Latest News
April 22, 2008
By Jonathan Gourlay
Siemens PLM Software (Plano, TX) today announced what is being billed as “the next big breakthrough in digital product development” in a global webcast-phone conference during which its synchronous technology was discussed. Siemens PLM’s synchronous technology refers to an intuitive direct modeling technology further described as history-free and feature-based. It is expected to provide users with up to a 100-times faster design experience than before.
Industry media and analysts were invited to view an 18-minute prepared video and then join a web-based question-and-answer (Q&A) session with Siemens PLM Software Chairman and CEO Tony Affuso, President Helmuth Ludwig, and Executive Vice President of Products Chuck Grindstaff. The new application was developed in conjunction with D-Cubed and Parasolid technology and is said to simultaneously synchronize model geometry and behavior rules and gathers it all together in a single decision-making inference engine.
It combines constraint-driven techniques with direct modeling and is being integrated into the company’s next versions of both NX and Solid Edge solutions, expected to be available this summer. It is not, at least initially, being considered as a component to the solutions, but is an integral part of the modeling programs.
As described by Grindstaff during the Q&A session, the technology has great fluidity with JT data and has the ability to work in a multiCAD strategy. When asked specifically about any possible breaks between model geometry and CAM programs, Grindstaff said, “We’ve been working on this for years, it’s good to go.”
In creating this synchronous technology, Siemens PLM is hoping that all stakeholders in the product lifecycle will have the freedom to work with the geometry of a new product, make modifications, and add or edit key features without having to wait for their MCAD system to go back through the history tree and recalculate changes in a separate series of steps. With the new versions of Solid Edge and NX, all associative connections between features and sections of the model are maintained, so constraints and various other relationships are automatically remembered.
The aim is for designers to devote more time to innovation with new techniques that provide the “efficiency of parametric dimension-driven modeling without the computational overhead of pre-planned dependencies,” according to a press release. The technology defines dimensions, parameters, and design rules at the time of creation or edit, without ordering or reordering a history.
A key feature of the technology is that users will be able to edit other MCAD system data faster than they would in the original system, regardless of the design methodology. A technique called “suggestive selection” automatically infers the function of various design elements without the need for feature or constraint definitions. It is said to increase design reuse and OEM or supplier efficiency. It is also said to make 3D as easy to use as 2D. The engine merges the two environments, providing the robustness of a mature 3D modeler with the ease of 2D. New inference technology automatically infers common constraints and executes typical commands based on cursor position. This makes design tools simple to learn and use for occasional users, driving downstream use to manufacturing engineering and the shop floor.
This seeming hybrid environment represented by Siemens PLM’s synchronous technology will allow designers to model or make changes with features without the headache of recomputing using a history tree. “Traditional parametric modeling serially applies rules to geometry, helping to automate planned change but not addressing unanticipated engineering changes,” said Grindstaff. “History-less modeling concentrates on geometry in an unconstrained manner, but sacrifices intelligence and intent. Direct editing minimizes the need to understand a complex history but does not address features. ]This] incorporates the best of constrained and unconstrained techniques.”
For more information on today’s announcement, view a replay.
Subscribe to our FREE magazine,
FREE email newsletters or both!Latest News
About the Author

DE’s editors contribute news and new product announcements to Digital Engineering.
Press releases may be sent to them via [email protected].
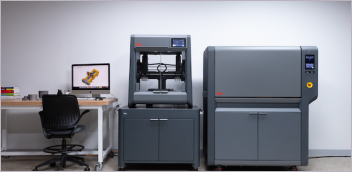
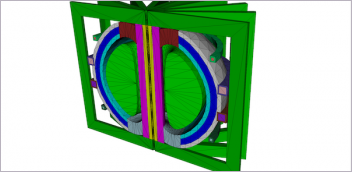
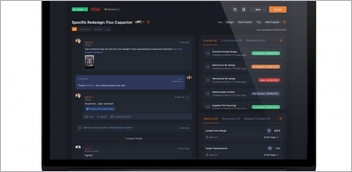
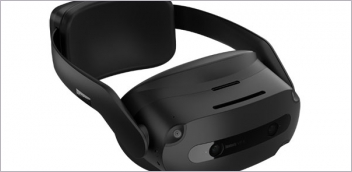