Solar Car Team Races to Finish with CATIA and ENOVIA
Blue Sky Solar Racing places first among Canadian teams with Dassault Systèmes PLM solutions as well as ANSYS CFX and MATLAB.
Latest News
October 1, 2008
By Jeff Griffith
![]() This is the front view of the solid model of Cerulean, the University of Toronto’s Blue Sky SolarRacing team’s fifth-generation car designed for the 2007 Panasonic World Solar Challenge. |
Every two years, a special field of cars competes in the Panasonic World Solar Challenge, crossing the Australian continent powered by nothing but the sun. Teams research, build, and design vehicles capable of completing the 3,000-kilometer journey from the tropical town of Darwin in the Northern Territory to cosmopolitan Adelaide in South Australia.
The Universityof Toronto’s Blue Sky Solar Racing team’s fifth-generation car, Cerulean, was the team’s entry for the 2007 challenge. The team, which consists of undergraduate and graduate students and alumni volunteers, leveraged Dassault Systèmes’ product lifecycle management (PLM) solutions, including CATIA and ENOVIA Digital Mock-up (DMU), in its designs.
Training on the Dassault Systèmes software was donated by Aventec Inc., a CATIA solutions provider based in Markham, Ontario. Dassault Systèmes is a sponsor of the Blue Sky Solar Racing team, whose members are committed to demonstrating the viability of renewable energy technology and the practical benefits of a multidisciplinary approach to solving problems.
Evaluating 60 Designs in a Few Hours
The critical challenge in developing a competitive solar vehicle is reducing drag and weight while increasing power, and ultimately optimizing the solar car. The solar panels are arrayed across the top of the body to maximize sunlight collection. They must be oriented directly toward the sun to increase the power they generate, but this often increases drag, compromising efficiency. Many design variables must be considered to improve this trade-off, including the baseline shape, track width, wheelbase, driver positioning, and others to optimize the car’s power-to-drag ratio.
![]() The isometric view of Cerulean hints at its aerodynamic shape andsolar-collecting capability. |
Amy Bilton, chief aerodynamicist for the 2007 car, needed to analyze many different alternatives to improve the efficiency of the design. She estimated that it would have taken about two hours to create each design iteration by manually modifying the CAD geometry. Instead, she developed a CATIA design table that incorporated each of the key design variables. Then she simply typed in the values of each variable for the iterations she wished to explore. CATIA automatically generated the resulting models.
Using C++, Bilton created a routine that read the design parameters from the spreadsheet. It calculated the area available for solar arrays on the top of the vehicle and the resulting power. With MATLAB scripts from The Mathworks, she was able to quickly create many design configurations that were imported into CATIA V5 for model creation.
![]() A lofted mesh of Cerulean’s main body imported from a design table using Dassault Systemes’ CATIA V5. |
Bilton also used ANSYS CFX for all the CFD performed, including drag calculations on several distinct CATIA solid model configurations for the car’s main body. After completing each design iteration, she modified the model and moved steadily toward her goal of optimizing the power-to-drag ratio. She generated 60 design iterations in about five hours, approximately a 96 percent time savings compared to conventional methods.
Blue Sky decreased drag by 22 percent overall and increased the power of the solar array by four percent. The team was well on its way toward creating one of the top cars in its class.
Wire Harness Design Cuts Weight 3 Percent
Solar vehicles have a large number of power and signal wires. Wiring harness design is critical because the holes that must be cut for the wires have a significant impact on the weight and structural integrity of the aerodynamic shell and chassis. The signal wires are also highly sensitive to impedance, so their lengths must be closely controlled.
On the 2005 car, the electrical wiring was done at the very end of the design process. This meant that the mechanical engineers did not know where the wiring holes would be, so they had to over-design the shell and chassis. They also had to make last-minute design changes to overcome impedance problems.
On the 2007 car, the team used CATIA electrical applications, including Electrical Library 2, to create and place electrical components, Electrical Harness Installation 2 to bundle harnesses, and Electrical Wire Routing 2 to route the wires through the created bundles. The CATIA electrical applications made it possible to design the wire harnesses at the same time as the mechanical structures.
![]() Tom Rodinger and Josh Switnicki inspect Cerulean’s battery monitoringsystem in the pits during qualifying rounds in Darwin, Australia. |
“Thanks to CATIA, the mechanical engineering team knew in advance what size and where holes would be needed to accommodate the wiring harness,” says Dmitri Stepanov, who is chief engineer for both the 2007 and 2009 cars. “This made it possible to optimize the design of the shell and chassis to make them lighter.”
Each time the Blue Sky engineers repositioned components, CATIA automatically calculated the amount of wire required by the new configuration. This made it possible to choose a configuration that substantially reduced the amount of wire. The software also calculated the length of each wire so the engineers could easily predict its impedance and reposition components where necessary. The reductions in the weight of the shell, chassis, and wire provided a three percent reduction in total mass compared to previous cars. In highly competitive solar racing, a three percent reduction in mass is a significant difference.
![]() Dmitri Stepanov is strapped into Cerulean as Blue Sky prepares to leavethe Dunmara check point during the 2007 PanasonicWorld Solar race. |
“CATIA Design Tables provided a competitive advantage by enabling us to evaluate a large number of design iterations in the limited time on hand,” says Andreas Marouchos, managing director of the 2007 car. “CATIA wiring harness design tools helped us reduce the weight of the vehicle. CATIA Composite Design helped reduce the weight and improve the margin of safety of our composite parts. These improvements helped us finish the World Solar Challenge in fifth place in our class and first among six Canadian competitors.”
Building on Success
In the 2009 car currently under development, Blue Sky Solar Racing plans to increase its use of the CATIA ergonomic workbenches to improve driver performance and safety. “The 2007 car was a two-seater, but the 2009 car will be a one-seat design that will be more challenging from an ergonomic standpoint,” Marouchos said. “The ergonomics capabilities built into CATIA make it easy to define a driver and manipulate him or her during the design process to optimize vision, crush zones, and egress in the event of an accident. The measurements of the driver can easily be changed to determine how different people would interact with a particular design.”
The team’s experiments with CATIA on the 2007 car were so successful that “our plan is to model all of the mechanical and structural components of the 2009 car in CATIA,” Stepanov said. “We already used this approach on the axle hub of the 2007 car using the ENOVIA Digital Mock-up functionality in CATIA, and it allowed us to reduce weight and the number of parts.” DMU allows users to see parts in an assembly to better understand their relationships and identify potential improvements.
“By viewing a 3D master model, we will be able to achieve similar savings throughout the entire vehicle,” Stepanov said. To build a master model of the entire car will require significant product data management capabilities, however, so the Blue Sky team is adding ENOVIA SmarTeam to its design arsenal for the 2009 car, donated by Aventec.
“Aventec has been very supportive,” Marouchos said. “They exposed us to the features and capabilities of CATIA and helped us take full advantage of its power. For example, they showed us CATIA’s composite design features, which helped us reduce the weight and improve the margin of safety of our composite parts. Aventec also helped us install the software and showed us how the technology could be applied to our unique problems.”
So far, for the 2009 design cycle, more than 100 body configurations have been run. Each CFD simulation uses approximately 8 million elements including detailed boundary layer resolution to study the effect of flow separation on the car’s surface. The MATLAB script automatically generates the configuration, and a C++ script loads the file into CATIA, which generates the model and automatically outputs the STP file to CFX for meshing and analysis. A constant stream of design configurations enables the team to run simulations back to back in order to maximize the use of computer time.
![]() The University of Toronto’s Blue Sky Solar Racing team at the finish lineof the 2007 Panasonic World Solar Challenge in Adelaide, Australia. |
Designing the Best
ENOVIA SmarTeam controls the CAD and related product data files, preserving all the native CATIA links and references in a secure electronic vault to eliminate the risk of unauthorized modification or accidental deletion. It also manages and stores all versions and variations studied by the designers and enables multiple designers to simultaneously work on the same parts or related parts with full knowledge of what their teammates are doing, updating modifications “on the fly” to avoid any inadvertent loss of edits. SmarTeam also enables the hierarchical creation of a product structure of the entire car as a single digital model, which will help identify and exploit additional opportunities for design improvement.
“The master model will help coordinate the work of our team of designers, who are by necessity working in different places at different times,” Stepanov says.
“We are expecting to see substantial time savings by eliminating time spent searching for the right version of a design file and time spent correcting errors, such as when someone makes a change to the wrong version of a file. We only have the time and money to build one vehicle, and CATIA and ENOVIA SmarTeam, along with our analysis tools, are ensuring that this one vehicle is the best we can possibly build,” adds Stepanov.
More Info:
ANSYS
Canonsburg,PA
ansys.com
Aventec
Markham, ONT
aventec.com
Blue Sky Solar Racing
Universityof Toronto
Toronto, ONT
utoronto.ca
Dassault Systèmes
Paris, France
3ds.com
The Mathworks
Natick, MA
mathworks.com
Jeff Griffith has been active in the PLM industry for 20 years and has a degree in mechanical engineering. He is a founder and president of Aventec, a PLM software and service provider. Send comments about this article to [email protected].
Subscribe to our FREE magazine,
FREE email newsletters or both!Latest News
About the Author

DE’s editors contribute news and new product announcements to Digital Engineering.
Press releases may be sent to them via [email protected].
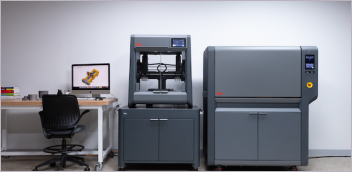
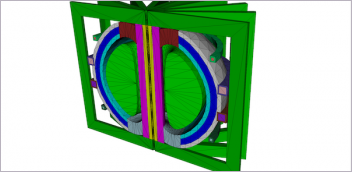
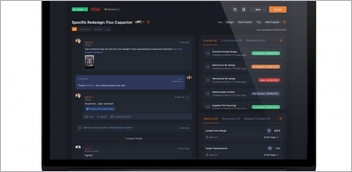
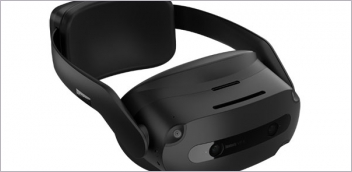