Modeling Explosions Using Harpoon and FLUENT
An oil company uses a third-party source with the tools to assess the strength of a blast wall on a new offshore platform.
Latest News
November 1, 2008
By Richard Bardwell
![]() This FLUENT plot simulates the gas cloud that would result from a major leak of process gas. |
Modeling hazardous scenarios has become an essential part of engineering design for offshore activities. Physical testing can be prohibitively expensive if not impossible, so modern computational fluid dynamics (CFD) techniques are commonly used to model exhaust-plume dispersion, natural and forced ventilation efficiency, flaring, hazardous spills, toxic gas releases, fires, and explosions.
Conducting and interpreting simulation research requires a substantial amount of specialist knowledge and so offshore organizations frequently outsource the task to dedicated companies. One such company is Abbott Risk Consulting (ARC) Ltd., an independent consultancy that provides services to the defense, transportation, marine, and energy sectors. The services include safety, risk, reliability, and environmental engineering assessments.
A major oil company recently approached ARC to conduct a fire and explosion risk assessment (FERA) on a new offshore platform design. As part of this assessment, engineers wanted to determine the magnitude and location of overpressures on a critical blast wall following an accidental flammable gas release and explosion.
![]() This is a Rhino 3D model of the offshore drilling complex under investigation. |
The large model, with a significant amount of detail such as piping and cable trays within the process area, presented a significant challenge to ARC’s existing meshing process. Traditionally, engineers would estimate blockage within these areas and implement a porosity model as opposed to meshing detail explicitly. However, due to the varying congestion within the immediate vicinity of the leak locations, ARC was concerned that the use of a porosity model could lead to introducing significant errors to the dispersion model and subsequently to the explosion model.
The oil company provided ARC with various 2D drawings and PDMS CAD data from which the model was to be constructed. After conversion and simplification in Rhino3D CAD, the model was exported in STL format ready for import to Harpoon, a meshing tool from Sharc Ltd.
“The use of Harpoon allowed the meshing of small detail, which significantly increased our and our client’s confidence in the results,” says Simon Feven, CFD engineer on the project. “The meshing technique used by Harpoon greatly reduced the time needed to manually process the model in CAD before meshing,” adds Feven.
![]() This surface mesh near the well head area shows the great detail possible in Harpoon. |
“For example, the intersection of equipment with the deck was handled gracefully and didn’t require a split or union operation to ensure a good quality mesh at the join.”
An additional advantage was that the geometry model could be updated as required by the client and re-meshed in a fraction of the time it would have taken with ARC’s other meshing tools.
“The study required many gas leak sizes and locations to be modeled. Each of these leak scenarios required unique meshes, which can lead to a high run cost,“ says Feven. “Using Harpoon allowed us to remain competitive, even compared to competitors that proposed simpler and more approximate modeling techniques, by automating the majority of the meshing process.
“Harpoon’s batch capability ensured that once the first mesh was created, the generation of the remaining meshes was trivial,“ Feven adds. “Once each mesh was created, Harpoon’s GUI allowed effective review of the produced mesh and evaluation of the mesh quality.”
![]() A cross-section through the Harpoon volume mesh within the process area. |
The key benefit that Harpoon offered was the hex-dominant meshing algorithm. This allowed fast refinement of the mesh to the fine level required to resolve the detail in the process area. The use of mainly hexahedral cells meant that fewer cells were needed to correctly resolve the dispersion of the cloud compared to the traditional method of using tetrahedral cells. Hence, modeling the increased detail was possible without significantly increasing the computational cost of the study.
Completed meshes were exported to the FLUENT solver for transient dispersion run analysis. An example of the maximum flammable envelope for one of the large leak scenarios is shown on page 50.
Various gas cloud dispersion scenarios were modeled within the hazardous areas by CFD. User-defined functions were written by ARC to transfer the resulting flammable clouds into the explosion solver, AutoReaGas (ARG) from ANSYS. Several explosions with varying ignition point locations were simulated to produce a full range of realistic scenarios.
![]() Plan view of peak overpressure contours predicted by AutoReaGas. |
The resulting overpressures were correlated with a leak and ignition frequency model to allow structural engineers to design the blast wall to withstand any likely explosions over the life of the platform.
Continued application of Harpoon to other projects has enabled ARC to significantly reduce the time required to construct a mesh from CAD data while increasing model quality.
More Info:
Abbott Risk Consulting Ltd.
Edinburgh, Scotland
AutoReaGas, FLUENT
ANSYS, Inc.
Canonsburg, PA
Harpoon
Sharc Ltd.
Manchester, UK
Rhino 3D
McNeel North America
Seattle, WA
Richard Bardwell is the CTO at Sharc Ltd. To comment on this article, send e-mail to [email protected].
Subscribe to our FREE magazine,
FREE email newsletters or both!Latest News
About the Author

DE’s editors contribute news and new product announcements to Digital Engineering.
Press releases may be sent to them via [email protected].
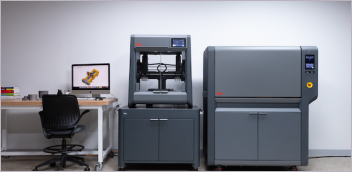
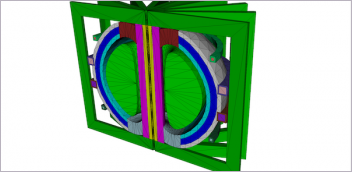
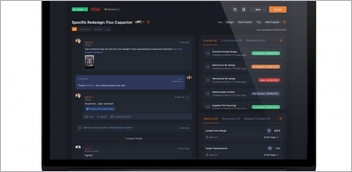
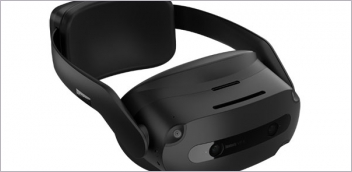