Latest News
August 1, 2008
By Nicholas Dewhurst
![]() |
It’s no secret that energy and material costs have increased as the value of the dollar has declined. Companies are scrambling to keep spending in line and remain competitive. Many have turned to suppliers and labor overseas, yet there is no better way to save product costs than by optimizing assembly tasks and manufacturing processes at the earliest stages of design when revisions are easiest and least expensive to make.
It’s also no secret to us and our customers that Design for Manufacture and Assembly (DFMA) software and methods help engineers save money. In 2000, we compiled more than 100 design case studies submitted by 56 manufacturers that use our software.
These companies, from all industries, compared DFMA-guided product assembly times and costs to those of the past. They reported average reductions of 60 percent in assembly times, 63 percent in manufacturing cycle times, and 50 percent in overall product costs. Eleven case studies included estimated annual savings that averaged more than $1.4 million per company.
What was true for these companies then is still true today: there is no better way to save money than by designing cost out of product development up front.
DFMA software is based on two complementary approaches: Design for assembly (DFA) and design for manufacture (DFM). DFA helps engineers evaluate the functional purpose of each component in a design, identifying unnecessary parts, quantifying how each part contributes to cost, and reducing complexity. DFM, on the other hand, identifies the expense drivers of manufacturing and gives engineers the means to assess the costs of a wide range of manufacturing processes and materials early on.
Frequently, an engineer’s own hard-won expertise can interfere. For instance, a designer with years of experience in molding plastics is less likely to consider stamping metal. Also, existing capabilities — in-house or otherwise — can seem more attractive than less well-known alternatives.We feel that by arming an engineer as early as possible with an extensive library of data for varied materials and processes he or she will be able to conduct an even-handed examination. It gives designers a comprehensive understanding of the costs to manufacture parts via different methods.
The software can also alert designers to potential manufacturing difficulties by pointing out that a wall is too thin for molding or an angle too acute for high-speed machining. The engineer can then alter individual design features to prevent delays.
In one example, an automotive manufacturer asked us to analyze a design for an injection-molded heater cover. DFM analysis revealed that the cover was thicker at three fastening points — a common way to ensure part strength. In this case, however, the extra material slowed the molding process and our review demonstrated ribs could be substituted. The change reduced manufacturing time and cut the cover’s cost by nearly half, potentially saving the company $2.25 million over the life of the product.
And yet DFMA does more than cut assembly and manufacturing costs. Implementing DFA and DFM can lead to savings in every aspect of product life. In fact, some manufacturers are just beginning to understand the extent to which redesigns can save on operations farther downstream.
Last year we conducted a second survey of customers and found that 68 percent of respondents measured increases in production throughput. Forty-seven percent documented increases in profit per unit of factory floor space, with one participant realizing a 300 percent-per-square-foot improvement by redesigning a product family.
While profit per square foot of factory floor space is one of the easiest and most meaningful metrics to gather, there are many other downstream areas where DFMA can lessen costs. But these are areas where companies fail to relate ongoing business expenses to early product-development activities.
Knowledge of cost-to-manufacture should be a design and management responsibility. It’s amazing how beneficial the results of such analysis can be — and how far downstream the financial benefits can extend.
Nick Dewhurst is the executive vice president of Boothroyd Dewhurst, Inc. Send feedback on this commentary to [email protected].
Subscribe to our FREE magazine,
FREE email newsletters or both!Latest News
About the Author

DE’s editors contribute news and new product announcements to Digital Engineering.
Press releases may be sent to them via [email protected].
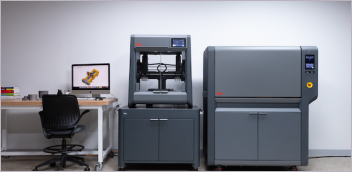
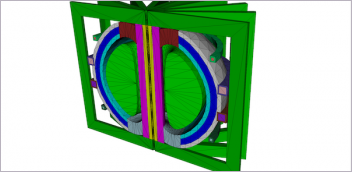
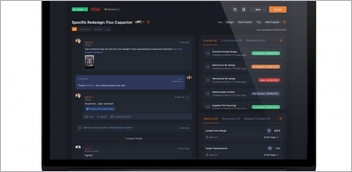
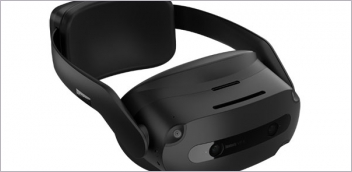