Custom Fit Dental Crowns and Bridges with Rapid Custom Manufacturing Technology
Creating a perfect 3D replica of a patient's teeth with a 3D scanner lead to better fit and time savings.
Latest News
December 18, 2008
By DE Editors
With a history of developing new products, equipment and production techniques within its own Research & Development department, Glidewell Laboratories, a large dental laboratory, uses Roland desktop milling machines to manufacture crowns and bridges. While maintaining seven separate laboratories, Glidewell attempts to keep down costs associated with large dental laboratories by maintaining its own R&D.
The Roland Rapid Custom Manufacturing (RCM) technology makes it possible to produce parts that are custom fit for each patient. Starting with a physical model of a patient’s teeth and using a 3D scanner, Glidewell researchers can create a perfect digital replica of the teeth. Then technicians can take the replica and design and manufacture models to be cased in gold or ceramic, making crowns and bridges that drop right into place with very little or no adjustment on the part of the dentist. It takes only about eight minutes to mill the parts and then cast them. The entire process can be accomplished in a turnaround time of less than five days.
Glidewell starts with the physical model of a patient’s teeth and, using a 3D scanner, creates a perfect digital replica. This allows technicians to design and manufacture models that can be cast in gold or ceramic for crowns and bridges with a perfect, custom fit. RCM offers the flexibility to choose from a wide range of FDA-approved materials.
The Roland RCM technology makes it possible for medical manufacturers to customize their designs on a case-by-case basis. Previously, companies such as Glidewell would have to rely on current clinical processes, such as mass-producing one-size-fits-all parts or hand sculpting unique parts.
Features of the RCM technology include the following:
- One machine does the whole process, from early prototyping to final production.
- A seamless workflow from prototype to production is achieved.
- Machines are added as production needs increase.
- Labor costs are reduced.
- There are a wide range of FDA-approved materials available on the open market.
- The technology allows customers to produce more parts in a smaller work area than traditional, room-sized CNC machines.
- RCM has low energy consumption that complies with green manufacturing practices.
The Roland MDX and JWX series milling machines are designed to produce very detailed parts with smooth surface finishes and tight tolerances. They are suitable for producing prototypes, medical implants and other RCM parts from a variety of materials, including wood, brass, aluminum and plastics. CAM software is included with Roland RCM solutions, which facilitates a seamless workflow with all major 3D CAD applications.
Glidewell Laboratories
Newport Beach,CA
Roland DGA
Irvine, CA
Sources: Press materials received from the company and additional information gleaned from the company’s website.
Subscribe to our FREE magazine,
FREE email newsletters or both!Latest News
About the Author

DE’s editors contribute news and new product announcements to Digital Engineering.
Press releases may be sent to them via [email protected].
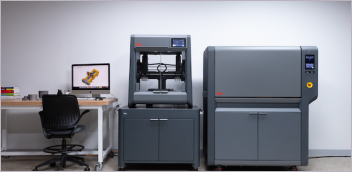
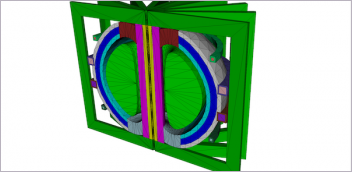
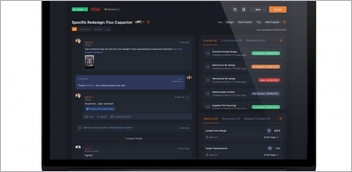
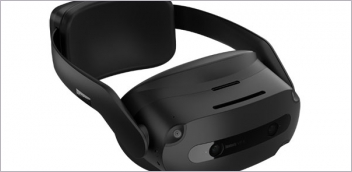