Latest News
March 1, 2006
By John Purnell
CFD solves complex flow dynamics of ACV lift fans and propellers in a fraction of the time.
When a recent client turned to CDI Marine of Portsmouth, VA, and asked them to develop the thrust and lift systems of a new Air Cushion Vehicle (ACV) hovercraft, the full-service marine engineering, design, and drafting company knew it had its work cut out for it. The new ACV would be about 40 percent longer and carry twice the payload of the existing craft (about equal to its own weight), and have to cruise at the same high speeds. It also had to maintain existing height and width maximums. CDI turned the development of the high-performance prototype designs over to its Marine Systems Development Division (CDIM-SDD).
The existing craft is a high-speed, fully amphibious large craft similar to vehicles currently being used by the British Navy, the Canadian Coast Guard, and the U.S. Navy. They have been used in rescue operations, as ice breakers, and for carrying troops and cargo from ship to shore.
The project meant designing new propellers capable of withstanding the additional forces of new turbines producing about twice the power of the existing engines, and new lift fans capable of developing additional pressure and flow to lift a heavier vehicle loaded with more payload. A technology roadmap analysis concluded that considerable advances in lift fan and propulsion technologies would be necessary to achieve the lift and thrust required for the new ACV.
Challenging Design ProblemCDIM-SDD was selected to design the lift fans and propellers because of the company’s long experience—operating as Band, Lavis & Associates—in the ACV design field. CDIM-SDD specializes in naval architecture and would have to solve the complex flow geometries in this challenging design problem. There are cabin structures forward, water-blocking wave fences outboard, and additional deck cargo that obstruct air flow to the twin aft-mounted propellers. The propellers are enclosed in a large aerodynamic shroud that contributes significant thrust because of the airflow around and through it. As a result, the shroud and propeller must be designed as a unit.
The four lift fans provide the cushion of high-pressure air that the ACV rides upon. These lift fans are mounted in double discharge volutes. The main discharge is for the lift-cushion system below the craft while the other directs air to a rotatable bow thruster system that helps craft steering. As with the thruster system, the volute design is affected by the fan design, so each must be developed in conjunction with the other.
We were given a maximum rpm for the components and told they would be turned by approximately twice the existing craft power. We were also required to maintain the existing craft ’s propeller shroud maximum diameter. The complexity of the geometry of each system meant an infinite number of potential designs and no intuitive way to determine the best. Building and testing a single blade design in a conventional manner can take months, which meant it could have potentially taken years to find a design that would meet all this project’s requirements.
We used blade design software to generate concept designs, and we used ANSYS CFX computational fluid dynamics (CFD) software from ANSYS Inc., to simulate the performance of these designs. We already had experience with CFD for designing turbomachinery, but this was the first time we had used ANSYS CFX. With its 3D capabilities and coupled multigrid solver that solves the full system of hydrodynamic equations simultaneously, CFX was the recommended choice.
You cannot learn to operate the full scope of a program like ANSYS CFX overnight, but beginning with the 3-day training course we attended, it didn’t take us long to feel comfortable operating the program and interpreting results. With the CFX program, one can pretty much do any kind of fluid flow analysis. Pressures and forces on different components in the flow field can be determined. Streamlines can be traced to show flow over objects or to show the upstream and downstream paths of the flow that passes through a propeller. Areas of flow separation can be identified. The torque requirements of rotating blades can be determined and component efficiencies computed. Basically, if you can setup the appropriate geometry of the problem, then you can perform the CFX analysis.
Our setup uses a cluster of four 2.6- to 2.8-GHz computers to run problems. This improves running time and allows larger problems with more detail to be tackled with ANSYS CFX automatically partitioning the problem to run on the multiple computers.
We used ANSYS CFX for predictions of horsepower, thrust, and inlet velocity profiles for the propeller and predictions of horsepower, flow rate, and pressure for the lift fans. CFX results from each design were iteratively fed back into the blade design software to further revise each design. Using this process we generated scores of potential designs while iterating toward an optimal solution. This was orders-of-magnitude faster than would have been required to design, build, and test just one design alternative using conventional methods. Finally, we simulated the wind tunnel used to test the propeller blades with ANSYS CFX, making it possible to correlate, with a high level of accuracy, the predicted and measured results.
We began by modeling the lift fan blades on the existing ACV in ANSYS CFX to validate our approach. The lift fan system was designed first because we had to determine the total lift fan power requirements. The propulsion power on the craft would use remaining available power from the engines.
CFX-TurboGrid was used for meshing the fan blades. We started by importing multiple radial blade sections between hub and tip into CFX-TurboGrid to generate a hexahedral mesh for the entire blade geometry. The volute used to distribute the fan airflow directs different airflow rates to the lift cushion and the bow thruster via a nonsymmetrical design. As a result, it is difficult to analyze and design without the benefits of CFX. And because the designs of the volute and fan blades are dependent on one another, the capabilities of ANSYS CFX were invaluable. The entire fan system would be modeled and analyzed from inlet through separate volute exits.
The propeller system design was undertaken following the lift fan system. The existing propeller blades were modeled and run in ANSYS CFX to validate our approach to the design. The ACV geometry—including propeller shroud, deck cabin, and the propeller shaft—were meshed. Deck cargo was easily added and meshed so that the program could be run both with and without the impact of cargo on the deck. The propeller shroud has a maximum diameter that is about 15 percent greater than the propeller diameter.
We found that air accelerating into the propeller around the forward face of the shroud creates a large region of lower pressure than exists on the back face of the shroud. That difference in pressure generates about a third of the total propeller system’s forward thrust. Directly downstream of the propeller within the shroud is a stator blade row that takes the swirl out of the propeller airflow. This recovers dynamic pressure, which generates additional thrust and improves overall propulsive efficiency. The propeller and stator must be designed as a system with accurate inlet conditions. Two interfacing cutout solids were left inside the propeller shroud for importation of the grids for the propeller and the stator blades. This approach made it possible to generate new propeller design iterations simply by importing the grids for the propeller blades, since the stator geometry did not have to be changed as frequently.
We used ANSYS’s CFX-TurboGrid software to generate the blade mesh for both the propeller and stator blade rows. We also used CFX-TurboGrid to set the tip gap between the shroud and the propeller blade tip, and also to simulate different angles of attack or loadings for the propeller blade by rotating the propeller blade about its center axis.
Since the baseline analysis showed very good agreement with physical tests of the existing ACV, we went to work immediately to create the new design. We used ANSYS CFX to simulate flow fields and calculate torque requirements for the proposed blades. We calculated horsepower by multiplying the torques (obtained with ANSYS CFX) with component rpm.
We took the inlet airflow velocity profile from the baseline CFX studies and input it into a blade generation program—TURBOdesign-1 from Advanced Design Technology—which allowed us to control many other design parameters. TURBOdesign then generated new blade section profiles that were imported into CFX-TurboGrid, which in turn generated the blade meshes for analysis with ANSYS CFX. The CFX results of the analysis included, along with power and system performance values, an updated inlet velocity profile that we would use to generate revised blade designs.
The fan blades were developed and meshed in CFX-TurboGrid in the same manner as were the propeller blades, except that the fan was a centrifugal type of fan, so that the airflow through the fan is turned 90° between its inlet and fan blade exit region that discharges into the double exit volute. CFX-TurboGrid could handle either flow case. The fan system that was modeled for CFX included an external area that fed a stationary inlet bellmouth, the rotating fan with blades, and the double exit volute with its two separate and different discharges. The design specifications called for similar volute exit static pressures but very different flow rates at the exits. Fan blade and double exit volute designs were changed iteratively with each ANSYS CFX run to converge on a suitable overall design that actually required less power than original estimates.
Each individual propeller and stator blade sees different loadings at any given time, since the air inflow to the propeller system is radially and circumferentially nonsymmetrical, as determined by CFX. The shroud, shaft, and hub components of the propeller, plus each stator blade and propeller blade, were all set up as separate surfaces in the CFX programming so loading could be easily determined and identified separately. By adding the forces in the thrust direction for these surfaces together, we could easily determine the total thrust generated by the propeller system.
CFX outputs the torque component about the shaft of each propeller blade. The sum of these outputs gives the total propeller shaft torque and hence the total input shaft horsepower. We proceeded through an iterative process that enabled us to continuously improve the blade and system design until the available powering requirements were met with maximum thrust. Through this process, we approximately doubled the power capacity of the new propeller system at normal operating conditions by designing a six-bladed propeller, compared to the existing four-bladed system, but the diameter of the propeller remained the same.
Within the space of a few weeks, we modeled scores of different blade designs; a fraction of the time that would have been required using a conventional approach. We also set up an ANSYS CFX model simulation of a one-sixth scale model with the new propeller in a wind tunnel, and used this to predict the results of subsequent wind tunnel tests of the new propeller blade design. The wind tunnel was meshed separately from the cabin, propeller shroud, and blades and the meshes were then assembled in CFX-Pre, the CFX physics preprocessor. With this approach, the craft components with the propeller system could be rotated in CFX to simulate different relative wind directions across the craft, which was to be part of the wind tunnel test. After ANSYS CFX solved the model, the postprocessor was also used to plot streamlines showing the flow direction around the model. CFX results traced the path of flow particles around the propeller region back to their source location at the inlet to the wind tunnel.
CFX is an invaluable tool for analyzing system designs. A key advantage is that all of the components can be analyzed together in order to view their effects and evaluate total system performance. Even simple geometries can become very complex to evaluate when they are tied together. Evaluation of complex components, such as the double discharge volute design used with the lift fan or the entire craft with the propeller system, would be nearly impossible without the aid of tools like CFX. Using an iterative approach between our various design tools and methods and the CFX results, we were able to refine the component designs to develop a lift fan and propeller system that efficiently met the ACV requirements in a reasonably short amount of time with minimum testing requirements.
John Purnell is a senior engineer with CDI Marine Systems Development Division in Severna Park, MD. You can send him an e-mail about this article by clicking here. Please reference “Hovercraft, EoA March 2006” in your message.
Product Information
TURBOdesign-1
Advanced Design Technology Ltd.
London, UK
ANSYS CFX, CFX-TurboGrid
ANSYS, Inc.
Canonsburg, PA
CDI Marine
Portsmouth, VA
Subscribe to our FREE magazine,
FREE email newsletters or both!Latest News
About the Author

DE’s editors contribute news and new product announcements to Digital Engineering.
Press releases may be sent to them via [email protected].
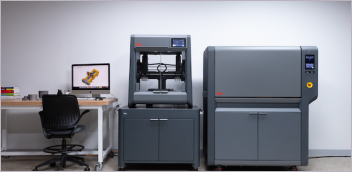
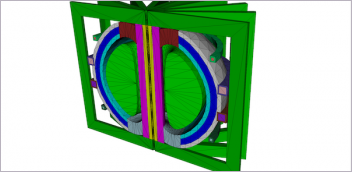
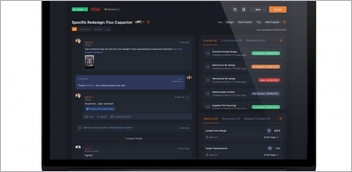
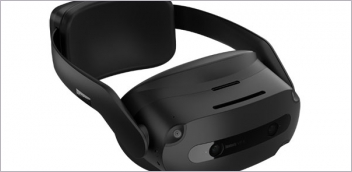