Taking the Heat Out Of Electronics
Contributing Editor Louise Elliott speaks with Sherman Ikemoto ofFlomerics on what Flotherm brings to electronics design. A coupleof users provide further insights.
Latest News
July 1, 2006
By Louise Elliott
Like most of the general-purpose CFD (computational fluid dynamics) programs, Flomerics Group PLC and its Marlborough, MA-based US subsidiary, Flomerics Inc., was founded by academics. Unlike general-purpose CFD programs, Flomerics has always been focused solely on a single industry: electronics.
The idea behind development of Flotherm was to build in electronics intelligence on top of CFD. This intelligence would, in turn, be used to make problem setup, modeling, and analysis much faster, more efficient, and more accurate for engineers who design electronics, says Sherman Ikemoto, Business Development Manager for Flomerics Inc.
“Accuracy takes on new meaning in delivering analysis to non-analysts,” he says, describing the result as “analogous to taming the CFD solver by setting up the software to obtain convergence in a high percentage of analyses. Because of the electronics intelligence and industry knowledge contained in the software, users feel more secure about the accuracy of their results.”
The industry knowledge Ikemoto describes is very specific, and in many cases is embodied in the form of smart parts—predefined models incorporated into the software. The high degree of standardization in electronics makes the inclusion of such information possible.
|
Taking the Heat Out |
‹ ‹ AMI Semiconductor used Flomerics’ Flotherm thermal analysis software and Flopack Web-based thermal model generator to accurately predict the operating temperature of this 28-lead small outline integrated circuit package for an automotive application.
“The industry’s standards can be embedded in the program, in the cases of such products as IC (integrated circuit) packages,” Ikemoto says, pointing out how Flotherm’s developers put rules into the software for such outside-supplied components as flip-chip BGAs (ball grid arrays). “We know the thermal properties of these components, and the program contains that information, so that the designer can go ahead and create high-density circuits with good thermal properties. Flotherm can guide the designer in setting up thermally efficient ICs.”
Smart parts exist for ICs, fans, and heat sinks. They coexist with a materials database that contains thermal properties for many other components. The chassis for electronics products are available either as smart parts or can be found in the Flotherm library.
Ikemoto points out that electronics designers need to know the kind of packages used for outside components, and where they go on the PCB (printed circuit board) for the best thermal performance. “The designer knows the boards, ]and yet] may not know the thermal properties of all outside parts—but the software knows them, and takes care of such issues.”
New Materials
As devices grow ever smaller and more tightly packed with components, thermal interface materials are becoming more important to the design of electronics products.
“The problem of managing heat in electronics packages is a major issue,” says Ikemoto. “If the heat is too high, engineers look for heat sinks to remove it. Because Flomerics keeps up with new materials as they appear, we can help designers incorporate new materials that may make the actual package into a heat sink.”
He gives the example of ThermalWorks, a company based in Anaheim, CA, which makes a material called STABLCOR. “This ]material] can be used as a substrate in PCBs and IC packages to remove heat,” he says. “Such materials weren’t known in traditional electronics designs—but because they improve the removal of heat, they are now incorporated in the Flotherm library.”
|
Taking the Heat Out |
› › When Cambridge Broadband needed to verify the thermal design of its new broadband wireless access unit, engineers used Flotherm to validate and optimize the initial design.
Ikemoto says that companies usually cannot afford dedicated thermal engineers on their staffs, because they must focus on designing products within an ever-narrowing window of opportunity. “Because they know they can depend on Flotherm, it’s currently used in a ratio of three to one over other CFD programs in the electronics industry.”
Staff of Industry Experts
The success of the software is due in part to the fact that Flomerics doesn’t consider itself to be a CFD company solely, and in fact, CFD isn’t its only business. It offers electromagnetic analysis software, also meant for electronics designers.
Many of the company’s engineers are actually electronics cooling experts who know how to use the software. “They keep themselves up to date in the industry, and are better versed in that than in CFD,” Ikemoto says. “They consult with users, support them, and train companies to become temperature-aware throughout the design process.”
Ever-Tightening Design Cycles
Cisco Systems, San Jose, CA, is among the technology leaders in switches and routers for many different applications. Herman Chu is Technology leader for Cisco’s Router Service Provider Technology Group (RSPTG). Chu says that he works with companies that manufacture CPUs, and depends upon them for thermal information, because the chips must meet thermal requirements for the types of applications Cisco develops.
|
Taking the Heat Out |
‹ ‹ Ascom Energy Systems used Flotherm to solve a cooling problem in a new high-frequency telecom power supply. The new heat sink guides air from a closely sited fan through curved channels rather than over conventional fins or pins.
Chu has used Flotherm since 1993. Before that, he worked in aerospace and used several general-purpose CFD codes. “Flotherm specializes in electronic cooling, and reduces product development time,” he says. “When companies designed mainframe computers, they had five-year development cycles, ran analyses on Cray supercomputers, and also built many prototypes for testing. Then the industry development cycle went down to three years—and today, we deal with 12-month to 18- month cycles. We don’t have time for multiple prototypes.”
He says that such tools as Flotherm hasten the cycle, because designers can build models that connect to MCAD and other programs quickly. “Today’s first pass consists of numerical simulation. Inexpensive computing resources mean that we can do advanced analysis up front, so that we’re close to the final product before building a prototype.”
Chu also likes FLO/PCB from Flomerics, a separate software tool that makes it possible to design 3D layouts together with a great deal of data. “It’s common for conceptual drawings of PCBs to be created as 2D layouts with Microsoft Visio. However, the design doesn’t have information about component height and power, and we need that information for running analyses. Waiting for the data wastes time, and then we have to redigitize the layout before we can submit it Flotherm. With FLO/PCB, the designs can produce a conceptual 3D layout with all the height and power data included—and that also reduces design cycle time.”
|
Taking the Heat Out |
› › Ascom used Flotherm to optimize cooling in its new power range using a space-saving circular aluminum heat sink. It matched the shape of the fins with the swirl from the fan.
He notes that over the past decade, PCBs have grown in complexity from single cards to multiple—and that sometimes this results in having the contents of three boards all in one. “They use double the power compared to older boards, and they need to be analyzed quickly and accurately. Although general-purpose CFD is more flexible, in terms of the kinds of physics undertaken, it requires expertise to use properly. Flotherm has more built-in libraries specific to electronics design than any other CFD program, as well as more models specific to electronics cooling, and it can pull in designs from eCAD programs.”
Future Electronics Cooling
The next big challenge for CFD in electronics will be thermal analysis at the silicon-die level, says Ikemoto. With only a few exceptions, this kind of analysis isn’t performed currently.
|
Taking the Heat Out |
‹ ‹ Flotherm analysis resulted in changes to Cambridge Broadband’s design for improved convection cooling and gave it the confidence to press ahead with product tooling.
“Virtually all electronics designers today assume constant die level temperature. But at the smaller manufacturing levels that occur now—65 nanometers or below—CPU makers can have between 25 million and 50 million transistors along with their interconnects on something the size of a person’s thumb. At those scales, temperature is a first-order effect on circuit performance—so starting this year, we have to make silicon design process engineers temperature-aware if we want newer circuits to work.”
Editor’s Note: On June 26, Contributing Editor Louise Elliott passed away after a sudden illness. After more than 200 articles and news stories for DE over the years, this is Ms. Elliott’s final article for you. Send your comments about this article through e-mail by clicking here. Please reference “Electronics Design, August 2006” in your message.
Company Information
FLOTHERM, FLO/PCB
Flomerics, Inc.
Marlborough, MA
STABLCOR
ThermalWorks
Anaheim, CA
Cisco Systems, Inc.
San Jose, CA
Visio
Microsoft Corp.
Redmond, WA
Subscribe to our FREE magazine,
FREE email newsletters or both!Latest News
About the Author

DE’s editors contribute news and new product announcements to Digital Engineering.
Press releases may be sent to them via [email protected].
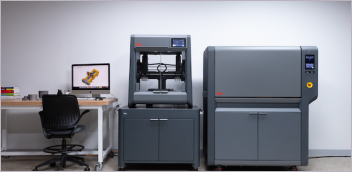
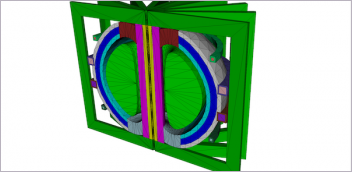
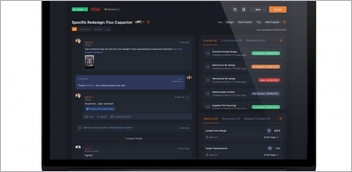
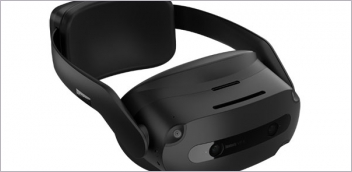