Latest News
June 1, 2006
By Michael Staiano
Desktop products present a tough thermal challenge for designengineers. Small footprints concentrate heat and leave scant space forair circulation. Crowded electronics make it tough to instrument andfind hot spots.
Traditionally, effective thermal solutions for electronic designs couldonly be developed through an endless round of designiterationsbuilding, testing, modifying, and retesting. CFD(computational fluid dynamics) software, however, can save months ofengineering time and effort, and drastically cut project costs.
At Seagate’s Design Service Center, Coolit CFD thermal and flowanalysis software from Daat Research Corp. is used to solve a widevariety of thermal problems for our desktop OEM customers. Thesecustomers are developing new applications and frequently will send usone-of-a-kind prototypes with strict instructions not to chop them upto test various design configurations. With CFD, we aren’t eventempted. We modify designs with just a few mouse clicks and calculateresults in a fraction of the time it would take to modify and testphysical prototypes: No hassle and no waiting for the shop to cut orbend metal.
CFD analysis identifies the temperature at every point in the design,uncovers trends created by design variables, and helps us find theoptimum parameter combination. With CFD, an engineer can see airflow inaction and detect stagnant air pockets, something that is impossiblewith the traditional build-and-test approach. The more efficient thethermal design, the smaller and fewer fans are needed to remove theheat, and fewer and smaller fans mean less noise.
To follow are three examples of the effectiveness of CFD analysis. Inthese examples, CFD locates a stagnant air pocket, uncovers an errantairflow pattern, and helps produce a custom heat sink design. Theseapplications could not have met their budgets or time-to-marketrequirements without the aid of this invaluable tool.Finding the Optimum Design Combination
Millions of DVRs (digital video recorders) are sold each year, andgetting a new design to market quickly can have a major impact onproduct revenue. In one unit the number of parameter permutations madeit impossible to optimize the thermal design using traditional methodswhile still meeting the customer’s project schedule.
The goal was to maximize reliability by delivering the incoming coolair to the hard drive, then directing it to the hottest components, andfinally to the remaining electronics. We separated the hard drive fromthe electronics by surrounding it with a sheet metal wall and thenmounted the fan on the downstream side of the wall (see Figure 1, below). This reduced noise by placing the fan inside the housing, and drewair from the hard drive section to cool the electronics.
› ›Figure 1: To maximize cooling efficiency while minimizing fan noise,the DVR fan is mounted in the divider wall surrounding the hard drive.The divider wall insulates the hard drive from the heat-producingcomponents. Air drawn from the drive compartment passes through thedivider wall to cool the electronics.
While there were a few limitations (mostly because of cabling),essentially the fan could be anywhere in the divider wall, the intakeand exhaust vents could be located on any of the six sides of theenclosure, and the electronics and hard drive could be positionedanywhere on their respective sides of the divider wall. We calculatedapproximately 60 Coolit models, studying the impact of componentplacement, whether the fan should blow from left to right or from frontto back, checking to make sure hot air from the power supply wasn’tdrawn toward the hard drive, and optimizing vent sizes and locations.We uncovered more than one design parameter combination that met thespecifications and were able to supply the customer with severalworkable designs from which to select based on manufacturing costs,aesthetics, or other criteria.
Something as simple as optimizing vent location and size candramatically reduce internal desktop temperatures. This was the casewith a prototype PC designed to operate at an elevated ambient temperature of 35°C. The very high power density model was scrunchedinto a small cabinet that was cooled by forced air flowing through alarge vent. The 6 cfm fan and venting appeared adequate, but the harddrive was overheating.
‹ ‹Figure 2: The original PC design had an oversized intake grill onthe side of the enclosure and a rear exhaust vent on the same level asthe intake. As a result, a significant portion of the incoming aircirculated back out the intake vent, leaving the hard driveinadequately cooled.
CFD analysis quickly pinpointed the problem. While some cooling air wasmaking its way to the hard drive, a significant portion was not; itwas, in effect, being short-circuited and circulating back out theintake vent (see Figure 2, above). For all practical purposes, airaround the hard drive formed a stagnant pocket up against the top ofthe enclosure.
The first design change was to reduce the intake vent size. Since theoriginal vent was much larger than required, the incoming air movedslowly with some of it finding an easy path back out the intake.Reducing the intake area reduced the opportunity for air to exit andincreased the flow directed toward the hot components.
Next, we moved the exhaust vent to behind the hard drive and near thetop of the opposite side of the enclosure. This provided an exit forthe normally stagnant air and created a natural path across the harddrive and components. Baffles were added to direct air toward thehotter components before it exited.
These design changes dramatically reduced drive temperature, whichdropped from 70°C to 58°C . The design changes werecompleted in less than half the time it would have taken to physicallymodify and test the unit.
One application was a 3.5-inch desktop external computer drive used forbackup and archiving (see Figure 3, below). The design ambient was40°C and natural convection cooling was specified in order to eliminateboth the cost and noise of a fan.
› ›Figure 3: The thermal solution for a Seagate 3.5-inch external storageunit was a natural convection design developed using CFD analysis tomaximize cooling efficiency.
Because users were known to place these units in almost any conceivableposition, the drive had to operate both vertically and horizontally.Users also frequently move external drives from one CPU to another, sothe unit had to be fairly robust and able to withstand the shock andvibration dealt to a mobile product. To save space inside the compactunit, the design combined the heat sinks (plates mounted on both sidesof the drive for cooling the drive) and the isolators for shock,vibration, and acoustics into one assembly.
The heat sink size presented the most complex thermal design challenge.It had to have sufficient surface area to adequately cool the unitwhile, at the same time, maintaining low air resistance to permitairflow through the heat sink. These requirements are difficult to meetsimultaneously, as increasing the surface area increases flowresistance, forcing the air to bypass the heat sink and making itineffective. We looked at whether to use a large number of small fins(large surface area, but high flow resistance) or a small number oflarge fins (smaller surface area, but better airflow).
There had to be good airflow regardless of the position of the unit.And there had to be an adequate gap between the drive and enclosurewalls so air would flow easily around the unit. But the gap could notbe enlarged at the expense of the envelope set by industrial design.Finally, the design had to be relatively inexpensive and easy tomanufacture.
‹ ‹Figure 4: CFD temperature profile through cross-section of harddrive shows drive is well within its 69°C design limit. Air movesfreely from the intake at the bottom, across the drive and through thecombined heat sink/isolator and outlet at the top.
Using Coolit, engineering was able to balance all these contradictoryrequirements and determine the optimum heat sink configuration (seeFigure 4, above).
As packages shrink, designs become more sensitive to slight changes incomponent, vent and fan locations, and heat sink design. CFD analysisresults are highly accurate, typically within 5-10%, as shown byverification testing. It is an essential and effective weapon formeeting project schedules and producing cost-effective desktop thermaldesigns.
Michael W. Staiano is an integration and qualification engineer forSeagate Corp., Boulder, CO. Send your comments about this articlethrough e-mail by clicking here. Please reference “CFD Shrinks, July2006” in your message.
Daat Research Corp.
Hanover, NH
Seagate Technology LLC
Scotts Valley, CA
Subscribe to our FREE magazine,
FREE email newsletters or both!Latest News
About the Author

DE’s editors contribute news and new product announcements to Digital Engineering.
Press releases may be sent to them via [email protected].
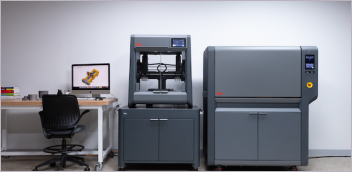
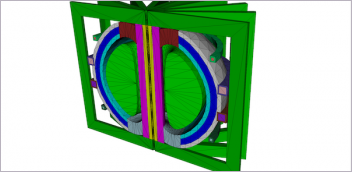
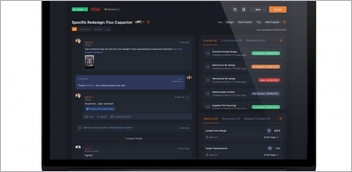
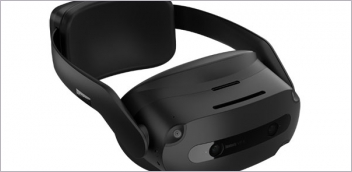