Prototypes for Clinical Trials Save Time and Money
Faster development cycle for electrotherapeutic device units cuts weeks off clinical trial.
Latest News
September 25, 2008
By Susan Smith
![]() An Ivivi device prototype, printed in hours on the Objet 3-D printer. |
Products that are developed for clinical trials in the medical profession require that a prototype be made for patient use that looks and feels like the real thing. Ivivi Technologies (Montvale, NJ) designs noninvasive, nonpharmalogic, electrotherapeutic devices which are electromagnetic in nature, to treat many conditions such as osteoarthritis and injured tissue. A small company of 25 employees, of which five are engineers, Ivivi’s focus is multidisciplinary. The company creates electronic and mechanical products that suit virtually all their development processes.
The Ivivi SofPulse is a patented pulsed electromagnetic field (PEMF) technology that generates a micro-current in injured tissues, jump-starting the natural electrochemical processes in the body. Why electrotherapies work is a new area of medical study that is being undertaken by some of the most esteemed scientists in the emerging field of electrotherapeutics.
The technology addresses health on a cellular level, as the electromagnetic response is inherent in all cells. Ivivi describes greater efficiency in aiding the activity of healthy cells. As with dominos, tapping the first domino sets off a chain of events that affects the other cells. The natural chain resets itself, and is ready to receive the next pulse from the Ivivi device.
The SofPulse, a patented, lightweight, embedded technology, can be worn over clothing. Contributing to the product’s success is a 3D printing system from Objet Geometries, the Eden 350. The Objet machine allows Ivivi to put their products into clinical testing very quickly.
According to Andre DiMino, Vice Chairman of the Board and Chief Technical Officer of Ivivi Technologies, the Objet allows them to produce a prototype unit of their non invasive electronic therapy devices that can be used in clinical trial. The way the clinical trial works is 100 people or so sign up and give feedback. Ivivi contracts with a university and specifies that they would like 80 patients tested, 40 with the placebo and 40 with the active device. Ivivi then provides to them the units made with Objet, which would produce the casing and the electronics put inside casing, to use to conduct the study. The majority of the devices are battery operated. “Patients can actually use it and it feels like a product that was made through injection molding.”
![]() A custom jig – printed on the Objet system – for finishing Ivivi clinical trial devices. |
Prior to acquiring the Objet 3D printer a year ago, Ivivi produced their conceptual drawings, then sent them out for stereolithography (SLA). The process provided a good representation of what the model would be like, but it was time consuming to make changes because Ivivi would have to redraw it and send it back out, then wait for it to come back, and it could take weeks in between the changes. The parts were expensive and could only be procured one at a time.
Further, DiMino said prototypes done in SLAs did not give you the feel of the actual produced unit. “We wanted to bring something in-house that would allow us to have a much faster development cycle which would cut the time down, but also if we got something that looked good we wanted to take it to the next step and actually put it into the hands of users for clinical testing, which is what we can do with Objet.”
According to DiMino, a big change occurred when they got the Objet, because they can now make a drawing, and from it, make the first units for testing. “If they looked good it was also very similar to what a final injection moulded piece would be like so we could then produce multiple copies of it,” said DiMino. “Once that was approved, we could then produce 20-100 units and put them directly into clinical trials so it shortened the development process tremendously.
Also, the cost of materials the Objet consumes are the company’s only costs now. “We’re not losing weeks, and sending it out for third party fees,” he explained. A change request made on Thursday can result in new units to ship to customers by Monday. “To be able to have a workable unit on a desktop within 48 hours is a dramatic change.”
In terms of materials, DiMino said Objet supplies a number of different materials such as VeroBlue and VeroWhite, from soft flexible materials to hard materials that are “just like” injection moulded polystyrene. Some of the products have a soft “over-mould” and the interior case will be made out of a harder material where the electronics go in. A softer piece will go on the inside for a cushiony feel.
![]() Ivivi’s André DiMino (left) showing an employee how the Objet system works. |
Ivivi also uses Objet to create the electrotherapeutic unit. Currently they are testing a unit designed for osteoarthritis of the knee. They produced the housing, a round shape that forms around the knee, and then put a velcro strap on the back, then embed the electronics into the housing. The button and window areas which display lights going on and off are also made with the Objet. The only thing not made by Objet are the circuit boards and circuitry, said DiMino.
Other uses for the Objet include making various tools and fixtures needed in the manufacturing process. Ivivi used to have the fixtures machined by a machine shop but now they draw it and make the tool themselves. The Objet machine is used at 60% of its capacity but DiMino said they hoped to fill that time up within the next six months.
DiMino has been involved in the medical device industry for more than two decades. “Looking back,” he said, “if I knew then what I know now, the decision to utilize rapid prototyping and the Objet system would be one of the easiest of my career.”
He added, “The Objet has easily cut five to six weeks off our clinical trial, and that’s a very conservative estimate. The machine has basically paid for itself in less than a year.” The additional savings from being able to develop new prototypes and make product modifications rapidly have not yet been quantified.
Ivivi Technologies
Montvale, NJ
Objet Geometries
Rehovot, Israel
Subscribe to our FREE magazine,
FREE email newsletters or both!Latest News
About the Author

DE’s editors contribute news and new product announcements to Digital Engineering.
Press releases may be sent to them via [email protected].
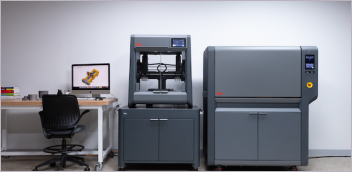
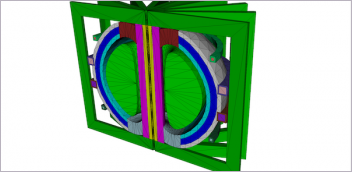
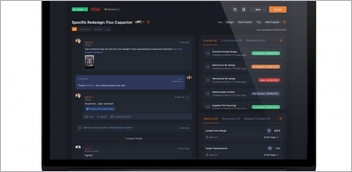
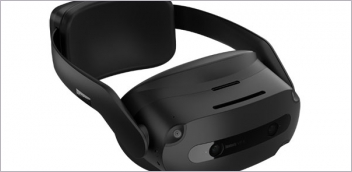