Fast parts for fast cars
Students turn to SLS to meet race car design challenges.
Latest News
June 27, 2007
By DE Editors
SLS (selective laser sintering) services provided by the UK’s 3T RPD played a key part in two entries in the Formula Student race car design competition. In both cases, student designers used the technology to build actual parts used in their vehicles.
![]() |
The competition challenges university students from around the world to design, build, and compete with a small, single-seat racing car. The contest is run by IMechE (Institute of Mechanical Engineers).
The University of Hertfordshire’s Formula Student competition team used the service to build a plenum chamber for the intake system on the UH10 race car. The SLS process fabricated the part from a nylon material that offered significant weight savings over other options, without compromising durability or strength. SLS is also able to handle complex forms, so the team was free to make the design as complicated as they liked. The student team plans to carry out research and pressure testing on the plenum chamber to determine whether SLS is a viable manufacturing option for other parts of the vehicle. The plenum chamber must withstand high vacuums generated by the engine when running.
3T RPD also sponsors the Oxford Brookes University racing team and supplied several parts for its 2007 race car. 3T used SLS technology to build two housings for the car’s electronic components. One houses the electronics that control the front end of the car, and the other contains the engine computer, relays, fuses, and rear end control electronics. To minimize overall weight, the racing team wanted to reduce the number of parts in the car. Toward this end, they came up with the idea of housing the electronic parts in a box that incorporated an integral fuse box to keep the relays in place. Such a design wouldn’t be feasible using any other manufacturing process because the tooling costs would be too high. Once the team decided on SLS, they were able to design the housings around the internal components to fit them precisely.
![]() Teams in the Formula Student challenge design and build single-seat race cars. | ![]() Oxford Brookes University students used SLS to make the housings for their car’s electronic components. They spray-painted the housings black for a more finished look and to hide oil stains. |
“We can do things with rapid prototyping that would not otherwise be possible on our tight time scale,” said Ian Cooke of Oxford Brookes University.
The housings have performed well during testing. In fact, the design team underestimated the strength of the glass-filled nylon material used in the SLS process. Future housings could be built with half of the current wall thickness. The housings are strong enough to act as structural supports for the radiator duct and fan.
3T RPD runs six SLS rapid prototyping machines and offers a range of materials. It also recently expanded its line to include metal parts created through DMLS (direct metal laser sintering).
www.3trpd.co.uk
www.formulastudent.com
Sources: Press materials received from the company and additional information gleaned from the company’s website.
Subscribe to our FREE magazine,
FREE email newsletters or both!Latest News
About the Author

DE’s editors contribute news and new product announcements to Digital Engineering.
Press releases may be sent to them via [email protected].
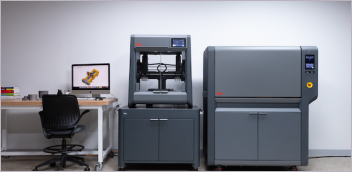
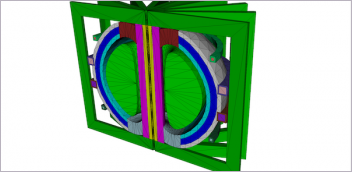
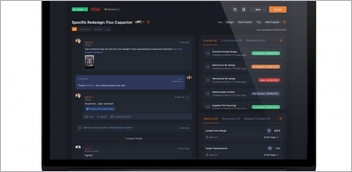
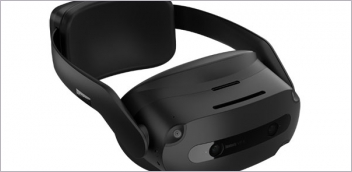