Nascar Goes Digital
How Geomagic and Pro/E Helped Richard Childress Racing fine tune their NASCARengines.
Latest News
November 1, 2004
By Bob Cramblitt
They call it stock car racing, but it’s anything but stock. By the time a NASCARmachine hits the track, only the outline of the car’s body conforms to the correspondingmodel on the showroom floor.
Some of the biggest changes are reserved for the engine. For teams such as RichardChildress Racinghome of Nextel Cup drivers Kevin Harvick and Robby Gordonthechallenge is to take the basic SB2 General Motors engine and squeeze out the mosthorsepower and torque possible within NASCAR rules.
One of the newest tools available to GM racing teams is an accurate 3D modelof the cast SB2 engine block created by Richard Childress Racing (RCR) using GeomagicStudio software from Raindrop Geomagic and Pro/Engineer from Parametric TechnologyCorp.
The new SB2 model enables GM and its racing teams to conduct FEA (finite elementanalysis) and CFD (computational fluid dynamics) studies based on an accuratedigital replica of the cast part. It also provides the foundation for creatinga complete digital engine assembly.
Foundation for HorsepowerThe SB2short for small block, second generationis the first engine GeneralMotors designed specifically for NASCAR racing. It simplifies preparation forracing teams, and reduces the overall cost of building and maintaining an engine.The SB2 was presented to NASCAR officials in late 1995 and won approval for competitionbefore the 1998 racing season. The engine was the latest version of the originalsmall-block V8 introduced in 1955, which had been modified for racing over theyears to work with each new cylinder head design.
The new engine is just the starting point for NASCAR teams that spend hundredsof thousands of dollars and tap into a treasure-trove of skill and imaginationto reach peak performance. The engine makes 800 horsepower and has carburetorsthat mix more than 800 cfm of air and fuel for engines that get about four milesto the gallon. That’s a lot of stress.
Digital Model ChallengesLast year, GM’s racing division asked Richard Childress Racing to create thefirst 3D digital model of the SB2 engine block. RCR was a logical choice for theassignment. The company was already using scanners and Geomagic software to reverse-engineercylinder head ports for its cars. It means they can improve performance in aboutone-sixth the time it took to do the work by hand.
Even with RCR’s experience, however, the SB2 project created a new set of challenges.
“The geometry of the casting, the shape, draft, water jackets, and internal cores,is complex,” says Clifton Kiziah, the senior design engineer who headed the project.
A logical starting point for a traditional reverse-engineering project wouldbe the 2D drawings. In this case, however, the 2D prints didn’t contain the wholestory because of changes made during construction that weren’t recorded or detailed.And RCR wanted to capture these changes as they appear in the finished part.
GM’s racing division asked RCR to create the first 3D digital model of the SB2engine block (above). The 3D model (below) was generated using eight surface filescompletewith datum planes, axes, and references created in Geomagic Studio, which wereimported individually into Pro/Engineer software, essentially simulating how ablock is physically machined.
Complicating matters further, the cast-feature shapes are difficult to reproduceusing direct CAD geometry, even after precise measurement. Radius rounds froman actual casting, for example, might be shaped like a spline rather than sphericalwith a single radius as depicted in CAD models.
“We wanted a model of what we have, rather than an idealization of what we thinkwe have,” says Kiziah. “The 3D model needed to match the physical block as accuratelyas possible.”
Accuracy for RCR means casting tolerances of 6.030 in. Anything less might compromisethe credibility of FEA and CFD testing results.
Removing Physical/Digital BoundariesMeeting RCR’s goals required software that would capture data from an actualSB2 engine block and turn it into a highly accurate 3D model. Geomagic Studiofit the description, but since it was being used by another group within RCR forthe head porting project, Kiziah would have to learn to use it on his own.
After consulting with Rob Black, an account engineer at Raindrop Geomagic, Kiziahdecided to send an engine block and a set of GM’s urethane molds of its internalcavities to Advanced Design Concepts (ADC), a Milwaukee-based scanning and reverseengineering company. ADC’s other clients for scanning and generating digital modelsfor complex parts include Fisher-Price Toys and Harley-Davidson.
ADC used a GOM ATOS white-light scanner to capture the core shapes and engineblock as eight separate point cloud files. The engine block was a 20MB file andthe cores were about 15MB each.
The point cloud files went back to Kiziah, who was beginning a two-day classto learn Geomagic Studio. He used the class as on-the-job training, turning oneof the point cloud files into his first 3D surface model.
Machining the Block in SoftwareAccording to Kiziah, the reverse engineering process was automated and logical.After bringing the point cloud files into Geomagic Studio, he thinned out thenumber of points with a uniform sampling operation. He then automatically createda polygon model, and repaired data holes to make it airtight. The polygon modelwas then converted to NURBS surfaces fine tuned by Kiziah.
The eight surface filescomplete with datum planes, axes, and references createdin Geomagic Studiowere imported individually into Pro/Engineer software. Thecores were assembled in Pro/E as they would be to cast an actual block, and acutout feature was used to subtract them.
“The critical datums created in Geomagic showed up in Pro/E, where they wereused as the foundation for the machining features on the block model,” says Kiziah.“In effect, we were simulating in software how a block is physically machined.”
Kiziah was able to achieve three times the accuracy required by casting, narrowingthe tolerances to 0.010 inch, and in some cases to within 0.005. And though hewas a novice with Geomagic, he completed the model much faster than if he hadto model it from scratch.
“It would probably have taken several months if we had to model it directly,and I’m not sure we would have been able to capture the complexity of the actualcast surfaces,” he says. “The finished model looks and measures the same as areal block.”
Computerized Fine TuningKiziah exported the final 90MB model of the engine block from Pro/E as an IGESsurface, so it could be imported into GM’s CATIA software.
GM and its racing teams now have an accurate digital model of the SB2 enginefor engineering analysis. RCR is preparing to use the model to run CFD tests tooptimize cooling, and secondary machining simulations to check for clearancesand fit of new parts. FEA simulations will be used to determine where materialcan be removed in secondary machining without affecting the strength of the block.
“Without accurate geometry, CFD, FEA, or secondary machining simulations cannotbe performed effectively,” says Kiziah. “When it comes to replicating cast parts,Geomagic Studio is the way to go.”
The SB2 engine block could be just the start for RCR’s digital modeling. Theteam is now working on a digital model of a complete car assembly, with surfacemodels of the chassis and the entire engine. At this rate, it won’t be long beforeRCR is staging computer-generated test races with exact digital replicas of itscars on virtual NASCAR tracks in its efforts to get into the winner’s circle.
Bob Cramblitt writes about computer graphics, IT, and other technology topics.You can contact him about this article at Desktop Engineering Feedback.
Product InformationPTC
Pro/Engineer
Needham, MA
ptc.com
Raindrop Geomagic
Geomagic Studio
Research Triangle Park, NC
geomagic.com
Subscribe to our FREE magazine,
FREE email newsletters or both!Latest News
About the Author

DE’s editors contribute news and new product announcements to Digital Engineering.
Press releases may be sent to them via [email protected].
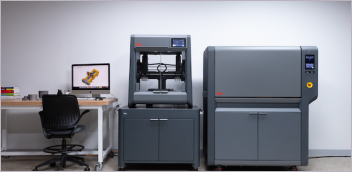
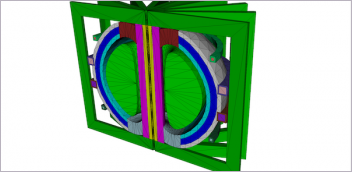
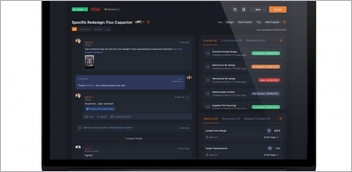
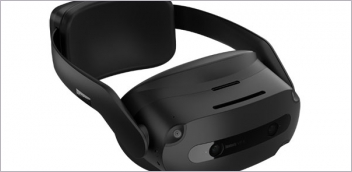