Latest News
May 30, 2009
By Steve Robbins
![]() |
I couldn’t help gravitating toward the Paul Bunyon-sized martini glass that was drawing the attention of many engineers at the SME Rapid 2009 event last month in Schaumberg, IL. After wondering where the gin was, I started to think the size of that martini glass might represent the expanding capabilities and opportunities of rapid technologies.
While the show might have had fewer attendees than last year’s due to our current economy, the engineers I talked with all had strong reasons for being there. Many were from smaller companies already using rapid prototyping, rapid manufacturing, service bureaus, scanning, and reverse engineering, or had compelling reasons to start to. And they were there to talk to the many rapid technology vendors who presented a slew of interesting products and demonstrations.
It quickly became apparent that there were three themes running throughout this event that all design engineers should be aware of.
First was materials. Over the years we have all seen the leapfrogging hardware and software in the computer trade. First the chip manufactures produce a high-powered CPU that promises great benefit to the user, then software engineers jump to the challenge and create applications that take advantage of the processing speed. New and wonderful things happen. Pretty soon the software vendors tap out the capabilities of the new hardware and the cycle repeats itself. Moore’s Law in action. This is now happening in rapid technologies. Some of these materials will create new markets, and some will drive vendors to create new machines to take advantage of the materials.
Which brings me to number two on the list. The line between rapid prototyping and manufacturing is blurring. There were a substantial number of new exhibitors selling rapid services on the show floor, and their services are expanding and becoming universal. Twenty-four-hour turnaround is becoming more common. Prototyping be will assimilated into rapid manufacturing. Metal parts will be more common across all applications, as will coatings. Designs are looking much more like their traditionally manufactured counterparts. While the acceptance of medical devices, aerospace, and dentistry applications were the forerunners of rapid technologies, it will become commonplace for parts to be produced on demand. If you own a 1972 Boss 302 Mustang, you’re in luck. One-off parts for all manner of consumer items are easily manufactured. With short turnaround times and high quality, this makes huge economic sense.
The third theme is medical device applications. While these were numerous last year, they were ubiquitous this year. With scanning, better software, and materials, these applications are changing the world. Prosthetics are being manufactured that don’t just do the job correctly but are fashionable. 3D Systems is entering a joint venture with Scicon to produce aluminum and stainless steel parts and medical devices. Dental crowns and implants are becoming standard practice on additive technology platforms because you can produce more accurate parts in much less time while both the service provider and dentist earn a higher ROI.
Rapid technologies are getting great traction with engineers, and it’s not just about having a cost-effective 3D printer on your desk anymore (though that can be handy), it’s about a sea-change in our methods and manufacturing infrastructure.
By the way, BJB Enterprises promised the martini glass would be filled at the show’s close, and I was the first in line.
Steve Robbins is the CEO of Level 5 Communications and executive editor of DE. Send comments about this subject to [email protected].
Subscribe to our FREE magazine,
FREE email newsletters or both!Latest News
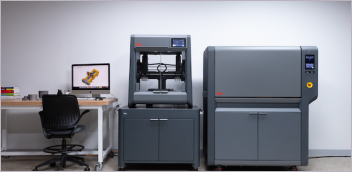
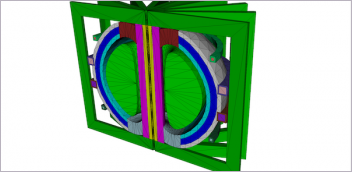
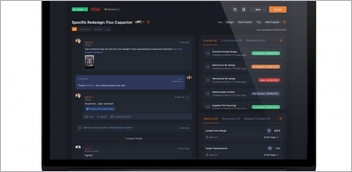
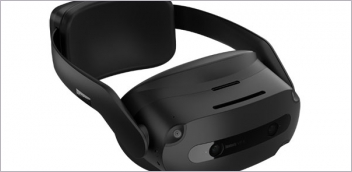