Latest News
January 11, 2008
By Jim Romeo
The Center for Occupational Health and Automobile Manufacturing (COHAM) is a laboratory specifically formed to study the biomech-anics of automobile manufacturing. The lab is located right next door to Ohio State University and is not far from Honda’s giant 8300-acre campus, which includes manufacturing engineering centers as well as several automobile and motor-cycle manufacturing lines.
![]() Computational biomechanics assessments study the risk of musculoskeletal injuries to which workers are exposed and leads to the redesign of existing jobs and the development of new work processes. |
The goal of this research center is to use cutting-edge computational biomechanics methods to analyze actual workers performing automobile manufacturing tasks in a real-world environment in order to understand the risk of musculoskeletal injuries to which the workers are exposed. By using quantitative assessment techniques, engineers help redesign existing jobs and develop new work processes. They are also able to examine the benefit of new production technologies as they emerge.
The staff at COHAM believes that this is the only facility of its kind in the world. To explore what this laboratory does, we spoke to Greg Knapik, one of the engineers at the laboratory who works on the use of software and technology to fulfill the mission of the research center.
CAN YOU TELL US WHAT ROLE SOFTWARE PLAYS IN THE ROLE OF THE LABORATORY?
Knapik: Our lab is extremely interested in quantifying the motions and forces to which the human body is exposed while doing work. As a result, we use a number of advanced sensor systems. These include goniometers to measure joint angles, electromyography to measure muscle activity levels, inertial motion tracking systems to record body movement, transducers to measure forces on the body, near infra-red spectroscopy to measure muscle fatigue, fiber optics to measure finger movement, and we even use an ultrasound measurement system to measure spinal curvature.
All of these sensors require a large contingent of software for data collection, processing, and analysis. This data is then combined into biomechanical models for assessing internal body reaction forces. This too requires a series of software packages to employ our models. Without the various software packages we employ, this type of quantitative analysis would be virtually impossible.
CAN YOU TAKE US THROUGH WHAT KIND OF SOFTWARE YOU NOW HAVE AND EXPLAIN ITS FUNCTIONALITY?
Knapik: Our studies begin with the experimental data collection. For this purpose we have developed an in-house software package, called Laboratory Information Management System (LIMS), which forms the backbone of our biomechanical modeling.
![]() Greg Knapik, an engineer at the Center for Occupational Health and Automobile Manufacturing, demonstrates a biomechanical model using the Laboratory Information Management System (LIMS). |
This software coordinates and synchronizes the data collection from our various sensor systems through a data acquisition board with a single user interface that — in real time — displays the collected raw data onscreen along with video of the experiment from an attached webcam.
Within the user interface, the entire data collection can be planned and coordinated with a built-in study designer that allows the user to select the sensors to be used, the tasks to be recorded, and the number of repetitions of each task.
The study designer then builds a data collection script for the user to follow. The experimental trials can then be collected and are appropriately labeled to aid in organization for later analysis, which is extremely important as we currently collect as many as 100 separate trials during a typical data collection.
As we have integrated new sensor systems into our data collection regimen over the years, we have had to make numerous updates to LIMS. Many new sensors come bundled with their own data collection software and operate independent of our data acquisition boards, so in order to integrate and synchronize them with our other sensors we have had to modify LIMS in order make it cooperate with this other software.
After collecting the data, the electrical signals from all of the various sensors have to be turned into data with physical meaning such as velocities, accelerations, or force measures. This too is done within LIMS.
![]() Solving ergonomics issues using software for biomechanics is a large part of the mission for the Center for Occupational Health and Automobile Manufacturing. |
This data is then applied to the biomechanical models we have been developing over the years. These models are able to take all of the external sensor data we collect and use it to determine the internal forces being imparted to the body, in particular to the intervertebral discs in the spine. These forces can then be compared to cadaveric tolerance limits or between different trials to assess risk of musculoskeletal injury. All of this modeling is also done within the LIMS software.
More recently, in order to be able to model different types of exertions and to examine different structures in the body in more detail, we have begun using MSC.Adams with the LifeMOD plug-in. Adams is a motion simulation solution for analyzing the complex behavior of mechanical assemblies. We have been able to embed our existing biomechanical models into the Adams software environment. This requires a large amount of coordination between our existing LIMS software and Adams.
To facilitate this we use MATLAB to help with data preprocessing and to coordinate the flow of data to and from the different software packages. In addition, we use MATLAB to postprocess the data before sending it on to a statistical analysis package like SAS for further analysis.
HOW DID THE DEVELOPMENT OF THE SOFTWARE COME ABOUT?
Knapik: The LIMS data collection, processing, and analysis software was developed for a number of purposes. First, the volume of input data and amount of processing had become too difficult to perform by hand. At the time we were collecting 25 channels of data at 1000 Hz each for about 10 seconds for each trial and as many as 50 trials per data collection session. Automating the processing made this feasible in a timely manner, and has become even more important as we add more sensors and look at increasingly complex activities.
Second, the biomechanical model had become so complicated that there was concern that performing all of the calculations by hand could result in human error. Automating the process all the way from data collection to analysis eliminated that worry. And third, by bringing all of the functions into a single user-friendly, turnkey system, it was much easier to learn, and simplified the data collection and analysis process.
WHAT WERE SOME OF THE BIGGEST OBSTACLES IN DEVELOPING YOUR OWN PORTAL OR CONGLOMERATION OF SOFTWARE FOR BIOMECHANICAL USES?
Knapik: The biggest problem during development was version control. The biomechanical model is and was constantly evolving and determining when to freeze the development and put it into code form was difficult. To eliminate potential difficulties, it was designed to allow for future expansion as our capabilities and needs changed. These extra capabilities have paid dividends as we continue to advance.
IS THERE “OFF-THE-SHELF” SOFTWARE AVAILABLE SPECIFICALLY FOR BIOMECHANICAL APPLICATIONS?
Knapik: Adams/LifeMOD modeling software is commercially available and has been used for other biomechanical applications. In addition, many of the advanced sensors we use in our studies come with their own software that allows them to be used independently.
CAN YOU GIVE US SOME ANECDOTES OF HOW YOUR SOFTWARE HAS SOLVED PROBLEMS?
Knapik: We have used our software to tackle a wide variety of biomechanical problems. Initially it was used to study basic biomechanics like lifting, carrying, pushing, and pulling. It has also been used to examine specific industrial tasks.
We have studied warehouse workers, aircraft baggage handlers, underground miners, railroad workers, patient lifting and handling done in hospitals and nursing homes, seat comfort, industrial spray paint gun use, the ergonomics of office work, grocery store check stand and scanner design, cell phone use and discomfort, as well as the work we are currently doing at COHAM in automobile manufacturing. We have even used it to look at more abstract problems like the impact that mental workload, stress, and even personality have on the mechanical loads in the body.
WHAT ADVICE DO YOU HAVE FOR ENGINEERS DEVELOPING SOFTWARE FOR UNCONVENTIONAL APPLICATIONS?
Knapik: I think it is extremely important that any software developed for a non-conventional application such as ours is very flexible. We are constantly undertaking new studies that have very different goals and analytical difficulties, while at the same time constantly integrating new sensor technologies.
The flexibility of all of our software packages and the way they are employed cooperatively has allowed us to keep pace with our changing experimental needs. Placing unnecessary restrictions on a software package’s use or ability to communicate with other outside packages inhibits capability expansion and usefulness.
WHAT’S THE NEXT CHALLENGE FOR YOUR LAB?
Knapik: Our lab is constantly looking for new ways (be they software or hardware solutions) to quantify the risk to which the body is exposed during work. So much time and effort has been put in to making our current core model software combination that any new leaps in software that come along will most likely just be added to our existing framework.
I imagine that any new software we will be adding into the fold will most likely be the result of some kind of new sensor technology with its own unique processing demands.
More Info
COHAM
Ohio State University
Columbus, OH
coham.osu.edu
Laboratory Information Management System (LIMS)
Honeywell
Phoenix, AZ
honeywell.com
MATLAB
The Mathworks
Natick, MA
mathworks.com
MSC.Adams
MSC.Software
Santa Ana, CA
mscsoftware.com
Jim Romeo is a freelance writer specializing in industrial technology topics. To comment on this interview, send e-mail to [email protected].
Subscribe to our FREE magazine,
FREE email newsletters or both!Latest News
About the Author

Jim Romeo is a freelance writer based in Chesapeake, VA. Send e-mail about this article to [email protected].
Follow DE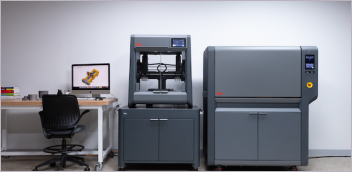
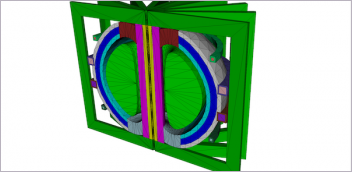
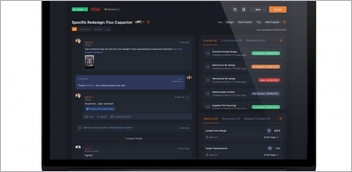
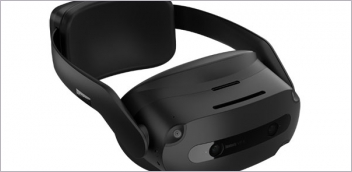