Latest News
July 2, 2008
By Erin Hatfield
![]() Flux density plot displayed on a quarter model of a brushless motor stator. The rotor turns withinthe stator, which is cooled by air at the outside of the assembly. (Image courtesy of Infolytica) |
Automakers are offering customers ever more choices these days with the advent of hybrid car designs that combine gasoline and electrical power. In order to make these new-generation cars more efficient, brushless permanent magnet (BPM) motors are used to set the hybrids in motion. While the BPM motors help with efficiency, they present unique design challenges when used in larger applications such as cars. Heat buildup is a common occurrence and most often causes the motor to fail — permanently.
To help solve this problem, motor designers need new tools to better simulate coupled temperature and electromagnetic properties to get a clearer picture of the role heat plays in BPM motor degradation. Such tools are already being developed by Infolytica Corporation to determine exactly how much heat a BPM can take.
Brush Twice Daily
Traditional electric motors require an armature (or rotor), commutator, brushes, axle, field magnet, and a direct current (DC) power supply. Most often, the rotor is an electromagnet and the field magnet is fixed, or permanent. The magnets in the motor create motion caused by the attraction and repulsion of a magnet’s north and south poles and a change in electrical current running across the rotor. This change in electrical current is achieved when the commutator contacts, which are small metal wires, touch the brushes. Changing the electrical current at the precise moment when the opposite poles align creates a full rotation and enables free movement.
But brushes present a few problems that offset their simple setup — and otherwise cost-effective — manufacturing. Mainly, they eventually wear out. Brushes also generate sparks when making and breaking the electrical connection and generate a great deal of electronic “noise” that can cause interference with other electronics.
Enter the BPM motor, where the electromagnets are moved to the stator and the permanent magnets to the rotor. Brushless motors rely on electronic current from computer-driven transistors to charge the electromagnets as the shaft turns. Removing the brushes from the design enables the development of variable-speed motors for more precision and efficiency. Brushless motors also generate less electrical noise, making them ideal in applications such as computers that are sensitive to electromagnetic fields (EMF). These motors also last longer and can be loaded with additional electromagnets for more precision.
![]() This is a temperature profile of a quarter model of the stator after 20minutes of operation. |
Another benefit of brushless motors is they are easy to cool. Most are cooled by air since the stator, at the outer edge of the motor, needs the cooling, not the rotor. In traditional brush motors, the stator is surrounded by the rotor, which presents cooling challenges. The flexible cooling aspect of brushless motors lends itself to a number of designs and magnet configurations and virtually unlimited size options.
While the easy cooling aspect is a huge benefit of brushless motors, heat buildup is still a major concern for motor designers and manufacturers. At a certain temperature, the permanent magnets become demagnetized, an irreversible process that renders the motor useless. More efficient motor designs achieved through finite element analysis have lessened the problem, but to truly understand the temperature threshold — the temperature at which the magnets lose their functionality — the motor designs need to be explored through scientific visualization.
Visualizing the Heat
“Most visualization products show temperature as a function of time,” said Gilles Fillion, technical advisor with Infolytica. “But the question isn’t, ‘Is the motor hot?’ It is, ‘How hot is the motor when the magnets degrade?’ To best answer this question, both temperature and EMFs need to be measured.”
Infolytica Corporation, a Montreal-based provider of electromagnetic software for low-frequency devices, sought the answer to that question by modeling a typical brushless DC motor to show the interdependencies of EMFs and temperature on motor performance. Most importantly, the company wanted to show the convective heat link between the rotor and stator and how heat is transferred across the motor’s interior.
Infolytica engineers modeled a 11.2cm diameter, 10hp motor with a rotating speed of 1800rpm in its MagNet software. MagNet simulates EMFs in both 2D and 3D and contains tools for modeling, meshing, and solving static and time-dependent equations. The software also offers transfer options to ThermNet, an Infolytica product that simulates static and transient thermal fields and can be coupled with MagNet to show both EMFs and temperature changes with the same model using the same data set and boundaries.
The motor analysis allowed for differing time and temperature intervals, which were set at 20 seconds for the temperature run and 16.7ms for the magnetic run as temperature changes more slowly than electromagnetic frequencies. The time difference made a coupled analysis all the more important in order to fully compute the change in motor performance due to increased winding resistance and degraded magnetic properties.
Infolytica engineers first created a one-eighth model of the brushless DC internal permanent magnet motor. A mesh was then generated over the model’s surface for the analysis. Due to the symmetry of the motor stator and rotor, the model was quartered and the size further reduced with binary conditions. The rotor and stator parts were modeled separately, including individual coils, which were modeled so they would not intersect the neighboring coils.
“We had to make models that were more detailed than regular magnetic simulation requires,” Fillion said. “Thermal simulation calls for this information since the end windings on the rotor provide most of the surface area for the convective cooling of the motor.”
![]() The rotor, stator, and winding of an 11.2 cm diameter, 10hp brushlessmotor modeled in MagNet software from Infolytica. |
In order to create an accurate analysis, a mesh of the space between the rotor and stator was generated in MagNet at each transient time step. After the magnetic simulation was completed, the model was transferred to ThermNet for temperature simulation. ThermNet features a Convective Link Calculator that determines the coefficients of temperature of a rotating machine based on proven algorithms that take into account rotor speed, Reynolds number, and other flow properties. This analysis was then coupled with the magnetic results to recalculate the effect of temperature on the magnetic performance over time. Data transfer between the two programs was made easier by file organization — a small single file contains all of the data and solution information for a given simulation, allowing different people to work on separate aspects of a problem.
“Magnetic performance is greatly affected by temperature, so it’s important to go back and forth between the two programs,” said Fillion. “Most unidirectional solvers only generate data for one or the other, not both, and even when these are ‘combined,’ the results are based on the original data and don’t take the interdependence into account. Bidirectional solvers such as the coupled MagNet and ThermNet show how the relationship between magnetism and temperature evolves.”
Surprising results
The temperature and magnetic changes were mapped over the course of one hour and Infolytica’s coupled analysis showed some surprising results. The stator temperature started off hotter than the rotor and then reversed as the temperature of the rotor and permanent magnets increased. While heat equalization was expected, Infolytica uncovered a greater temperature difference between the rotor and stator than was previously known.
Furthermore, Infolytica was able to determine the exact temperature and time at which the magnets degraded — at 97 degrees C after a little more than two hours of runtime. This value will vary based on motor size, but these results can greatly help designers determine the best applications for each motor based on expected time in use. Coupled temperature and magnetic field simulation can also lead to optimized motor designs that will help shuttle away damaging heat.
“As greater efficiency becomes more and more paramount, coupled simulation will be the only way to get the best motor designs,” Fillion said. “With optimized permanent magnet motors, we can help machines of all sizes for all purposes run much more efficiently.”
More Info:
Infolytica Corp.
Montreal, QUE
infolytica.com
Erin Hatfield is a freelance writer specializing in computer graphics, IT, and software development topics. You can send comments about this article to [email protected].
Subscribe to our FREE magazine,
FREE email newsletters or both!Latest News
About the Author

DE’s editors contribute news and new product announcements to Digital Engineering.
Press releases may be sent to them via [email protected].
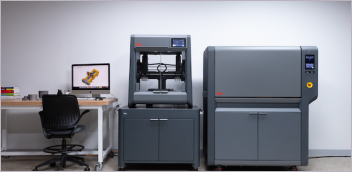
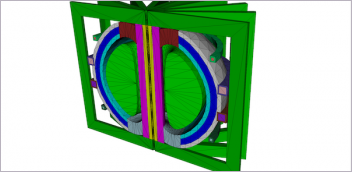
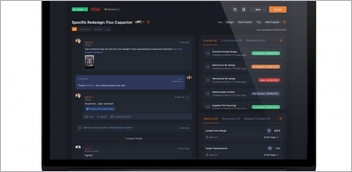
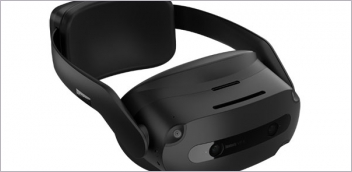