Digitized for Downstream Development
New tools make a NURBS model with high-quality, aerodynamically optimized surfaces.
Latest News
January 1, 2006
By L. James Ashley
New tools make a NURBS model with high-quality, aerodynamically optimized surfaces.
Realadi is making some classified improvements to one of the world’s most aerodynamic propjet airplanes. Today’s version of this propeller-powered aircraft uses a 750hp engine to fly faster than any other plane in its class, even the experimental ones. Tomorrow’s propjet will benefit from new design elements that will take its performance to an even higher level.
But before Realadi can make any improvements, it first needs to generate a complete 3D CAD model of the current propjet. This is a massive reverse engineering job, but Realadi a company with a well-earned reputation for its ability to scan large objects and produce 3D models to meet the most exacting requirements.
In the case of the 26-foot-long propjet, model accuracy need to be within a quarter of an inch with smooth, optimally parameterized surfaces. “We had extremely strict boundary-wrapped guidelines for both accuracy and smoothness,” said Ron Marsden, Realadi VP of marketing & development. “These qualities will help the aircraft fly at high speeds without sacrificing its efficient aerodynamic qualities.”
Data AcquisitionRealadi used photogrammetry and optical scanning technology to obtain the propjet’s 3D data. “This two-step process gives us the most precise scans for large, airplane-sized objects,” said Marsden. “First, we hoisted the propjet up onto jacks, placed markers on the aircraft, and snapped hundreds of pictures with a high-resolution digital camera from different angles.”
![]() |
Point-cloud image of the propjet. |
The photogrammetry process established proper coordinate position and a reference grid right on the model itself, while the optical scanning process captured the detailed surface of the model and aligned each patch based on the marker’s position. “After photogrammetry was completed, we used an ATOS white light high-density scanner to obtain incredibly dense and accurate point-cloud data.”
Capturing all of this raw point-cloud data from the scanner was a huge undertaking, but it was just the starting point for this project. The model still had a long way to go before achieving the extremely precise model specifications. Realadi needed to smooth out and mold these data points before it could transform them into a highly accurate CAD model with aerodynamically optimized NURBS surfaces.
![]() |
Surface image of the propjet. |
First, Realadi cleaned up the point-cloud data. “The propjet had tons of sampling points,” said Marsden. “We digitally removed all outliers and greatly reduced surface noise.”
Next, Realadi converted the propjet’s point-cloud data into a polygonal mesh model. While point-cloud data typically lacks precision and is nearly impossible to manufacture, polygonal mesh can be manipulated and articulated to a high degree of integrity. This enabled Realadi to make several enhancements required for down stream users.
Now on the home stretch, Realadi relied on RapidForm reverse engineering software to convert the polygonal model into a refined CAD model with high-quality, accurate NURBS surfaces. The resulting CAD model met and even surpassed the high standards and expectations for the new propjet.
![]() |
ISO surface image of the propjet. |
“RapidForm was our primary surface generator,” said Marsden. “We really put the reverse engineering software though its paces. RapidForm was instrumental in helping us meet the quality requirements for this model. It gave the propjet model an incredibly smooth NURBS surface that, in addition to looking good, maintained the propjet’s superior aerodynamic properties.”
“RapidForm definitely saved us lots of time and money,” added Cliff Yanzick, Realadi director of operations. “It let us complete the project 100 hours faster than any other reverse engineering software we’ve tried. RapidForm’s robust algorithms and precision surface generation decreased processing time for the entire project.”
Realadi integrated additional parts into finished propjet CAD model using RapidForm. With these final touches, the CAD model was complete and ready for downstream design and manufacturing.
![]() |
This screen shot shows the STL (stereolithography) image of the propjet. |
“These additional parts might end up on a future propjet,” said Marsden. “After these types of changes are made to the current CAD model, they will likely mill it with a subtractive rapid prototyping device and test it in a wind tunnel. Eventually, the model could be manufactured as a new propjet and rip though the clouds at over 350 mph.”
L. James Ashley has been writing about high-tech for more than 25 years. He says it all started with a soldering iron. Send your thoughts about this article via e-mail by clicking here. Please reference “Digitizing for Downstream, January 2006” in your message.
Contact Information
ATOS III, TRITOP
Capture 3D, Inc.
Costa Mesa, CA
RapidForm
INUS Technology, Inc.
San Jose, CA
Realadi, Inc.
St. Charles, MO
Subscribe to our FREE magazine,
FREE email newsletters or both!Latest News
About the Author

DE’s editors contribute news and new product announcements to Digital Engineering.
Press releases may be sent to them via [email protected].
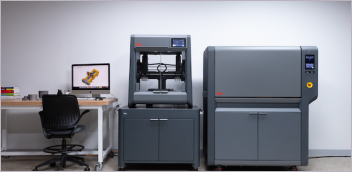
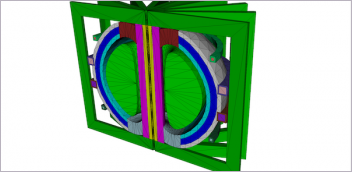
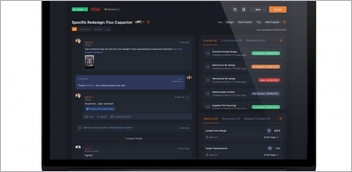
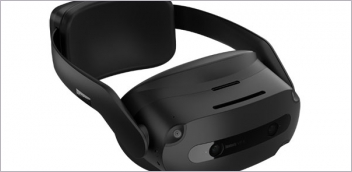