EDEM Helps Astec Engineer a Better Dryer
DEM Solutions simulation software leads to operational efficiency and greener asphalt production via accurate visualization.
Latest News
April 1, 2010
By Andrew Hobbs
![]() This is a close-up of the simulated drum in action showing the veiling of aggregate in the dryer. |
When going green means using less energy and saving money, everyone’s on board. This is especially true with asphalt production—an energy-intensive operation where hundreds of tons/hour of aggregate rock must be dried to ensure good binding between the asphalt cement and the rock particles. At Astec, Inc. we found that it’s often small design changes that improve equipment efficiency and lead to less wasted heat, lower fuel costs, and lower emissions. When we set out to develop a more energy-efficient drum dryer that could process a wide range of aggregate types, at various tonnage rates, we turned to EDEM simulation software from DEM Solutions to test our designs. EDEM gives us a virtual environment to observe and analyze what can’t be seen with the naked eye—the effect of flight design and operating parameters on material flow within an operating drum dryer.
The drum dryer is the heart of the hot-mix asphalt production process—typically a counter-flow dryer, heated by a burner at the far end. A conveyor feeds aggregate into the rotating inner drum where it is kept in motion by sections of flighting (cupped steel paddles of various design) that are attached to the inner surface. As the drum rotates, each flight collects aggregate and gradually releases it, producing a “veil” of falling material within the drum. Better veiling exposes more of the wet aggregate to the burner’s heat—improving heat transfer, speeding the drying process, and directly reducing the unit’s fuel consumption.
One of the goals in engineering a more efficient and economic dryer, then, is more effective veiling of the aggregate. Improved veiling, however, isn’t straightforward. Both the amount of aggregate picked up and dispersed by the flights, as well as the rate of release of aggregate as the drum rotates are important. A given design may perform well at high tonnage rates, but not at lower rates. Flights may work well with some aggregate mixtures, but not with a wide range of materials. Also, aggregate properties change as the material dries, so the flight veiling pattern is typically altered over the length of the drum.
Field testing new flight designs is, in itself, a challenge. The harsh internal environment of the operating dryer makes direct measurement and observation inside the unit nearly impossible. Without the EDEM discrete element method simulation we would have to rely on trial and error. With EDEM simulations we were able to set up a virtual environment to examine—with particle-scale resolution—the veiling performance of prototype flight designs, and use this knowledge to design a new flight that improved the aggregate drying process.
To accurately simulate aggregate flow and veiling in the Astec dryer, we imported CAD files of the full drum geometry into EDEM. We also generated a ‘virtual aggregate’ model in EDEM, assigning physical properties to the particles to replicate the behavior of a range of aggregate rock types. Once the virtual aggregate rock particles were introduced into the model drum, EDEM simulated the dynamics of the particles as they were lifted and released by the flights.
![]() Cross-section of the drum showing examples of veiling action induced by different flight designs along the length of the drum. |
EDEM allowed us to visualize the particle flow and analyze particle-particle and particle-equipment interaction within the rotating drum. Using EDEM’s binning functionality, which calculates statistics such as the numbers of particles in a given volume, we were also able to quantify the density of the veiled aggregate in a given drum section. A grid of bins was positioned along a cross-section of the drum and the number of particles falling into each bin was recorded over time. We were able to compare the performance of different flight designs by examining plots of veil density across the drum as it rotated. Our objective was to achieve as uniform a distribution of particles as possible.
Ultimately, after simulating the veiling action of many design iterations, we identified a flight geometry that provided optimum veiling characteristics for a range of aggregate types and tonnage rates. The new flight design, which we call our “V-Flight,” has proven successful in trials.
EDEM software has proven itself a valuable design tool and Astec engineers have made it an integral part of our design process. Using EDEM shortened the design cycle by giving us the capability to virtually test prototypes of new flights within a simulated operating dryer. We also have more confidence in our understanding of aggregate behavior in the drying process and we’re now using EDEM for trouble-shooting existing dryers in the field, where local aggregate properties can present problems that require custom solutions.
![]() Astec, Inc. counter-flow dryer: wet aggregate enters the drum at right, and travels toward the burner at left. |
The new design that EDEM helped us engineer is more efficient, reduces drying time, and uses less fuel than previous designs. This makes Astec customers more competitive and, at the same time, reduces the impact on the environment.
Astec is well known as a hot-mix asphalt plant market leader that makes improvements largely due to customer feedback. We are also moving ahead with research and development of green technology—such as low-emission warm-mix systems, solar heating, and the engineering of more energy-efficient asphalt production equipment. Green technology is no longer limited to cars on the road—it’s now being applied to the equipment making the roads.
More Info:
Astec, Inc.
Andrew Hobbs is an engineer at Astec, Inc., specializing in computer analysis. Send comments to [email protected].
Subscribe to our FREE magazine,
FREE email newsletters or both!Latest News
About the Author

DE’s editors contribute news and new product announcements to Digital Engineering.
Press releases may be sent to them via [email protected].
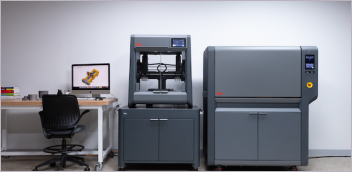
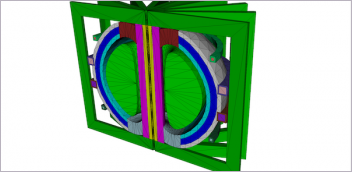
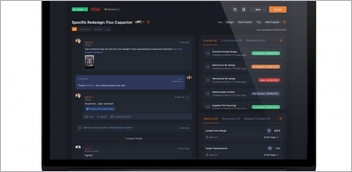
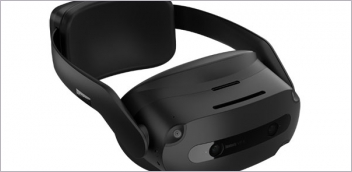