DFMA Hits the Jackpot
Design analysis software from Boothroyd Dewhurst helps engineers score 40 percent total savings on slot machine part and assembly costs.
Latest News
July 1, 2010
By Nick O’Donohoe
Long before the lights start flickering in the video slot machine corner of a casino, a light bulb has to go on over a design engineer’s head. And over the heads of an electrical engineer, a mechanical engineer, and a manufacturing engineer as well.
![]() IGT uses Design for Manufacture and Assembly analysis software from Boothroyd Dewhurst to cut parts, time, and costs. At right are pictured the former electrical box (top) and redesign (bottom). |
“The simple part of a gaming machine is putting in your money and pushing a button,” says Sam Mikhail, engineering manager at International Game Technology (IGT). “The difficult part is keeping every other task relating to the machine nearly as simple. Our customers aren’t only the brand-name operators—it’s everyone who touches the machine.” That includes installation personnel, casino employees reloading the cash system, service technicians, players, and others.
Specifications for the gaming system are quite rigorous inside and out. Because it is an electromechanical product, there are EMF and ESD requirements as well as safety standards to meet. Beyond these, there are security requirements imposed for gaming equipment. “Safety, security, quality, functionality, and cost reduction are our main design goals,” Mikhail says. In addition, the slot machines must be customizable for a wide variety of games, with new ones coming out every few months.
But the more complex the internal assembly, the more time-consuming assembly and service can be. Unless the design team strives for simplicity, their product can build in costs up front. “Bear in mind,” Mikhail says, “Every moment that these machines are shut down they make no money for the casino. Ease of service is extremely important so, for designers here, that’s a constant challenge.”
To meet that challenge, and because of his experience in implementing similar programs in a number of companies, Mikhail led the initiative to implement Design for Manufacture and Assembly (DFMA) analysis software from Boothroyd Dewhurst, Inc., at IGT.
Through the use of the software, one of the design teams in the pilot workshop managed to pare 30 percent off part cost and an impressive 50 percent off assembly times and costs for a critical electrical box used in many of their machines.
Betting on design analysis
Appropriately headquartered in Reno, Nevada, International Game Technology specializes in the design, development, manufacturing, distribution, and sales of computerized gaming machines and systems products. IGT’s video gaming machines are instantly familiar all over the world. The company’s main product families are video and mechanical-reel slots. Cabinets for the machines have either upright or slanted fronts, depending on the angle of the LCD screen.
Inside the slot machine cabinet is a large array of electronic and mechanical components that perform the behind-the-scenes work for the games: generating random numbers for virtual reels, controlling the sights and sounds that make play entertaining, and managing and tracking payment in and out. “It’s very busy inside our machines,” Mikhail explains. “As a result, it’s also very crowded.” Numerous fasteners and limited access points can make assembly and service challenging and time-consuming.
For instance, the electrical box mentioned earlier originally contained two PCBs and a number of hard (plug) connectors wired to it and distributed around the box. The sheet metal box itself had multiple mounting points for parts and several electrical ground points where studs had to be attached by hand and ground wires hooked up. Because there were so many parts in a small space, access was tight and assembly operations difficult. “That box was an obvious place to start a redesign,” Mikhail recalls. “In terms of its complexity and our ability to rapidly put a new design in production, it was low-hanging fruit.”
Mikhail and other IGT personnel began training on their newly acquired DFMA software, which combines two complementary, closely integrated analysis tools: Design for Assembly (DFA) and Design for Manufacture (DFM).
DFA software enables engineers to reduce a product’s complexity by consolidating parts. DFM guides designers through the selection of materials and processes. Early in product development, at the concept stage, the software helps engineers starting with basic shapes or CAD models to cost out alternative materials and processes. The extensive process library and cost models in DFM Concurrent Costing help to identify major cost drivers such as machining time, part handling (set-up) time, materials outlay, or secondary manufacturing processes.
The software was a hit at IGT right from the earliest implementation. An interesting by-product of the design discussions during training was a new level of communication and spirit. “Our design teams have always interacted, with members giving their best input from their specialties,” Mikhail notes. “What was different with DFMA was the level of creativity it drew out. It turned the team training exercise into an environment that was fun to work in.”
Once training was over, it was time to begin a practical, hands-on design exercise.
An assembly in play
The first step was to use the software to benchmark the existing electronic box. Fresh from their training, several team members found that seeing their first real-world analysis triggered new ideas for redesigns. “It was hard to restrain them,” Mikhail recalls, “but I asked them to make notes and wait until we started work on our next analyses.”
With the benchmark complete, each design team—which included mechanical, electrical, and manufacturing engineers and a shop technician—worked methodically on two DFMA-guided redesigns: a highly innovative “blue sky” concept and a more moderate reworking of the original box.
The blue-sky version involved eliminating unnecessary fasteners, particularly for grounding. It also included integrating all the connectors into one bulkhead on the printed circuit board, an option that was “attractive, but unrealistic,” Mikhail says. There were also additional design constraints, such as the need to retain standardized components that were used across other product lines. “Still,” he adds, “the blue-sky design sessions really opened up our creative sides. Someone would make a suggestion so radical that the rest of us would laugh, but suddenly we’d find ourselves thinking how it could actually work.”
The blue-sky version resulted in eliminating more than two-thirds of the parts, with assembly time reduction of over 84 percent. Even the more moderate redesign incorporated two PCBs into one and—by integrating connectors, combining grounds, and consolidating or outright eliminating parts—reduce total components by nearlyhalf.
Source: IGT |
Taking advantage of the freed-up real estate in the new box, the design team relocated several connectors to create room around the plug-ins. The team also shifted components (including mounting them on the lid, bottom, and one side of the box) to make shorter, less complicated wiring runs with simpler harnesses (see Table 1).
The end result was a 30 percent reduction in part costs and a 50 percent reduction in labor cost and assembly time—an overall 40 percent cut in total cost savings. “DFMA gave us a systematic and structured approach to address and satisfy electrical, mechanical, and assembly issues,” Mikhail says. “That paid off, even on our first project.”
The payout
The redesigned electronic box will be included in future gaming machines from IGT. The new design is expected to reduce assembly and service times, cut potential engineering change orders, and promote design modularity.
More than that, the project validated the use of DFMA as a product development strategy. “Our goal is to promote continuous product improvement and lean design at IGT,” Mikhail says. “Now that DFMA has proven its worth, we will go about integrating it in our product design life cycle.”
The company will also be looking at their existing gaming machines carefully to determine which components could provide the quickest and greatest potential returns on a redesign. “One thing’s sure,” Mikhail adds. “Nobody here is going to turn away from a design tool that produces that level of assembly and service time savings.” And you can bet on that.
More Info:
Boothroyd Dewhurst, Inc.
Nick O’Donohoe writes bout technology and design. Send comments to [email protected].
Subscribe to our FREE magazine,
FREE email newsletters or both!Latest News
About the Author

DE’s editors contribute news and new product announcements to Digital Engineering.
Press releases may be sent to them via [email protected].
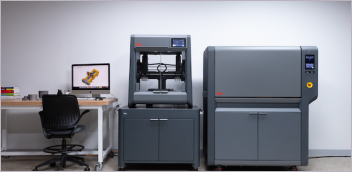
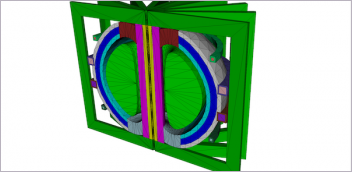
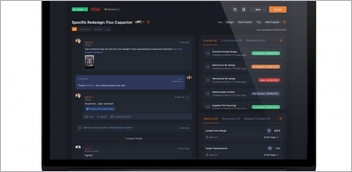
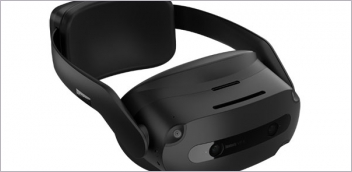