Latest News
February 1, 2007
By DE Editors
PAM-QUIKFORM for CATIA V5 from the ESI Group (Paris, France) is a new simulation tool that can predict the deformation of the reinforcement of composite parts during manufacturing. The software is based on geometrical methods and can determine if a selected material can be used to form a part without potential problems.
The PAM-QUIKFORM algorithms can capture the specific deformation mechanisms occurring in unidirectional draping like intra-ply sliding or the spreading of the fibers, enabling the simulation of unidirectional composite deformation during the draping process.
PAM-QUIKFORM, which was developed under the CAA V5 Gold Software Partnership Agreement signed with Dassault Systemes (Paris, France), is currently implemented in DS’ CATIA V5 Composites Design.
With this integration, the simulations can be directly performed based upon the laminate definition built in CATIA V5 Composites Design. All the existing CATIA V5 Composites Design options, like flattening and 2D/3D transfer, are available and exportable to digital manufacturing machines like Automatic Laser Pointer or nesting and cutting programs available in CAA V5.
For more information, visit esi-group.com.
Sources: Press materials received from the company and additional information gleaned from the company’s website.
Subscribe to our FREE magazine,
FREE email newsletters or both!Latest News
About the Author

DE’s editors contribute news and new product announcements to Digital Engineering.
Press releases may be sent to them via [email protected].
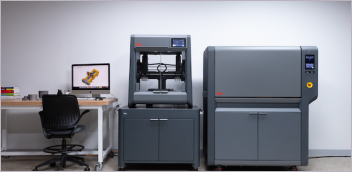
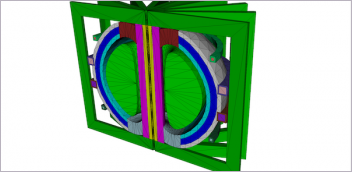
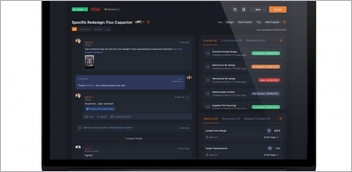
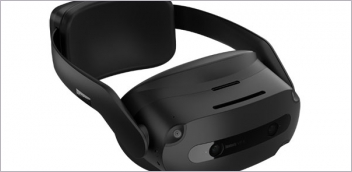