Jaguar: Style and Quiet Power
LMS helps Jaguar maintain its brand, enabling engineers to combine luxurious silence with a powerful ride and first-class handling.
Latest News
July 1, 2010
By Jennifer Schlegel
Jaguars are known for power, style, quality, and—most importantly—driving dynamics and comfort. It’s a clear brand image Jaguar has maintained for decades by giving its expert engineers leading-edge automotive technology.
![]() |
A case in point is the chassis and suspension design of the XJ series, Jaguar’s flagship full-size sedan. A third-generation XJ was introduced in 2003 with a ground-breaking aluminum body and chassis that minimizes the use of heavier steel parts.
The aluminum design is 60 percent stiffer and 40 percent lighter than comparable all-steel vehicles, translating into improved fuel economy and handling. Furthermore, a Computer Active Technology Suspension (CATS) system constantly monitors and tunes the car’s four-wheel independent double-wishbone suspension to match driving conditions, automaticaly adjusting for maneuvering, responsiveness, and comfort.
A redesigned XJ is underway. A key goal of the project is to optimize the design of the chassis to maintain current ride and handling behavior while further reducing interior noise. Historically, traditional prototype testing performed late in development was used to eliminate road noise, but time constraints limited what engineers could accomplish with this trial-and-error method.
Building full vehicle concept models
To ensure an efficient process and successful project outcome, Jaguar opted to work with LMS Engineering Services to perform a systematic multi-attribute optimization of the vehicle chassis. The multi-attribute optimization process required engineers to create full-vehicle concept models to predict different functional performances for road noise as well as ride and handling. To reach the target noise levels and maintain precise handling, engineers optimized and balanced the functional performance quickly and efficiently.
The road noise model was a hybrid representation consisting of test-based and simulation-based building-block sub-models assembled in LMS Virtual.Lab Noise and Vibration using a frequency response function (FRF)-based sub-structuring method. The chassis sub-frame (including all the different suspension connections) and the various suspension links were represented as flexible-body finite-element analysis (FEA) models. For computational efficiency, these FEA models were reduced to modal representations. The car body (frame, doors, side panels, etc.) was a test-based representation created from FRF measurements taken by LMS Test Lab. A revolutionary test-based NVH tire model unique to LMS was derived from FRF experimental data, along with three-degree-of-freedom road displacement measurement data.
![]() The hybrid full vehicle road noise model in LMS Virtual.Lab contains test-based representations of the tires, body and road displacements as well as a simulation-based representation of the chassis sub-frame (including all the di erent suspension connections). Image courtesy of LMS |
New test-based tire model
In order to respond to the automotive industry’s need for accurate representations of road-induced input forces on the vehicle structure (an input that remains the same regardless of suspension or body design configuration), LMS engineers developed a NVH tire model. A physically correct tire representation can achieve accurate predictions of structure-borne road noise in the early vehicle development stages when prototypes are not available for measuring the forces or resulting noise.
Traditional automotive industry methods for handling road noise phenomena involve applying experimental spindle forces or vertical displacements to the tire patch. Each method has limitations with respect to absolute accuracy or input dependency on suspension characteristics. For an accurate design evaluation, an invariant input that can reproduce measured vehicle cabin response is required. This is why LMS decided to develop a new NVH tire model derived from experimental data along with three-degree-of-freedom tire patch input displacements. When coupled with a vehicle model, road noise can be predicted accurately up to 300Hz, enabling virtual testing of suspension and body design changes.
Tire manufacturers typically make modal models available to the vehicle OEMs, but effects such as wheel rim flexibility and cavity acoustic effects are not included. Fully meshed FE models have been created to include these effects, but a high level of accuracy is difficult to achieve.
“For these reasons, an experimentally derived NVH tire model is an attractive approach,” explained Joris Van Herbruggen, vehicle development manager at LMS Engineering Services. “When the NVH tire model is coupled with representations for road displacements, sub-frame, body, and chassis in a full vehicle model, road noise can be accurately predicted for frequencies up to 300 Hz.”
Multi-attribute optimization
LMS and Jaguar engineers worked together to create a full-vehicle ride and handling model for predicting handling and steering feel during steady-state cornering, step steer inputs, double lane changes, and other vehicle maneuvers. LMS Virtual.Lab Optimization correctly adjusted these models using a Design of Experiments (DOE) process to determine various “best of” chassis parameters.
According to Van Herbruggen, thousands of different chassis parameter combinations were explored. It let engineers find the “best-possible” optimized road noise using a target curve while keeping handling performance within specified boundaries. The final result was a set of modified chassis design parameters and the study’s predicted road noise levels were lower by as much as 2 decibels.
More Info:
Jaguar
Jennifer Schlegel is senior editor at LMS International. Send comments about this article to [email protected].
Subscribe to our FREE magazine,
FREE email newsletters or both!Latest News
About the Author

DE’s editors contribute news and new product announcements to Digital Engineering.
Press releases may be sent to them via [email protected].
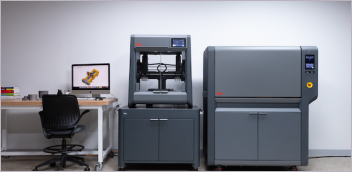
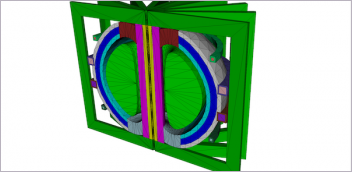
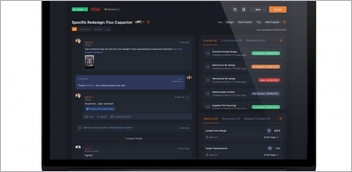
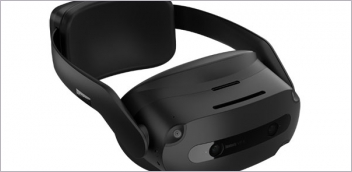