Latest News
January 3, 2010
By Victor Nelson
Quality assurance at Force10 Networks, a pioneer of high-performance data and communications networks, is an imperative. The company’s customers count on their high-density 10-gigabit ethernet switching, routing, and security networks solutions, with up to 5,000 components on a board, to be fail-proof and cost effective.
![]() SigmaQuest pulls data from each phase of the manufacturing process and provides real-time alerts when products or processes go awry. Issues are caught early in the process, resulting in lower overall manufacturing costs and the shipment of higher-quality products to customers. |
To ensure its products were consistently of the highest quality, the company sought a solution to get real-time quality insight during and after product manufacturing. The quality management team couldn’t afford to wait weeks to get reports containing only summary data (e.g., statistics on how many devices passed). It required real-time insight into the manufacturing process without having to wade through long, hard-to-interpret reports. In particular, Force10 wanted faster access to valuable parametric data, in-circuit testing, and X-ray data. The company also sought more in-depth test station information such as pass-fail rates, numbers of tests completed, and a listing of tests that were skipped including how often, when, and why.
Essentially, Force10 wanted at-a-glance, easy-to-understand feedback, with drilldown capabilities on its products that have more than 1500 test points each. To get there, Force10 turned to SigmaQuest, a provider of on-demand product quality management software for meaningful data, real-time reports, and its easy-to-use dashboard.
Improving Yields
Accurate yield information is another imperative at Force10. The company had experienced a not-too-uncommon scenario whereby its contract manufacturers’ (CMs) data didn’t seem reliable. The CM previously claimed 90+ percent pass rates of boards following in-circuit test (ICT) and 5DX (automated X-ray inspection). The CM only provided pass-fail data, leading to operator interpretation and guessing.
Rather than analyze the CM’s pass-fail data feed, Force10 leveraged SigmaQuest’s SigmaSure suite of software with automatic data collection, powerful root-cause analysis, and the means to quickly find, fix, and avoid quality issues. The On-Demand software pulls data directly from any automatic tester source, providing its own pass-fail data along with parametric data.
SigmaSure indicated that a significantly higher percentage of the boards had actually failed. It also provided limit information on components in the board that failed. For example, if a particular resistor is expected to operate at 7 ohms, SigmaSure shows the number of resistors below the lower specification limit of 4 ohms and above the upper specification limit of 10 ohms. From there, the serial numbers of the boards with failing resistance values can be pulled and the defective resistors can be easily replaced.
![]() The SigmaSure dashboard provides real-time measurements with drill-down analytics. |
SigmaSure automatically generates e-mail and pager alerts, flagging issues that need investigation. The alerts go out when the process-indicator limits or thresholds have been violated. For example, when target yields are outside of acceptably determined limits (e.g., below 95 percent) an alert is activated. Since this information is presented in real time—as opposed to several weeks later—plant managers can solve problems quickly, significantly reducing rework and remanufacturing time as well as cost.
Improving Quality and Product Cost
At one time, a certain percentage of Force10’s line cards were failing. With SigmaSure, Force10 found that a component was being placed in the wrong location. Measurement data showed a different performance characteristic as compared to data from a properly installed component. From here, Force10 quickly tracked the lot of products that weren’t assembled correctly and revised them prior to shipment to customers.
In another situation, the plant team was reporting excessive “false calls” amounting to more than several thousand a month. (Operators often visually inspect boards after test and can assume an issue is actually a “false call.”) SigmaQuest’s failure Pareto charts and drill-down capability depicts relationships between failures at particular locations on the boards to defects reported at X-ray. As it turned out, a percentage of the defects were real and shouldn’t have been characterized as a “false call.” As the software pinpoints the root cause, these issues can then be resolved prior to shipping products to customers.
The software identifies key product failure stats such as 30 percent of components installed into slot 45 failed. From there, it shows the percentage of components, in the slot, that are indeed defective as a result of being soldered incorrectly, placed sideways, etc. When defects can be identified at X-ray, this results in savings of tens to hundreds of thousands of dollars.
Another intriguing issue arose as a result of an oscillator placement on boards. The issue was tricky to diagnose as three oscillators were being used in each printed circuit board. They worked initially, but started to fail within a week of use in the field. The high failure rates were an unusual circumstance as the supplier had been delivering high-quality products for years. Force10 learned that the oscillators’ crystal blanks were not properly etched. By reviewing the underlying data via SigmaSure, the team quickly found other boards showing the same characteristics as the defective products that had initially passed ICT. From there, the software quickly located the serial numbers of the boards that had the defective oscillators. The components were replaced with good parts and retested prior to shipping additional products. Also, Force10 was able to identify the units that had been shipped and fixed them quickly.
As companies strive to manage costs, they want to avoid bringing on more test stations, particularly as fixtures can cost more than $100,000 each. As SigmaQuest identifies how many hours each station is used each day and tracks the amount of time it takes the station to test each product, Force10 determined it had unused capacity and that it could run its existing test stations for more hours, saving on costs.
Quality Tracking for the Entire Team
SigmaQuest’s SigmaSure gives CXOs to plant engineers and CMs real-time access to manufacturing, return material authorization, and test data. Information is presented via a dashboard with drill-down analytic capabilities. Teams are then notified if, when, and where products and processes go awry.
By leveraging SigmaQuest’s SigmaSure On-Demand software, Force10 has improved its quality operations and significantly reduced scrap. Moreover, customers are satisfied when returns are kept to a minimum. Better yet, Force10 has cut manufacturing costs by 20 percent, reduced customer returns by 40 percent, and eliminated $5,000,000 in service repair costs over the past four years.
More Info:
Force10 Networks
Victor Nelson served as head of quality and manufacturing operations at Force10. He is currently managing partner at Axiom Associates. Send comments about this article to [email protected].
Subscribe to our FREE magazine,
FREE email newsletters or both!Latest News
About the Author

DE’s editors contribute news and new product announcements to Digital Engineering.
Press releases may be sent to them via [email protected].
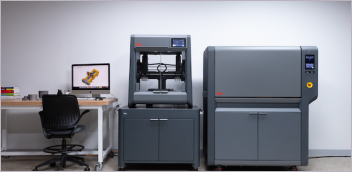
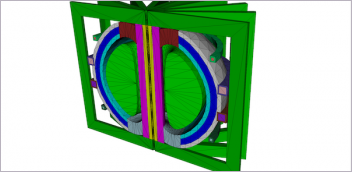
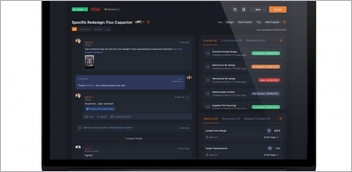
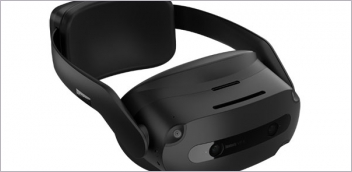