Latest News
September 19, 2007
By Sara Ferris
Lowrance (Tulsa, OK), one of PTC’s earliest customers, continues to find competitive advantages in using Pro/ENGINEER to design GPS instruments and SONAR systems for sportfishing. The company recently used Pro/ENGINEER design and simulation tools to develop a family of marine electronics products in only six months, cutting in half the time required using the company’s previous design methods.
In 1957, Lowrance introduced the world’s first sportfishing SONAR instruments that were capable of locating individual fish. The company’s focus is still on fish-finders, but consumers now expect devices loaded with ever more features. Instead of the old two-tone electronic displays, consumers prefer color monitors that can be easily viewed in outdoor, direct-sun environments.
For its new family of marine electronic devices, Lowrance challenged its engineers to include features such as 800 x 600 pixel color graphics and internal hard drives as large as 30GB.
![]() |
The Lowrance LCX113C HD sonar/GPS chartplotter features a 10.44-inch screen with 800 x 600 resolution. |
In parallel with this design initiative, Lowrance investigated how to streamline its design process to facilitate simultaneous work on multple projects, thereby accelerating the time-to-market of new products.
Lowrance turned to PTC to help them leverage the Pro/ENGINEER product line in executing these initiatives. The integrated design and simulation capabilities of Pro/ENGINEER enabled Lowrance engineers to concurrently design the marine electronics as linked assembly models that reference many of the same parametric component models.
“Being able to do all three projects concurrently while reusing components to a much higher degree than normal helped us cut a lot of time out of the design process,” says Steve Swisher, senior design engineer at Lowrance. “The result was that we were able to beat our competitors to market with some exciting new products.”
Reuse Returns
This approach increased the ability to maximize modularity and component reuse among the three new products. Because the designs were coupled, common components had to be changed only once to update their references in all of the products.
“Rather than designing components for one product and then waiting to see if they could be used on the other members of the family, we designed components upfront to meet the requirements of all three products,” Swisher says. “So we were able to re-use many more parts than in the past.”
Despite the emphasis on part reuse, there were still differences in the envelope of key components, so each product required a substantially different mechanical design. The individual instances of the components were adjusted parametrically to fit the individual products.
“All three products were designed on the same datum plane so when new components were utilized, they were simply aligned to the datum plane,” Swisher says.
Speedier Surfaces
Lowrance gained further efficiencies through the use of the Pro/ENGINEER Interactive Surface Design Extension (ISDX). That surface modeling tool was used to create the look of the outer shell. It provides advanced surface modeling capabilities within the Pro/ENGINEER environment. That means that industrial designers and mechanical engineers can work on the same model simultaneously.
For example, the shell for the new chartplotters created by the industrial designers encompassed multiple components. Mechanical engineers divided the shell and provided offsets to create the bezel and keypad. As the mechanical design was produced, industrial designers oversaw any required adjustments to the shell.
Links to Analysis
An additional benefit to designing these products using a single system is that the electronics could be analyzed throughout their development to ensure that they satisfied performance requirements, reducing the reliance on physical prototype testing late in the process.
Lowrance engineers performed interference checking within Pro/ENGINEER and exported the design geometry to computational fluid dynamics (CFD) software to analyze electronic cooling. Preliminary models were provided at an early stage to groups responsible for building and testing the new products. Later, the design geometry was exported to create computerized numerical control (CNC) programs that were used to produce the tooling used to mold the enclosure, bezel, and keypad.
“Planning for component reuse gives us the ability to simultaneously design and test across all three new products,” said Steve Swisher, senior design engineer at Lowrance. “Using the old system, it would have taken one year to design, test, and deliver these products to the market, versus the six months that it took with the PTC Product Development System. We were also able to reduce costs typically associated with multiple physical prototype development and multiple quality control cycles.”
Sources: Press materials received from the company and additional information gleaned from the company’s website.
Subscribe to our FREE magazine,
FREE email newsletters or both!Latest News
About the Author

DE’s editors contribute news and new product announcements to Digital Engineering.
Press releases may be sent to them via [email protected].
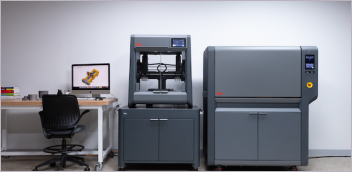
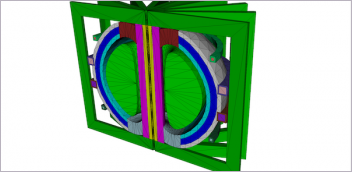
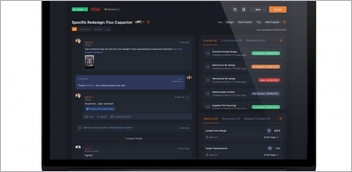
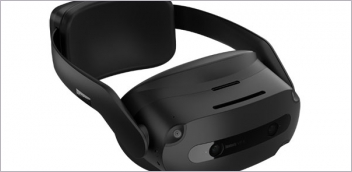