Latest News
October 1, 2009
By Rod Habeshaw
While we traditionally think of loudspeakers as separate boxes, at SFX Technologies Ltd. of Dunfermline, Scotland, we are using COMSOL Multiphysics to help us design a new type of loudspeaker driver that uses virtually any surface—from a tabletop to walls and from mirrors to dashboards—to produce high-quality sound. When a GA (Gel Audio) transducer is placed against a surface, the surface itself becomes the loudspeaker. It’s virtually impossible to model this complex process on a theoretical basis on paper, which makes it a perfect candidate for numerical simulation. After having worked with several modeling packages, we found that COMSOL Multiphysics offers the combination of features and usability that best matches our requirements.
![]() An isosurface plot generated with COMSOL Multiphysics illustrates the sound-pressure levels that emit from a typical panel surface when driven with the Gel Audio transducer. Here the results are shown for one frequency (1092 Hz), while the graph shows the extent of surface displacement. |
Gel as the Interface
Our speaker technology is quite unique: users mount a GA transducer to a panel without being permanently bonded to it, oftentimes using two-sided adhesive tape. The transducer’s magnet and coil receive analog audio signals from an amplifier, and the gel acts as an intermediary material that transfers the acoustic waves to the wall, tabletop, or even billboard. The panel, whatever resonating material it may be composed of, then produces a waveform. Hard surfaces will transmit sound better than softer, absorptive surfaces, but designs are available for a wide variety of applications.
![]() A Gel Audio transducer inside a television can produce very good bass response using the TV case as the resonating surface. The simulation of the sound pressure level at 1900 Hz shows the screen’s structural displacement and a close-up 2D plot around the transducer as a slice plot. |
While the driver can be as small as 11mm x 16mm x 2.5mm, the result is a “speaker” with good high-frequency response with the added advantage of also generating very good bass response without the need for a large speaker box. GA transducers were initially popular in places where customers didn’t want speakers to be visible or accessible, such as in bus stops or public-address systems. Now, though, they are being incorporated into products such as small televisions to generate very good bass response without requiring a subwoofer. We are also looking at putting them into mobile phones for better audio response.
In these cases, it is difficult to test prototypes because handset manufacturers have tight time-to-market schedules. Simulation results can show them what they can expect when drivers are incorporated into their phones so that development can simultaneously proceed on both the phone and the driver.
Previously, it would take us three months to build an initial prototype of a new design, but now we use COMSOL Multiphysics and the Acoustics Module add-on, which enables our design team to achieve a first prototype within a month. This time difference is vital for us, especially when using simulation in our design process because we must get our devices on the market quickly. This technological advantage will be even more vital as we expand from the commercial arena into consumer products.
Complicated Route to Simple Results
Our modeling process takes place in three major stages. First, we create a model of the coil and magnet to determine the forces that are generated at all frequencies. We next take these results and use them in a simulation of the panel to obtain its deformation and acceleration across the frequency band of interest. In the final step, we simulate the acoustic field that the panel would generate. Although we model intricate movement of the loudspeakers, the result we want from the simulation is relatively simple: a plot of the sound pressure level coming from the loudspeaker versus frequency.
Getting to this result, however, requires a complicated route. Simulation is first necessary to size the various mechanical components, such as the coil and magnet in the driver, and examine their effects. Further, while those two components produce unidirectional movement, the panel on the other side of the gel can produce a very complicated waveform, especially at high frequencies, consisting of movement that might lead to sound distortion and modal shapes that change with frequency.
![]() When placed on a panel such as a wall, mirror, or dashboard, a Gel Audio transducer turns that surface into a loudspeaker with good frequency response across the audio range. |
A primary goal of the modeling is to find the optimal assembly—the right amount of gel and the best way to attach it to the surface—and doing so by considering structural-acoustic interactions. Too much gel makes the driver inefficient and unresponsive; too little leads to sound distortions. Initially, our design group used an FEA solution that loosely couples structural mechanics to acoustics iteratively. But this made modeling the acoustics domain an elaborate operation and didn’t really allow us to model what we wanted. We were therefore pleased to find out that we can do all this work in a straightforward manner using COMSOL Multiphysics Version 3.5a. And things just got better using the new predefined multiphysics coupling template between the Solid, Stress-Strain, and Pressure Acoustics modeling templates in the Acoustics Module.
Every Case Unique
COMSOL proves to be very useful for us at SFX because almost every design we consider is unique; we work with a wide variety of panels and panel materials, and for each, a different driver and mounting is required. For instance, the panel that acts as the loudspeaker might be made of any of a variety of plastics, various rubbers and elastomers, or a composite material such as cardboard. In this case, our modelers improvise by representing the panels with isotropic materials. Besides using COMSOL Multiphysics for all of our new speaker designs, we are also examining new ways of shaping panels, where modeling provides an understanding of the involved phenomena as well as concrete design parameters. In addition, we are also starting to combine traditional loudspeakers and GA transducers in the same system. Modeling is essential in these efforts where the acoustics-structure interaction from both devices, and their effects on each other, must be considered.
More Info:
COMSOL
Rod Habeshaw studied acoustic engineering at Salford University, UK, and then worked as a consultant in noise and vibration. He is currently a senior acoustics engineer at SFX Technologies Ltd. Send comments about this article to [email protected].
Subscribe to our FREE magazine,
FREE email newsletters or both!Latest News
About the Author

DE’s editors contribute news and new product announcements to Digital Engineering.
Press releases may be sent to them via [email protected].
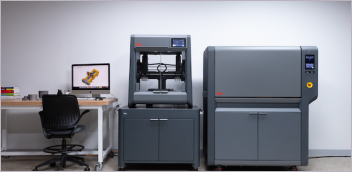
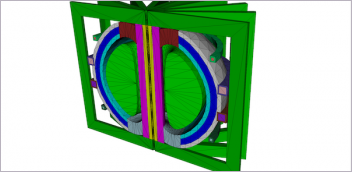
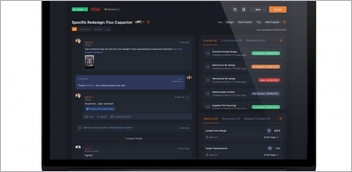
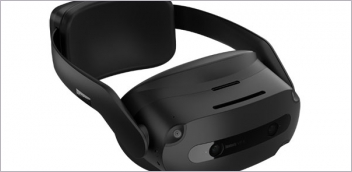