Latest News
September 4, 2007
By Bruno Massa
![]() LMS Test.Lab allows Autoliv to simulate the acoustics of the explosive charges used to inflate airbags in times of accidents and to determine how occupants’ hearing is affected. |
To evaluate the performance of airbag and seat belt systems — and measure the damaging noise they generate — Autoliv uses LMS test systems during crash simulations. LMS test systems also provide the vibration control of environmental noise measurements that are executed to evaluate individual safety products, such as seat belts, seat frames, and steering column assemblies.
Autoliv uses LMS Test.Lab because it incorporates reliable and stable measurement and analysis routines, works with high-precision data acquisition hardware, and includes a workflow-based user interface that eliminates possible human errors during the test run. It also helps reduce simulation times by enabling qualified test-based models of components and subsystems to be combined with virtual models of new components.
The company’s latest contributions to automotive safety include a new anti-whiplash seat, a side-impact airbag for chest protection, and an inflatable head-protection curtain designed for lateral impacts. Currently, Autoliv is developing rollover protection, night vision, and pedestrian protection systems. It is a supplier to all major vehicle manufacturers and most vehicle brands, and every year its products save thousands of lives and prevent many more severe injuries.
In the event of a car accident, a predefined sequence of actions is automatically initiated to protect the occupants of the vehicle. Thomas Norberg, laboratory manager at Autoliv, describes what happens at the onset of a crash:
![]() In dedicated acoustic test facilities, Autoliv engineers perform noise measurements inside vehicles equipped with fully integrated seat belt and airbag prototypes, and use up to five test dummies. |
Avoiding airbag explosion noise
As part of the development of new safety products, Autoliv invests significant research and development effort in reducing the noise generated by pyrotechnic initiator mechanisms because they may increase the risk of hearing damage. Apart from sound pressure levels, the human ear is very sensitive to the timing sequence that is applied to initiate the different safety equipment.
In general, a firm sound, for example from a pyrotechnic belt pretensioner initiator, activates the Stapidus reflex of occupants’ ears — a self-protective reaction that temporarily inactivates hearing capability after approximately 10 milliseconds. After this, it is unlikely that subsequent airbag initiator noise will further damage an occupant’s hearing and Autoliv is trying to make sure the first explosion activates the reflex without causing damage.
In dedicated acoustic test facilities, Autoliv engineers perform noise measurements inside vehicles equipped with a series of fully integrated seat belt and airbag prototypes and occupied by up to five crash test dummies. A dedicated trigger unit precisely executes a predefined trigger sequence to activate seat belt restrainers and airbag detonation. Microphones, integrated in all dummies’ ear positions, capture the noise generated by successively exploding initiator mechanisms and feed it to an LMS SCADAS III front-end data acquisition and analysis unit. Autoliv engineers then use LMS Test.Lab and LMS CADA-X test software to communicate and process the acquired data. The complete sequence of such tests is often recorded with dedicated video cameras.
Norberg explains that the recorded noise time signals form the basis for running dedicated frequency analyses that provide insight into maximum amplitudes and the most dominant frequency components.
“The main purpose of these kinds of investigations,” Norberg says, “is to examine the noise performance of different types of explosive materials as well as to fine-tune the mechanics of airbag initiator designs during the final stages of development. A specific proprietary algorithm is developed to convert the acquired test data of each microphone into one single numerical value that reliably reflects the risk of hearing damage. The use of this algorithm increases the efficiency and consistency of the evaluation process of the noise measurements, as it allows the noise performance of new design modifications to be quickly interpreted and compared with previous results.”
Eliminating safety equipment sounds
At Autoliv noise-test laboratories, engineers also focus on eliminating undesired sounds generated by other safety-related equipment, such as seat belts and seat frames, during their normal operation. Even the weakest noises produced by such systems negatively influence the comfort of driver as well as passengers.
![]() Autoliv’s testing with LMS Test.Lab demonstrates that testing throughput times are compressed as a result of the software’s flexibility and efficiency. |
These environmental tests can be quite relentless because the shaker system is able to excite more than half a ton of weight with accelerations up to 60G. In addition, the ambient temperature present can vary between -50 and +110 degrees Celsius. The purpose of these tests is to execute safety system benchmark tests and to drive development innovation.
Expectations met
Autoliv engineers compile the vibrations they apply to test specimens on the basis of accelerometer measurements taken on identical or similar safety equipment during road-and-track testing. In LMS Test.Lab, they perform random Power Spectral Density (PSD) calculations to convert the realistically acquired vibration measurements into representative and effective shaker table control.
To further increase the test capabilities of its noise test facilities, Autoliv extended its existing LMS CADA-X install base with LMS Test.Lab. Norberg summarizes how this affects testing operations: “For many years, we have relied on LMS test systems to accommodate our dedicated and varying testing requirements. Our experience clearly demonstrates that testing throughput times are compressed drastically.
“The associated productivity gains mainly result from the software’s higher flexibility and efficiency standards that help speed up test setup and postprocessing stages,” Norberg says. “Also, LMS Test.Lab’s process-driven application workbooks accelerate our repetitive benchmark testing activities and increase the involved data consistency significantly.
“Autoliv engineers consider high data acquisition accuracy, custom calculation flexibility, and reliable external interaction as the cores to further step up testing productivity and strengthen their commitment to realize optimum occupant protection,” adds Norberg.
LMS North America
Troy, MI
lmsintl.com
Bruno Massa is director of marketing at LMS International in Leuven, Belgium. You can send e-mail about this article to DE-Editorsmailto:[email protected].
Subscribe to our FREE magazine,
FREE email newsletters or both!Latest News
About the Author

DE’s editors contribute news and new product announcements to Digital Engineering.
Press releases may be sent to them via [email protected].
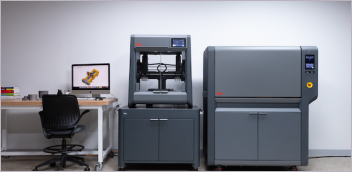
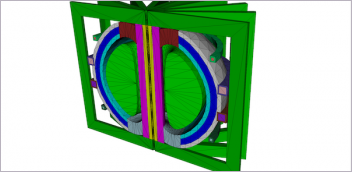
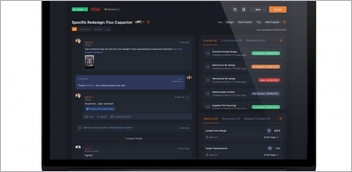
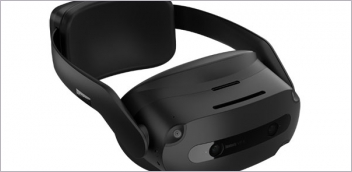