SIMULIA Asks: Is SLM for You?
Consider managing realistic simulation as a valuable corporate asset to trim time to market, cut waste, improve quality, and innovate.
Latest News
April 1, 2008
By Paul Lalor
![]() As demonstrated by virtual crash testing, realistic simulation allows engineers to evaluate multipledesign alternatives more efficiently than is possible with traditional physical testing. |
Providing a computer-aided environment where 3D models can precisely represent the physical behavior of objects under realistic operating conditions enables developers of design simulation technology to deliver improved technology and user experiences that reduce or even eliminate some physical tests.
Armed with the knowledge of what will happen in the physical world before it actually happens, product development teams have been able to optimize designs, eliminate errors before committing to physical prototypes, and anticipate production problems before the first tool has been cut.
A 2007 survey by the research firm CPDA (cpd-associates.com) found that 58 percent of engineers have growing confidence in simulation results and 21 percent have complete confidence. As confidence in simulation results has grown, product development teams have been using realistic simulation earlier and more frequently in the design cycle. However, the technology is typically still used outside of most product lifecycle management (PLM) systems or processes. The tools and data are controlled by small groups of experts or individuals and, more often than not, the simulation results are stored on local computers. That means the way the simulation was built and performed is known only by the expert who created the model.
![]() SIMULIA SLM leverages technology from Dassault Systemes’ 3D Live and EnoviaPLM solutions to enable product development teams to accesssimulation results and collaborate on product design decisions. |
Research Shows Innovation Results
For simulation to be truly effective as an integral part of the product development cycle, the processes, authoring tools, data, and resulting intellectual property (IP) associated with simulation must be shared, managed, and secured as strategic business assets. A new solution category, simulation lifecycle management (SLM), is emerging to address these issues.
The vision for SLM is to bring order to simulation processes and provide the technology to ensure simulation data integrity, traceability, knowledge capture, and collaboration. The end goal is to assist organizations in leveraging their simulation assets more effectively and bring a new level of efficiency in shortening development cycles, reducing waste, and improving product quality, while fostering a culture of collaboration and innovation.
“Simulation lifecycle management will allow for many previously excluded downstream elements of projects to be engaged with the upstream elements as early as the concept-creation stage,” says Tom Lange, director of corporate research and development modeling and simulation for Procter & Gamble. “The early integration of experts, designers, and managers, with requirements is the key. It will improve the productivity of the entire technical community to innovate — innovating how we innovate.”
![]() Companies such as PelamisWave Power are leveraging realistic simulation to develop new and innovative alternative energy solutions. Capturing andmanaging simulation-generated intellectual property is a natural step to take to gain the maximum benefit from an organization’s simulation expertise. |
SLM is defined as the ability to manage simulation-generated intellectual property related to product or process development. To be effective an SLM system must encompass four essential functional areas: simulation data management, integration and process automation, decision support, and collaboration.
Engineering organizations that wish to incorporate SLM with their processes face several tasks: integrating various design and simulation solutions; striving toward standardized simulation and validation methodologies; incorporating these tools and processes into a data management environment; and determining how to share simulation results to support decision making throughout the organization.
![]() |
Integrating simulation solutions
Because of advances in simulation technology, product development companies are migrating to best-in-class solutions. In addition, many of these companies have created in-house technology applications that extend their ability to innovate and gain a competitive advantage. These multiple technologies require SLM systems to be designed with openness and configurability as key design principles.
Openness permits a wide variety of simulation applications from different engineering domains, such as durability, noise and vibration, crash worthiness, fluid dynamics, and others to be connected to — and executed from — the SLM system. Configurability enables this openness to occur quickly and easily without the need for deep, costly customization of the SLM environment.
Unplanned simulations that add great value to the development of a product are fairly common occurrences. The data associated with these types of simulations should be associated with the product design and maintained within the SLM system. However, without capturing well-defined simulation processes, product developers cannot achieve efficiency and consistency across programs or from one stage of product development to the next or even from one engineer to another.
![]() When selecting an SLM solution, it is importantto know how much of the capabilities areprovided as out-of-the-box, configurable, orcustomizable. |
Providing Insight
According to Frank Popielas, manager of advanced engineering at Dana Sealing Products Division, “Accurate and consistent simulation has to be at the heart of any design and manufacturing development process. In order for simulation to provide more than a partial picture, we need system simulation capabilities as well as the ability to carry over simulation results from one stage to the next. A good example of this is the influence that manufacturing processes have on the functional behavior of the final product.”
SLM can be used to capture best simulation practices developed by the experts in your company and promote their consistent use to a wider group of users. This helps ensure that the simulation deliverables arrive more efficiently in a validated and traceable manner.
SLM also allows your simulation team to monitor and improve these simulation methodologies over time, which increases confidence in the design decisions based on simulation results. Lastly, when done well, approved simulation methodologies can be deployed to nontraditional users in your organization, allowing them to benefit from the insights provided by simulation.
![]() Multiple engineering domains influenceproduct performance and design decisions.By managing the simulation tools, data, andprocesses organizations are able to securetheir simulation-generated intellectualproperty and gain significant efficiencies. |
Incorporating simulation with data management environments
The traditional absence of a data management framework for simulation has limited engineers’ ability to share information and collaborate effectively on design decisions in a timely and consistent fashion. The previously mentioned CPDA survey also reported that only 6.1 percent of companies are using some form of a simulation data management solution, which is typically designed to handle large, complex, and highly specialized simulation data files.
Thirty-five percent use legacy databases or data management applications. The largest percentage of respondents, 42.7 percent, keeps their simulation data on local or departmental drives. This makes it difficult or even impossible for other decision-making stakeholders to access the data or even be aware that it exists. This makes it extremely important to leverage a data management system that can be configured to handle large and complex data sets, be configured to manage unique processes, and make the simulation results available to a wider audience of constituents, including non-engineers.
Most engineers and designers would agree that repeated simulation throughout the design process yields higher quality products that hit the market sooner than those designed and validated using only conventional prototyping and physical testing. Often ignored, but perhaps more significantly, simulation results have an impact beyond the immediate scope of product design and production.
Major Aspects of SLM Simulation Data Management: Collects and manages the data and processes associated with simulations within the overall design process. It establishes the relationships between requirements, design data, and simulation data, provides full traceability to simulation data and processes and enables data reuse. Integration and Process Automation: Integrates a broad spectrum of simulation applications into the SLM environment. Captures overall, best in class, business processes, and embedded simulation methodologies within automated workflows in order to deploy these methods to a wider group of users. Decision Support: Provides intelligent and intuitive access to the information and knowledge generated by simulations to individuals or groups who need the data to support design and business decisions throughout the development process. —P.L. |
SLM Yields Solutions
The research firm CIMdata predicts that the role of simulation will expand beyond specific validation phases and permeate every element of product development. According to CIMdata’s December 2006 white paper titled “Enterprise Simulation Management:”
“Simulation capabilities will eventually become available much more broadly throughout a company, from purchasing to sales, to many others as they are enabled to utilize them to make more informed and confident decisions. The business will benefit and be able to respond faster to customer requests while also improving design variation predictability, leading to more accurate quotations and higher profitability.”
The corporate ability to create virtual products that mirror their behavior in the physical world is well within reach. Those companies performing realistic simulation on a regular basis find themselves at a crossroads. They can either continue to let simulation processes and results be disconnected from their product lifecycle management solutions, or they can explore the emerging SLM solutions to begin the process of securing their investments in simulation technology and expertise.
Thus, SLM solutions promise to improve the effective deployment of simulation technology and practices throughout the product and process development activities and, in doing so, organizations embracing this new paradigm will be able to fully leverage their simulation expertise as the valuable corporate asset that it has become.
More Info:
SIMULIA
Providence,RI
simulia.com
Paul Lalor is product manager for the SIMULIA brand of Dassault Systemes. To comment on this article, send e-mail to [email protected].
Subscribe to our FREE magazine,
FREE email newsletters or both!Latest News
About the Author

DE’s editors contribute news and new product announcements to Digital Engineering.
Press releases may be sent to them via [email protected].
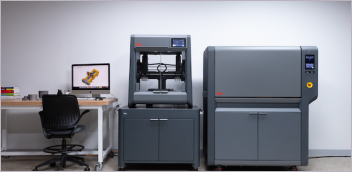
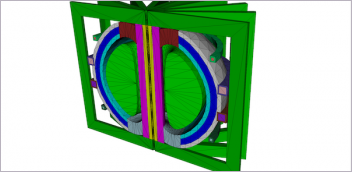
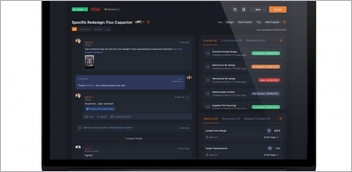
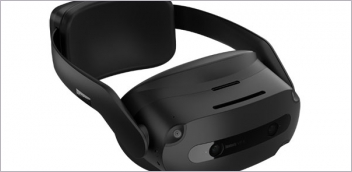