Latest News
April 1, 2006
By Louise Elliott
While industry analysts and PLM vendors discuss the PLM needs of small and midsize businesses (SMB) in broad market terms, the companies themselves are, by and large, very pragmatic in interpreting their needs for the technology. In this third installment on PLM for the SMB market, DE interviewed users in firms that make products ranging from golf clubs to pharmaceutical lab enclosures and from ultra high-tech optical devices to interactive advertising systems. Their immediate needs differ, as do their criteria for choosing PLM solutions. (Click here to go to Part One of this series or here for Part Two.)
The kinds of products they make, as well as the number of different products and quantities they produce, dictate their needs and guide their choices.
Internal Collaboration
Flow Sciences Inc. (Leland, NC) makes standard and custom containment enclosures for pharmaceutical laboratories. Tom Rambach, senior designer and CAD manager for the company, describes product design changes as generational. “Once we’ve built and shipped something, that design won’t go on changing,” he says, “but as technological knowledge grows, designs evolve.” His department had Autodesk Inventor with its built-in Vault but, Rambach adds, “we needed to handle data that had been scattered on different computers, and also to replace paper for internal collaboration.”
|
Image courtesy of Flow Sciences. |
› › Flow Sciences makes containment enclosures for pharmaceutical laboratories and uses
Autodesk’s Productstream for its collaboration capabilities and its ability to handle data
scattered on different computers.
The company now uses Autodesk Productstream for “any task that generates files, including CAE runs,” he reports. The system has helped Flow Sciences move away from paper-based processes for part procurement by purchasing managers, getting assembly data to the shop floor, and making sure all incoming parts match specifications.
“We get our return on investment from a shorter design cycle, because the system streamlines product development through reuse of designs, without time wasted in hunting for older ones. It gives us a central, accessible location for all data.”
Configuration Management
Elcan Optical Technologies, a Raytheon company based in Midland, Ontario, needed to improve its configuration management processes, which, says Product Quality Manager Gunter Schmidt, “couldn’t keep up with demand and caused bottlenecks.” Elcan decided to base configuration management on Raytheon’s Six Sigma program, and to deploy PLM starting with configuration management.
“We found inefficiencies and duplication, as well as significant downtime caused by paper-based processes and use of microfilm, which was also very costly,” Schmidt says. Elcan wanted a system that worked with AutoCAD and Inventor, and would also work with an existing MRP program. Elcan’s first PLM system took a year to implement, and proved very helpful—but was discontinued, and the company went with Softech.
Softech gave Elcan a three-month trial, and installed and set up workflows so that the system worked in parallel with the existing PLM tools.
“The actual installation went live in six weeks, is easier to use than the old one, and is less time-consuming,” says Schmidt. “We’re planning to expand its use. It has a 3D modeling capability, and we’re using it for assembly. We are also looking at contract approval and review, and help with meeting ITAR requirements—and this system makes it easy.”
Project Management and Design Cycle
Ping Inc. (Phoenix, AZ) designs and makes golf clubs and accessories. Dan Shoenhair, director of engineering, says that in 2001, “we saw a significant need to become more agile to shorten the design cycle and get products to market faster.” The company recognized that it needed to capture knowledge in an organized way and decided to implement Pro/Engineer and Windchill ProjectLink simultaneously. At the same time, Ping set up a project management team.
|
Image courtesy of Ping, Inc. |
‹ ‹ In 2001, Ping needed to shorten the design cycle of its golf products and implemented Pro/Engineer and Windchill ProjectLink to capture knowledge and better manage projects. Ping went from introducing two products in 2001 to introducing 14 in 2005, and greatly shortened time to market.
“Once we had established the use of Pro/E and built our project management capability, we implemented PDMLink,” Shoenhair says. “The results have been dramatic.”
Ping measured the results. “In 2001 we introduced two products; in 2005, we introduced 14. It used to take about 24 months from inception to shipment, and now it takes less than nine, bringing us closer to users’ needs. We’ve also had a nine-fold increase in productivity at the high end with Pro/E, and three- and four-fold gains with more midrange products.”
Project Management and Workflow
Sonnax Industries of Bellows Falls, VT, designs, manufactures, and distributes replacement transmission, torque converter, and related automotive parts worldwide. Its catalog includes approximately 4,000 salable products, of which about 250 are new products under development every day. Jeff Loewer, vice president of planning and IT, says, “We didn’t go looking for PLM, but rather for ways to handle specific issues. Primarily, we needed help with project management. We wanted to replace Excel spreadsheets, time reporting software, and a workflow tool—all separate from each other and giving us no good ways to extract data and analyze the ... process.”
|
Image courtesy of Sonnax Industries. |
› › Sonnax Industries has about 4,000 automotive parts in its catalog, of which about 250 are under development every day. It picked Aras for its project management, engineering change orders, and QA capabilities.
After looking at a number of PLM tools, Sonnax chose Aras, because the system could be extended beyond project management, and has already added engineering change orders and QA. “Our product quality benefits from the system, because we can record receipt inspections and access the data as needed,” Loewer says.
“What used to require the time of many people can now be done quickly by one,” he says. “In fact, new product development used to be managed by a small group of people who knew the old ad hoc tools, and they formed a bottleneck because they had to coordinate everything.” Those people aren’t involved in product development any more; instead it’s managed by the people who do the work—accountable stakeholders who now generate ideas and participate more directly.
CAD-Based Remote Collaboration
Liebert Corp., a Columbus, Ohio-based division of Emerson Electric, designs and manufactures power management, cooling, enclosure, and similar high-technology tools for intensive computing environments such as data centers. The company uses Agile tools to manage PDM processes related to bills of material (BOM), engineering changes, and approvals as related to the BOMs.
“CAD data lives in its own environment,” says Jack Beeckman, manager of CAD systems administration for Liebert. “Interconnectivity within CAD makes it hard for designs, apart from visualizations, to be accessed by PDM.” Liebert uses Solid Edge for design, Mentor Graphics for printed circuit boards, and some locations have legacy data in other CAD programs. Because Insight, the PDM tool inside Solid Edge, doesn’t work with other CAD models, and also doesn’t enable easy global sharing, the company decided to implement Teamcenter Express from UGS.
“Teamcenter Express lets us replicate data from one locality to another, and integrate with ERP and other company-wide tools,” Beeckman says. “We’re also testing a mixed environment of Teamcenter Express and Teamcenter Engineering to ease communication worldwide.”
Widespread Team Accessibility
The only word to describe technology from Reactrix Systems (Redwood City , CA) is “cool.” Reactrix makes an advertising system for malls and theater complexes that projects images on walls and floors, and the hardware and software that make it possible for people to interact with them. The hardware used, mostly projectors and computers, is produced in low volumes—some 50 to 100 systems at a time. However, the system is complex, and many parts come from many different sources.
|
Image courtesy of Reactrix Systems. |
‹ ‹ Reactrix makes an advertising system that projects images on walls and floors, and the hardware and software that makes it possible for people to interact with them. To keep track of everything involved in the low-volume but highly complex systems, Reactrix uses Arena Solutions because the hosted solution proved to be flexible enough to enable wide access to data for everyone who needed it.
“It’s hard to keep track of which products—CPUs, cards, electronic components—go into which configurations,” says Helen Shaughnessy, product marketing manager for hardware. “We use a contract manufacturer and an outside design company, both of which we trust a great deal and with whom we need to share data.”
Reactrix decided on Arena Solutions for its PLM needs because the system makes it possible for both contractors to have full access, and because the hosted solution proved to be flexible enough to enable wide access to data for everyone who needed it. “Even Arena didn’t understand how much access people needed to BOMs, engineering change orders, and suppliers’ component availability. But they learned and have been very helpful.”
Toward Lean Product Development
Phillips & Temro chose to go with a hosted Windchill PLM system from PTC. The company’s primary CAD platform is Pro/E, but they actually use six different CAD platforms to work with customers, and “Windchill works with all CAD programs.” The investment was a big consideration, Gill says, “and being able to do PLM on-demand meant that just one engineer, who also did his regular work, was able to do the implementation, with help from the local PTC reseller.”
Gill defines his most important reason for PLM implementation as wanting the system to give uniformity of processes and help people do their jobs better. “With it, we created a product development process that would make workgroups more productive,” Gill says.
Every company that helped with this story has individual needs that have started to be met with PLM tools. Each is different. The most frequently mentioned goal, however, appears to be the product development issues articulated by Alan Gill. DE will zero in on that topic in a future story.
Contributing Editor Louise Elliott is a freelance writer based in California. Offer Louise your feedback on this article by clicking here. Please reference “One Fits All, May 2006” in your message.
Product Information
Agile Software
Aras Corp.
Arena Solutions
Autodesk
Elcan Optical Technologies
Flow Sciences, Inc.
Liebert Corp., Division of Emerson Electric
Ping, Inc.
Phillips & Temro
PTC
Reactrix Systems
Sonnax Industries
Softech, Inc.
UGS Corp.—Solid Edge
UGS Corp.
Subscribe to our FREE magazine,
FREE email newsletters or both!Latest News
About the Author

DE’s editors contribute news and new product announcements to Digital Engineering.
Press releases may be sent to them via [email protected].
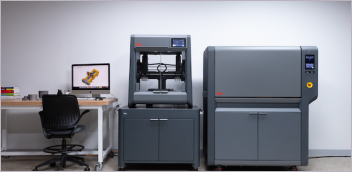
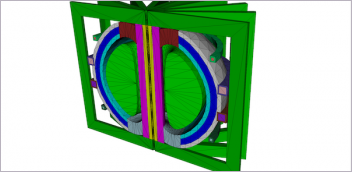
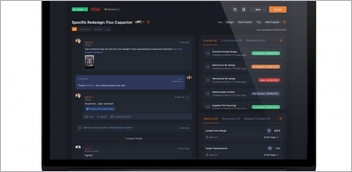
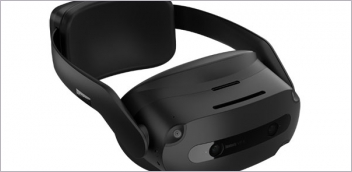