Needham, MA
UGS Corp.
Plano, TX
Subscribe to our FREE magazine,
FREE email newsletters or both!Latest News
About the Author

DE’s editors contribute news and new product announcements to Digital Engineering.
Press releases may be sent to them via [email protected].
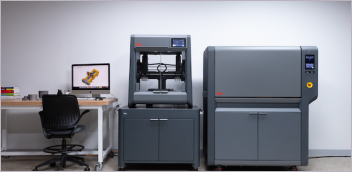
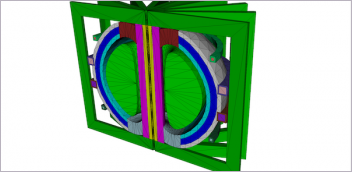
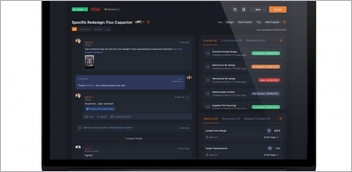
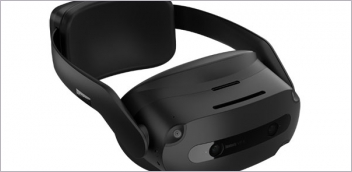