Latest News
October 1, 2005
By Robert Brincheck
Almost 30 years after industry began embracing computerized design technology, too many companies still rely on a relic of the early 20th century—physical drawings—for communicating product information between engineering and manufacturing. Although they develop 3D products using 3D CAD technology, most designers expect production engineers to figure out how to manufacture the products using 2D representations. Their adherence to 2D-centric communication compromises the quality, efficiency, and cost improvements that emerging technologies such as 3D product lifecycle management (PLM) technology provides.
The shift from 2D drawings to 3D solid models as the communication building block in automotive design lays the foundation for digital manufacturing, a major component of PLM. Digital manufacturing is the primary device for automotive companies to compress their production cycles, reduce their expenses, lessen tooling, and save plant construction costs. It is a virtual 3D representation of the manufacturing process exactly as that process would work in real life. It provides a holistic view of products, design, and manufacturing, and puts them in the larger context of a product’s lifecycle from conception to end of life. Digital manufacturing supports process, tooling, and factory design planning; simulates operations, ergonomics, and other human factors.
These capabilities enable companies to: • Mitigate risk from errors Establish proof of concept The economic gains from these efficiencies are hard to overestimate. Digital manufacturing environments give engineers a clearer understanding than 2D drawings of the tools required for production. It also improves training for product and tool designers on manufacturing processes. Overall, it leads to more back-and-forth communication early in the design process, when changes cost almost nothing. As part of a broader PLM suite that includes supply chain management, digital manufacturing encompasses all internal and external stakeholders in a collaborative process that breaks the linear pattern of design-planning-tooling-production and enables them to all happen at the same time.
Surveys of digital manufacturing customers identify annual returns of anywhere from five to 10 times their annual investments in the technology. The U.S. Navy credits modeling and simulation processes with $370 million in total cost of ownership savings on a Bath Iron Works surface ship program. Pratt and Whitney Canada cut 20 percent from its assembly time after it implemented a PLM system around a central repository of 3D solid models. The repository enabled the company’s suppliers to keep abreast of design changes throughout the process, so when designs were finalized, most of the tooling and production was already planned. European auto parts supplier SERRA saw its design time drop 40 percent and its assembly line layout costs drop 60 percent after PLM implementation. According to a Dassault Systemes survey of companies in various industries, the benefits that digital manufacturing has yielded include: Engineering creativity and innovation are going into products at a faster pace than ever. Those designs, however, seldom turn into profitable products. Not because of designs flaws, but because of flaws in the process that introduce errors and stretch production cycles. Economics might have spared inefficient companies until fairly recently, but things are becoming more difficult each year. Market economics have changed radically since the days when a single product could have a multiyear lifecycle with few modifications. Product lines are more fragmented and lifecycles shorter as tastes change and subcontractors rush to keep up. Companies that cannot respond to shifting customer demands by producing high-quality products in tight time frames will not survive the next downturn or consolidation.
The transition to a fully 3D-based product lifecycle requires suppliers to make technology investments, but it does not have to be painful. Most suppliers already design in 3D. All that remains is to put 2D drawings into their proper role—at the end of the process, where they are effective for final verifications. PLM’s Roots in the Automotive Industry It was almost 50 years ago that General Motors started transitioning from ink and Mylar to computerized design, which soon led to 3D CAD technology. At the time, forward-looking executives realized that the company’s 24-month product development cycle lagged behind market demands, and that hand-drawn designs were the culprit. Although it has taken since then to realize computerized 3D’s full potential, major automotive companies are now embracing 3D-based product PLM as the best way to get better products to market sooner. The Language of 3D PLM As a management method that encompasses every facet of a product’s design, production, and upgrade from inception until its end of life, PLM’s goal is to make design and production processes agile. That agility supports aggressive innovation without compromising quality so companies can respond quickly to changing market demands with new and upgraded products PLM is composed of three essential technologies: 3D mechanical design software, product data management (PDM) software, and digital manufacturing software. Together, these technologies provide a common framework for designing products and their manufacturing processes simultaneously. The time saved by working on design and production concurrently gives companies more flexibility to deal with production quality issues before products go to market. Automotive and aerospace companies are the heaviest users of PLM today. However, as many of them move toward full digital manufacturing, they are requiring their suppliers to implement PLM solutions as well, so the entire design and production process is a seamless digital whole from parts to final products. A major component of PLM, digital manufacturing enables companies to model their production processes virtually, yet with real-life accuracy. Unlike often-used animations of production facilities, digital manufacturing simulates production processes exactly as they would work when a facility is built and operating. This enables companies to anticipate collisions and other problems that can slow production or erode the finished product’s quality. The key to digital manufacturing is for every component that goes into a product to exist as a 3D solid model. With the 3D models depicting parts’ exact shapes, dimensions, and physical properties, engineers can anticipate tooling and production needs almost as soon as a design starts taking shape.—R.B. Product Information |
Subscribe to our FREE magazine,
FREE email newsletters or both!Latest News
About the Author

DE’s editors contribute news and new product announcements to Digital Engineering.
Press releases may be sent to them via [email protected].
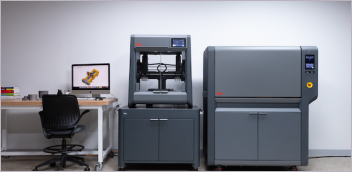
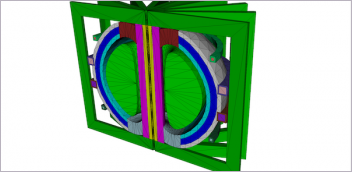
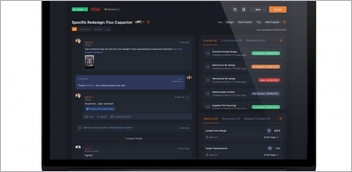
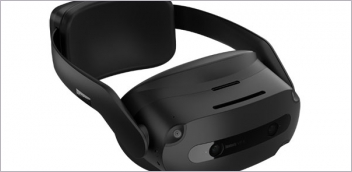