Latest News
January 1, 2005
By Louise Elliott
Once regarded as a pie-in-the-sky slice of science fiction requiring afull-face helmet-like headset, virtual reality (VR) is now fairlyeasily available, comfortable to use, and becoming affordable. In fact,it’s frequently used for product development in conjunction withCAD/PLM-based visualization solutions from the usual suspectsUGS, PTC,and Dassault Systemes.
In VR prototyping, the 3D image is often viewable with a sophisticatedset of glasses that imperceptibly shift the wearer’s vision from oneeye to the other using a rapid-fire shutter system synchronized to acomputer. The technology can be used on platforms ranging from $2,000PCs to four-, five-, or six-wall CAVE (Cave Automatic VirtualEnvironment) systems that can cost $400,000 and more for fullyimmersive visualization environments.

The results are amazingly lifelike and, in a CAVE or power-wallenvironment (a single or multiple rear-projection screen at least 20feet wide), viewable in 1:1 scale or larger. Because of this, thevirtual prototype provides information previously only available from afull-scale physical prototype and, in some cases, data formerlyinaccessible.

UGS’s Teamcenter Visualization software is being used for this flightsimulation in the CAVE (Cave Automatic Virtual Environment) at IowaState University’s Virtual Reality and Application Center.
A Few Examples
While most prevalent in the automotive and aerospace industries, VRtechnology has a home wherever very complex products need to besimulated. An example is the National Ignition Facility (NIF) projectunder way at Lawrence Livermore National Laboratory in Livermore,Calif. When finishedscheduled for completion in 2008the facility willbe the largest laser in the world (roughly the size of a stadium) andwill be used for studying nuclear fusion target theory for energyproduction. The huge laser will focus on a very small targetabout thesize of a BB gun pellet. The system itself will be very powerful, equalto 1,000 times the energy generating capacity of all the electricitygenerating plants in the United States, in very short bursts. Theequipment itself contains between 800,000 and 1 million parts.
To examine the subassemblies, NIF engineers use PTC’s Division Mockup,says Scott Myers, NIF senior mechanical engineer for SystemsIntegration. “It’s very vital for us to be able to fly through thesecomplex parts,” he says.
Often, the subassemblies have thousands of parts. Myers’ colleague JackWass reports, “It’s very important to make sure of clearances and avoidinterference, and to see whether the subassembly can fit into thefacility housing the equipment.” On occasion, when the equipment wastoo large, engineers had to redesign it in smaller units. “Thisequipment is ery expensive,” Myers says, “so we have to be absolutelycertain the parts will fit together and fit the facility beforemanufacturing anything.”
Dassualt Systemes’ ENOVIA V5 VPM and DMU product lines offercapabilities to provide manufacturers with full visualizations of alltypes.
Commercial automotive manufacturers don’t have as much time to designand build their products. Diane Jurgens, IT manager of StrategicPlanning and Benchmarking for General Motors, says that in its quest toget from concept to vehicle launch without problems ever occurring, thecompany uses virtual prototyping of many kinds. They include VRtoolsUGS’s Teamcenter Concept based on the JT file formatfor design,decision-making, and maintenance.
“At the conceptual design stage,” says Jurgens, “we use digital representationsof engineering constraints for the design teams and exchange digital prototypeswiththe aim of simulatingphysical and functional prototypes, so that physical prototypes justserve to verify our findings. We use virtual reality tools forhigh-quality aesthetic visualization, with stereo viewing for stylingand design.”
Decision-making takes place in “reality rooms” that display VR versionsof alternative vehicle designs in different settings. GM uses immersivetechnology in conjunction with real automobile seats and other physicalcues to decide on auto interiors. “Stereo viewing helps withserviceability as well,” Jurgens says. “We can see the clearance pathsfor removing and replacing parts.”
The State of the Technology
In its immersive versions, VR costs a great deal of moneymostly forthe projection system hardware and construction of the viewingenclosure. However, the software is also available for other, moreaffordable platforms.
The mockup at right uses Dassault Systemes’ DMU solution and helps amanufacturer and designer of jet interiors envision the final product.
“The software largely involves breaking up an image into differentangles of viewing for CAVE type viewing,” says Stu Johnson,visualization product manager for UGS’s Teamcenter Visualization. “Or,if using a 20-foot by 8-foot wall, it takes a single image and sendsdifferent chunks out to each projector. With a power wall, the numberof projectors can vary from one to almost any number. It’s possible tocreate a matrix of 64 projectors, with each one focusing into one smallspace for ultra high resolution.”
The single biggest area of recent improvement has been in graphicscards, Johnson says. “We’ve all benefited a great deal from the videogame developers; so much so, that we’re starting to see PC clusterscome into the virtual reality environment, replacing Unix platforms.”
Johnson believes that the availability of haptic devices now brings VRtools into manufacturing, making it possible to simulate someoneassembling a product, such as a circuit board, as a way to train peoplehow to do the actual assembly. Such use is currently being studied atIowa State University in Ames, Iowa.
Another Dassault Systemes ENOVIA V5 mockup helps engineers at Peugeot work outthe ergonomic kinks of a new minivan model.
Michael Rygol, senior director of Product Management for PTC’s Divisionproducts, believes that use of the technology is growing as peoplerealize that 2D renditions of 3D simply don’t tell the whole story.“Stereo visualizations on the desktop give a clearer idea of spatialrelationships. This kind of viewing is being used on shop floors and inmaintenance facilities, as well as for product reviews in engineeringdepartments,” he says.
“Between desktop and immersive platforms,” says Rygol, “today we havetools like the Holobench, which offers a three- or four-foot-squaretracked stereo system with one horizontal and one vertical screen.” Headds that Division Mockup now uses sound that’s embedded into thedigital image for stereo playback along with stereo viewing “forgreater realism.”
Rygol explains that VR systems can now add virtual human beings tovisualizations to help solve ergonomic issues. He pointed to an exampleof a Korean manufacturer of construction cranes who put a virtual “50thpercentile Korean male in the cab of the crane to see if he would beable to reach all the controls comfortably and safely.”
PTC’s MockUp product has even reached into traditional manufacturing.Here, a piece of Wedgewood china is manipulated against a diningroombackground by an engineer at Virtalis, a manufacturer of stereoscopichardware.
Dassault Systemes’ ENOVIA V5 VPM and DMU product lines have similarcapabilities to those described above. The tools, says Fabrice Pinot,marketing engineer for the product line, are currently in use for"realistic review and validation for decision support prior toinvestment in physical prototypes, early evaluation of product styling,and for marketing and sales purposes.”
Customers are also requesting such added capabilities as “larger data,loaded for removability studies; that is, to simulate parts beingremoved during maintenance, contact instead of clearance, multiple bodymechanisms, and human integration,” says Pinot. In this case, humanintegration includes simulation of forearm motions for themanufacturing floor
Greater Access in the Future
GM’s Diane Jurgens looks ahead: “I see a broad extension of thetechnology for multiple purposes, including data sharing insidecompanies and with suppliers. Everyone, everywhere will have access toexcellent visualization that has ever-better graphics.” That, in turn,spells a bright future for VR and virtual prototyping as designerscontinue to perfect their products before they see the light of day.
Contributing editor Louise Elliott is a freelance writer based inCalifornia. Offer Louise your feedback on this article through[email protected].
Companies Mentioned
General Motors
Detroit, MI
website
PTC
Needham, MA
website
UGS
Plano, TX
website
Dassault Systemes
Paris, France
website
The NationalIgnition Facility
Livermore, CA
website
Subscribe to our FREE magazine,
FREE email newsletters or both!Latest News
About the Author

DE’s editors contribute news and new product announcements to Digital Engineering.
Press releases may be sent to them via [email protected].
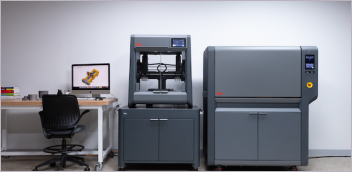
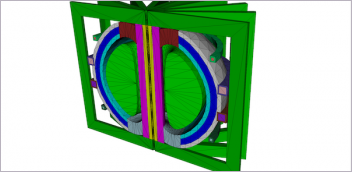
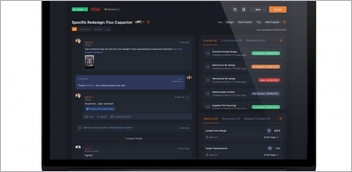
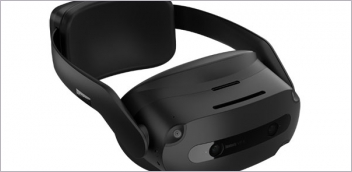