Rethinking Product Development: Insourcing RP & RM to Do More with Less
Making models, molds, and more on a $12K platform.
Latest News
December 1, 2008
By Tormach LLC
![]() Combined with the optional probe, the PCNC 1100turns into a powerful system for reverse engineering. |
Insourcing product development with flexible, in-house rapid prototyping provides a competitive advantage to businesses that want to position themselves for future success, regardless of economic climate. Many companies are finding that internalizing product development in lean times allows them to retain talented employees and promote a culture of creativity while cutting overall costs. In turn, they find themselves in a better position to respond when economic fortunes improve by virtue of a workforce that is already upto- speed with a basket full of new products waiting in the wings.
Tormach is bringing rapid prototyping and more within the reach for many small businesses, entrepreneurs, inventors, and R&D groups with the PCNC 1100. The PCNC 1100 is the first “personal” CNC mill. The idea is simple — build an affordable mill that can provide both the functionality and precision of an industrial vertical machining center and is easy to move, easy to learn, easy to use, and easy to maintain.
In the past, entry into 3D machining was prohibitive: the expensive cost of a quality CNC mill and the specialized CAD/CAM software needed to produce 3D geometries made CNC machining only feasible in a production environment operated by a skilled machinist. Tormach offers high quality value-priced CNC mills combined with powerful but affordable CAD/CAM to provide an “at-the-ready” 3D rapid prototyping solution for just about any budget. It’s been a successful approach that is being proven every day, often by those with zero“traditional” machining experience.
The advantages of the PCNC 1100 for rapid prototyping are significant. For one, it offers versatility: machinable wax or plastic can be used to quickly produce first-concept 3D models. The same machine can then be used to cut working prototypes out of plastic, aluminum, steel, carbon fiber, or nearly anything else. And unlike many of the other rapid prototyping systems, the PCNC 1100 is fully capable of being used for smallscale production or moldmaking.
In-house rapid prototyping can allow for nimble, low-cost design iterations. Relying on contractors to deliver revisions can be costly and time consuming. With the PCNC 1100, a small design change in a CAD drawing can be easily implemented via CAM and cut on a machine in the same day with virtually no out of-pocket cost.
Many businesses are also finding the PCNC 1100 indispensable for producing new fixtures for use in product testing and/or manufacturing. Affordable, in-house CNC capability is allowing these companies to quickly and cost-effectively produce custom jigs and tooling. They are able to react quickly, both to changes in test plans and unanticipated manufacturing problems, and are quickly able to repair or replace parts to minimize downtime.
The PCNC 1100 is empowering product development around the globe with the agility to bring ideas to market quicker and cheaper than ever before. It’s an affordable, versatile platform for rapid prototyping, rapid manufacturing, reverse engineering, and small-scale production that enables creativity and entrepreneurship. When it comes to product development, the PCNC 1100 is helping businesses of any size do more with less.
More Info:
Tormach LLC
Waunakee,WI
608-849-8381
Subscribe to our FREE magazine,
FREE email newsletters or both!Latest News
About the Author

DE’s editors contribute news and new product announcements to Digital Engineering.
Press releases may be sent to them via [email protected].
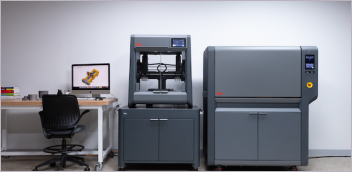
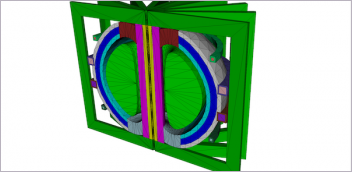
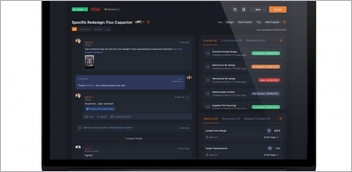
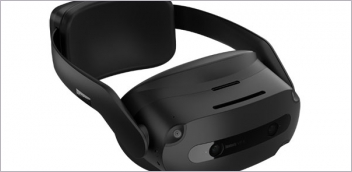