Latest News
January 1, 2009
By Christopher N. Delametter
![]() Figure 1: A short electrical pulse is applied to a thin-film stack and superheats the ink. |
When Eastman Kodak Company decided to enter the inkjet-printing market, it had no time to waste if it wanted to capture part of an expanding segment.
Kodak planned to make inroads by providing photo prints with vivid colors that last a lifetime and substantially reducing ink costs at the same time. It would accomplish this by using premium pigment-based inks delivered through a print head incorporated into the printer rather than as part of the replacement ink cartridge.
While the innovative ink had recently been developed, the project required the development of a totally new print head, the heart of an inkjet printer. And while industry experience had shown it typically takes 8 to 10 years to develop new inkjet printer technology, Kodak researchers accomplished the task in only three years. They developed a design in which the ink vapor vents to the atmosphere so there is essentially no mechanical wear on the heater.
One of the keys to Kodak’s success was the use of simulation technology that enabled engineers to predict the performance of a conceptual print head design with a high level of accuracy and reliability.
Innovative Ink Leads to New Printer Line
Most inkjet printers use dye-based inks that provide vibrant colors but tend to fade over time. Dye-based inks use an organic dye dissolved in a solvent, a process similar to the ink used in a fountain pen. In contrast, pigment-based inks consist of a liquid suspending colored particles chosen for their stability, similar to oil paints.
In the inkjet printer arena, dye-based inks have always provided livelier colors while pigment-based inks have lasted longer. A key innovation that shaped Kodak’s EASYSHARE line of printers was the development of a pigment-based ink that provides the same level of brilliance as dye-based inks, but which last much longer. Kodak managers determined to build on this improvement by eliminating the need for each cartridge to include the costly printhead, thereby further reducing the cost of replacement ink cartridges.
![]() Figure 2: This simulation shows the vapor bubble forming and pushing the ink (blue)through the nozzle plate (top gray block). |
The challenge for Kodak engineers was to develop a print head that could deliver this new ink precisely onto the paper and other media while providing much longer life than existing print heads. Early work at Kodak on microelectromechanical systems (MEMS) provided the foundations for a unique thermal inkjet drop ejector design. In its basic operation, the print head works like those in other thermal inkjet printers whereby a short electrical pulse is applied to a resistive heater structure embedded in a thin-film stack located below a chamber that holds the ink. Approximately one microsecond after the heat is applied, the fluid next to the heated structure reaches its superheat limit and a vapor bubble begins to form. The vapor bubble expands rapidly, driving fluid through the orifice, and propelling a droplet onto the paper. In addition, some of the displaced fluid is forced back into a liquid supply reservoir. As the vapor bubble expands, energy stored in the thin fluid region adjacent to the vapor is depleted. Eventually, the bubble growth can no longer be sustained and the bubble collapses. In essence, the bubble acts as a pump that forces the droplet out of the head and onto the paper.
Incorporating the Print Head
In many thermal inkjet printers, the ink in the nozzle that is not ejected collapses back onto the heater with substantial force, wearing it out over time. Kodak researchers pursued an approach in which the vapor bubble vents to the atmosphere, so there is essentially no mechanical wear on the heater. In addition, the material forming the heater does not change over time as much as most thin-film heater materials. Because of this, the heater not only lasts through many ink tank changes, but the characteristics of the drops are very stable over long lifetimes.
The resulting improvement in print head life made it possible to consider incorporating the print head into the printer rather than into the cartridge. In addition, an approach was taken of building the nozzles directly into the print head. Normally, inkjet print heads have a separate nozzle plate attached to the integrated circuit that forms the print head, creating a sandwich with fluid passages in between.
It is difficult to align these components with precision and misalignment results in dot placement errors. Building the nozzles into the print head is an inherently more accurate method. Nozzles for Kodak EASYSHARE printers are produced using thin-film semiconductor fabrication processes. The chamber and nozzles are built layer by layer from silicon-based oxides and nitrides using standard microelectronics manufacturing processes. The heater is made from a resistive material and metal materials are deposited to form the leads and contacts of the assembly. The result is a monolithic structure that provides alignment tolerances that would be impossible with traditional two-plate systems.
![]() Figure 3: This simulation of ink droplet formation was used for experimental device configurationand served as a basis for comparison with physical experiments. |
MEMS design challenges
After developing these concepts, Kodak researchers were tasked with optimizing the design. They had to answer questions such as how large to make the chamber, what diameter to make the nozzle, and how thick the nozzle plate should be. They labored under the usual constraints that apply to MEMS: physical testing will determine whether a MEMS design works but only after a time-consuming process of prototype creation. The silicon processing cycle used to produce the print head takes about six months. If the design does not work, which is typical, then the small size of the device and the microsecond time scale of inkjet firing events make it difficult to determine why not.
Like most manufacturers of inkjet printers, Kodak uses computational fluid dynamics (CFD) technology to simulate the operation of potential print head designs in software in much less time than would be required to build and test a prototype. Kodak researchers recognized that to meet the time constraints of the project, they needed both very accurate simulation software and a systematic method of optimizing their design.
Homogeneous Bubble Model
Kodak engineers met their first objective of accurately simulating the print head operation by modeling it with FLOW-3D CFD software from Flow Science Inc. They used the FLOW-3D preprocessor to develop the geometry. FLOW-3D incorporates a homogeneous bubble model that couples the formation of the vapor bubble to fluid and heat flow. A heat source within the thin-film stack is transported to the ink by conduction within the solid structure and by heat transfer at the fluid-solid interface. The vapor bubble forms explosively once the superheat temperature is reached in the fluid. The bubble is assumed to have homogeneous pressure and temperature, the dynamics of which are governed by the Clapeyron equation for the vapor. Mass and heat exchange at the vapor-liquid interface continues as the bubble expands, with the mass flux determined from kinetic theory. Surface tension and viscous forces are also included in the simulations.
Proper representation of forces and fluxes in the model depends on accurate tracking of the free surface, which is achieved by using the TruVOF methodology and is a significant part of the calculations.
Design of Experiments
Kodak researchers met their second objective of optimizing the design by using design of experiments (DOE) to drive their print-head simulations. The traditional approach to optimizing a product or process using computer simulation is to evaluate the effects of one design parameter at a time. The problem with this approach is that interactions between design factors and second-order effects are likely to result in a locally optimized design that will provide far less performance than the global optimum. Kodak researchers use DOE to develop experiments that examine first-order, second-order, and multiple factor effects simultaneously with relatively few simulation runs. They used about 100 runs to optimize the design, which took on the order of 1 day each. The result is that the analyst can iterate to a globally optimized design with a far higher level of certainty and in much less time than the traditional approach.
The following are some of the design factors and resulting responses that were evaluated with Kodak’s DOE approach:
Factors: | Responses: |
Chamber height Nozzle plate thickness Nozzle shape Reservoir impedance Heater size | Drop volume Drop velocity Drop quality Maximum firing frequency |
Kodak researchers developed a series of D-optimal designed experiments that explored the design space. These experiments determined how key performance parameters such as the drop volume and drop velocity change with respect to the geometry parameters. Kodak researchers used coarser computational meshes early in the design process in order to evaluate many alternatives in the least possible amount of time. As the design began to stabilize they moved to finer computational meshes in order to increase the accuracy of the simulation results. In addition to the numerical results, the graphical output of the simulation was very useful in helping researchers derive insights by visualizing flow fields and free surfaces.
By using DOE to drive CFD, Kodak researchers were able to optimize the design of the print head in considerably less time than competitors. The advantages of simulation were especially apparent late in the project when researchers discovered a more optimal ink formulation for one of the colors. The ink was quickly reformulated to capitalize on these advantages and since researchers had already run sensitivity studies on the ink properties, they quickly determined that the existing print head design would work fine. The EASYSHARE family of printers was thus launched only three years after the project was initiated, in approximately one-third the amount of time typically required to bring new inkjet technology to market.
More Info:
Flow Science Inc.
Santa Fe, NM
Kodak
Rochester, NY
Christopher N. Delametter is a senior research scientist at Eastman Kodak Company. To comment on this article, send e-mail to [email protected].
Subscribe to our FREE magazine,
FREE email newsletters or both!Latest News
About the Author

DE’s editors contribute news and new product announcements to Digital Engineering.
Press releases may be sent to them via [email protected].
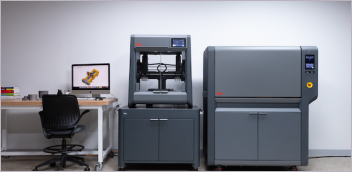
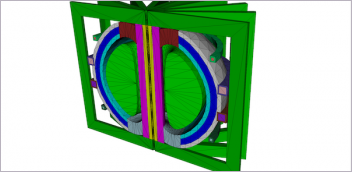
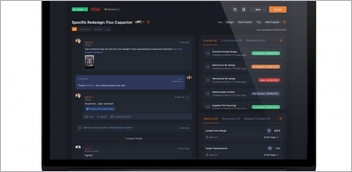
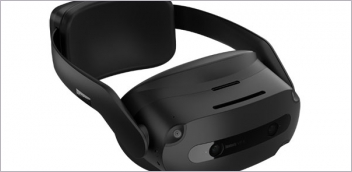