Motion Simulation Tools Part 2: Dynamic Solutions
From a simple kinematic design check to a large-scale nonlinear analysis, today's software gets you the details you need with improved ease and speed.
Latest News
March 2, 2009
By Pamela J. Waterman
![]() |
This article continues the discussion about software that helps you analyze the way mechanical assemblies rotate, slide, bend, and achieve their design goals. (See Part 1, February 2009.) Such tools reach ever farther in their ability to work with third-party packages, incorporate multiphysics interactions, and accommodate widely varying time-scales.
Tailored Solutions
Developers at MSC.Software agree that integrating various solver technologies offers a faster approach than using separate packages, and gets simulation technology out to a broader audience. The company’s latest motion-structures solution combines both MD Nastran and MD Adams within its MD Solutions. The latter supports native CAD files from CATIA, Pro/ENGINEER, and NX, and builds on both the Nastran and Adams lines of multi-body, functional virtual-prototyping solutions.
Recognizing that modeling an entire assembly with finite elements for a system response prediction can be cost-prohibitive, MD Adams includes a suite of targeted modules beginning with MD Adams/Basic Package, the core of the product, to first examine rigid-body motion. Users can then incorporate flexible component properties and easily transfer data to and from finite element analysis (FEA) applications such as MD Nastran using the flexible body simulation capabilities available in the MD Adams/Advanced Package.
Also available with the MD Adams/Advanced Package is the ability to simultaneously simulate mechanisms and control systems, such as for evaluating performance of a braking system with and without traction control. Dave Johnson, MSC.Software product marketing manager, notes that the package can be supported with toolsets and libraries specific to such industries as aerospace, automotive, and railway.
![]() | ![]() |
Sophisticated control logic enables industrial robots to operate. SIMULIA’s Abaqus analyzes movement in a closed-loop process to help define the necessary logic. Image courtesy SIMULIA |
SIMULIA’s approach with Abaqus focuses on the FEA, dynamic side of analysis but acknowledges the need for smooth, scalable connections between their analyses and basic motion simulation. David Fox,SIMULIA’s director of mechanics technology, says, “We’ve added joint constraints and the ability to turn deformable parts into rigid parts. Then you can run dynamics on an assembly, and get the same type of results as in a motion code, where behavior is dominated by mostly rigid motion.”
![]() LMS Virtual.Lab Powertrain Motion provides powertrain modeling templates that help users builddetailed behavior models of full assemblies or specific subassemblies. Image courtesy LMS Intl. |
The Abaqus/Standard package is suited to FE analyses where low-speed dynamics are involved, while Abaqus/Explicit can be applied to portions of an analysis where high-speed, nonlinear transient responses dominate. The combination offers a balance between the very high accuracy of a highly meshed, fully deformable analysis and optimized compute time (as fine-tuned with choices of material properties and DOF definition). Fox explains, “We have implemented the functions of motion simulation, such as nonlinear joint constraints, but without the mathematical reductions. This gives you motion simulation with large deformations and nonlinear material behavior that still includes inertia effects from fast motion.”
The structure of LS-DYNA, a generalpurpose multiphysics FE program from LSTC, permits users to tailor an analysis to both their data and their available computer resources. For example, rigid-body systems, defined only by the density and geometry of the bodies, can be inexpensively analyzed to obtain basic motion and load information. Such analyses will easily run on laptop computers.
Next in complexity are linear structural analyses, limited to small displacements, since they require only basic elastic constants. Results from these runs allow engineers to make sure their designs operate below the yield or failure stress of a given material. Designers can also increase the sophistication of the analysis by adding contact between parts to model pre-stress from such influences as interference fits and bolt tightening.
Lastly, the motions involved in automotive crash-worthiness calculations, routinely performed with LS-DYNA, reflect the high-end capabilities of the software. Rigid-body dummies must interact with large deformations in the vehicle structure, the latter modeled with more than a million elements generating more than ten million fully coupled simultaneous ordinary differential equations. The complete analysis must also incorporate material models for steel, rubber, glass, cloth, and composites; allow for contact almost everywhere; and couple fluid-structure interactions for airbag deployment. Not surprisingly, this level of analysis requires the power of computing
clusters.
![]() MSC SimEnterprise enables integrated motion-FEA solutions, operating with MSC SimXpert. Motion models include integrated flexible components for better full-system performanceprediction, as in this complete vehicle-performance simulation. Image courtesy MSC Software |
MOTION SIMULATION IN THE BIG PICTURE
LMS International markets an unusually wide-ranging family of software that incorporates simulation, physical testing, and virtual testing system-level behavior under real-world conditions. LMS Virtual.Lab Motion products focus on dynamics to analyze such characteristics as durability, noise, vibration, and acoustics. Some are FE-based while others use modal test measurements for input. Within the Flexible Bodies option, a number of FEA interfaces are provided-for such solvers as Nastran, ANSYS, and Abaqus.
LMS’ business model is clever in that once you’ve purchased the core software, you can buy generic “tokens” to access one of its dozens of specific application or task modules as needed. LMS has also embraced the inclusion of 1D modeling via its LMS Imagine.Lab solutions to optimize performance requirements across multiple domains (such as thermal management and control systems) and integrate them in a two-way exchange with 3D mechanism simulations.
Another company that has expanded its offering of analysis products is Cranes Software. Along with its subsidiary Engineering Technology Associates (ETA), the two companies cover both general-purpose and application-specific motion-simulation solutions. Within the NISA family of analysis products, the stand-alone NISA/DYMES package uses a mixed set of nonlinear differential equations to compute the time history of rigid multi-body systems, either for motions (kinematic) or accounting for forces (dynamic). These outputs can then be used to conduct stress analyses using NISA dynamic or static analysis modules.
Vipul Kinariwala, NISA product manager, says that a key feature of NISA/DYMES is its ability to complete inverse dynamic analyses. He explains, “If you want to design a control mechanism, to achieve a certain task, the software back-calculates for you—reverse engineering.” By identifying the limiting loading, in many cases this determines the type of control forces that may be required to achieve a desired performance.
To extend their analysis capabilities, Cranes’ ETA group markets, among other products, VPG/Structure, where VPG stands for Virtual Proving Ground. This software enables user to create systems including flexible bodies, combining kinematic/dynamic analyses with FEA methods. For example, users could investigate the behavior of a rigid system mounted on a flexible frame; today’s desktop computing power makes this task quite reasonable time-wise. As a bonus, legacy Adams models can be imported and converted to VPG models.
Offering a range of capabilities is also a recurring theme at ANSYS, which has been involved in flexible dynamics since 1972. Steve Pilz, senior product manager, says,“We’ll give you a tool that starts from 3D models and allows you to prototype your model, change designs parametrically, and analyze designs quickly. But we’ll also give you the tools that go all the way to the end, the full flexible transient dynamic analysis.”
ANSYS Rigid Dynamics is that tool, an ANSYS Workbench add-on to ANSYS Structural, ANSYS Mechanical, or even ANSYS Multiphysics software. It saves time in model troubleshooting by first analyzing a system as fully rigid with joints. Once a working rigid model is developed, users can readily convert parts of interest from rigid to flexible for a more comprehensive rigid-flexible dynamics simulation.
Pilz adds, “One aspect users love is ANSYS’ automatic joint creation. We read in a model, and say, based on the proximity of these parts, and what these parts look like, we’re going to assume that there’s a joint between this one and this one, of this type. Users can then modify the location or type. For a dynamics user this is as attractive as automatic contact creation is for an FEA user.”
Integrated within Altair Engineering’s HyperWorks CAE technology suite is Altair MotionSolve, a high-end analysis package that can assess designs with nonlinear dynamics, kinematics, linear, static, or quasi-static studies. Tailored for models containing a number of large flexible bodies, MotionSolve includes such advanced modeling elements as deformable curves and surfaces, general 3D contact (to simulate collision, rolling, or sliding behavior), pair constraints such as point-to-curve and point-to-deformable constraints, and nonmechanical elements such as sensors and user-defined algebraic variables.
Kshitij Kulkarni, Altair business development manager for multibody dynamics, acknowledges the need to work with a range of computational resources. He says, “Although in reality every system is dynamic in nature, the analysis can be idealized to a quasi-static ]no inertial forces] analysis if the mechanism is moving very slowly. This reduces computational cost.” MotionSolve also helps users save time by working with legacy models such as Adams and supporting bulk data file (BDF) transfers between FE and multibody dynamics domains.
An additional and powerful MotionSolve feature is the command file function. With this, users can activate or deactivate modeling elements at run-time and modify their attributes during a simulation run. The software can also handle flexible bodies undergoing large overall rigid-body motion; todo so, a linear deformation, modeled with mode shapes and modal states, is superimposed on top of the rigid-body motion. For initial model creation, users have two visual interfaces available, Altair’s MotionView modeling environment, streamlined for multibody systems, and the classic Hyper-Mesh preprocessor, both solver-neutral for broad industry use.
A Solution for Every User
Whether you need a simple kinematic overview of your system’s motion envelope or a full-blown nonlinear flexible multibody investigation, there’s a software analysis package just right for you. And remember that old saying, a picture is worth a thousand words? Motion simulation lends itself to terrific animations. Many of the companies mentioned in both parts of this article series have very insightful examples on their websites, so click away and take a tour.
More Info:
ANSYS, Inc.
Canonsburg, PA
Altair Engineering, Inc.
Troy, MI
Cranes Software
Troy, MI
LMS International
Troy, MI
LSTC
Livermore, CA
MSC.Software Corp.
Santa Ana, CA
SIMULIA
Providence, RI
Contributing Editor Pamela J. Waterman is an electrical engineer and freelance technical writer based in Arizona. You can contact her about this article via email sent to [email protected].
Subscribe to our FREE magazine,
FREE email newsletters or both!Latest News
About the Author

Pamela Waterman worked as Digital Engineering’s contributing editor for two decades. Contact her via .(JavaScript must be enabled to view this email address).
Follow DE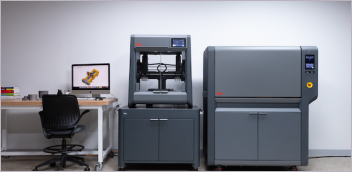
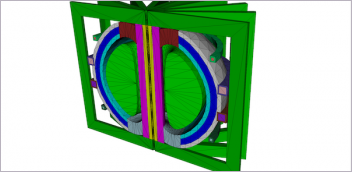
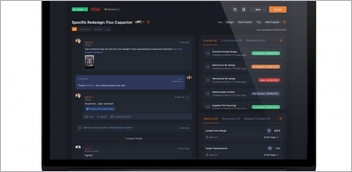
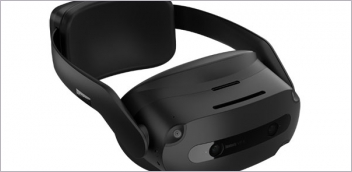