Time for RP Standards
Lots of talk, some intriguing action, and feedback from the trenches of RP setthe stage for developing standards.
Latest News
March 1, 2005
By Pamela J. Waterman
The lack of standards for rapid prototyping (RP) is a perennial barrierto launching it on the fast track to wide acceptance. A time and moneysaver when compared to traditional subtractive machining, RP can alsoproduce parts otherwise not physically buildable, but there are stillno official methods for evaluating its benefits and limitations. WhileRP equipment and materials suppliers provide their own specifications,users are seeking objective information.
Every year at the Society of Manufacturing Engineers (SME) RapidPrototyping and Manufacturing Conference, roundtable forumsinevitably turn to the need for national or international standards.Despite the apparent demise of several government-led projects, thereare pockets of activity addressing this subject around the world. DEcaught up with some of the activists involved to get a status report.
Stepping Up to the Plate
Wondering if a given material will behave consistently from batch tobatch? Can you predict how behavioral properties may or may not varybetween traditional and RP parts? Where can you go for answers?
The SME, continuing its efforts to meet the needs of professionals,companies, and industry, recently launched the Rapid Technologies andAdditive Manufacturing Community (RTAM) to address such questions. Itevolved from the Rapid Prototyping Association of SME (RPA/SME), agroup that had been active since 1993. Within the RTAM, the Materialsand Process Standards committee is working to research and collect justthis kind of data, and eventually determine a path that could bring theresults together as universally accepted standards.
Image of cowling Courtesy of Stratasys, Inc.
Carl Dekker, last year’s Chairman of the RTAM Steering Committee andPresident of Met-L-Flo, an RP service bureau located in Geneva,Illinois, notes that one drawback to developing standards is that mostpeople don’t want to fund something if the end result only applies toprototyping, rather than large-scale manufacturing. “The groupacknowledges that material and process standards are critical toevolving rapid prototyping into true 3D digital manufacturing,” headds, “but what’s needed are definitions.“In the mid-1990s, both the NationalInstitute of Standards andTechnology (NIST) and ASTM International (originally known as theAmerican Society for Testing and Materials), supported independent workin this area. The former generated a flurry of articles andpresentations by its Manufacturing Systems Integration Division, butthat work does not appear to have stimulated action toward eitherformal standardspossibly defined by the American National StandardsInstituteor de facto standards, such as an improved or replaced STLfile format. And while ASTM’s website still lists an RP subcommittee aspart of its mechanical testing group, activity on the subcommitteeended sometime prior to 1998. So, the search continues.

Z Corp’s Spectrum Z510 System prints prototypes like this running shoe sole inhigh-definition color to reflect original design data and to make sure modelsaccurately communicate thedesign intent.
Academic Research Digs Deep
Of the several dozen universities spread around the world that areheavily involved in a range of RP material and process research, manyhave projects that tackle bits of the standards puzzle.
For more information on university efforts in both basic and appliedresearch, as well as contact names for follow-up, see Wohlers Report2004, an annual study on rapid prototyping, tooling and manufacturingworldwide, published by Wohlers Associates.
Industry Efforts Often Linked to DoD
The not-for-profit National Center for Manufacturing Sciences (NCMS) inAnn Arbor, Michigan, offers a related but different approach supportedby industry and government funding. NCMS, the largest cross-industrycollaborative research and development consortium in North America,supports an Advanced Digital Fabrication and Repair group that includessuch companies as Honeywell and Pratt and Whitney. They areconducting experiments to determine the most viable approach to usingRP to produce functional parts, including cast metal parts, eitherdirectly or indirectly.
According to NCMS Program Manager Connie Philips, over the past 10years the group’s members have worked with every major supplier of RPequipment in existence, with the ultimate purpose of introducing thetechnology into Department of Defense (DoD) maintenance depots. Assuch, members work on pilot projects and test samples, but so farthey’ve focused on characterizing RP processes and materials forspecific DoD applications.
Philips notes that users are starting to put pressure on RP equipmentvendors to certify materials for content. She points to the steelindustry as an example. “They can’t guarantee how a part is made,” saysPhilips, “but they can certify the raw materials they produce. Ourgroup is now pulling the RP suppliers along to do just that.”
The Boeing Company is one of the first manufacturers to succeed incertifying a material that meets military requirements. On-DemandManufacturing, a Boeing subsidiary that’s based in Camarillo,California, has succeeded in using 3D System’s Selective LaserSintering equipment to create approved nylon air-duct layouts. A bigadvantage, beyond weight savings, is the fact that the new partsreplace multipiece metal assemblies.
Looking Ahead
During a roundtable session during 2002’s SME RPandM Conference,users explored obstacles to RP product development, and cited lack ofpublished data as one of the main issues. However, it appearsthat even hard data may be kept private for competitive purposes, andsometimes hard-earned data is out of date when published, as newmaterials are continually developed. It may be worth investing directlyin one of the consortium efforts at a particular university orassociation, to tap into their collective knowledge in a timely fashion.
“The most likely scenario is that de facto standards will appear when acompany develops the IBM PC of the RP industry,” says industryconsultant Terry Wohlers. “Until then, we will have little choice butto live with the unwieldy smorgasbord of machines, materials, and dataformats offered by dozens of companies worldwide.”
NCMS consortium members agree, stating that it’s really a materialissue, and that once you find a high-volume application that you canfill with an existing material, suppliers will justify characterizingthat material for quality and design purposes. They think the bestexample of this so far is the Invisalign teeth-straightening systemfrom Align Technology. In this process, patients wear a series of clearplastic aligners fabricated from customized SL molds. Even though theprocess uses RP indirectly, it’s becoming a huge business.
In the meantime, never underestimate the power of the grassrootsmovement. Every once in a while this topic arises on the RapidPrototyping Mailing List (http://rapid.lpt.fi/archives/) with a threadworth following, and members are quite willing to share theirreal-world experiences.
An RP Parts Library?
Many of the aspects of an RP standards solution were proposed inarticles and reports following an NIST workshop in October 1997. One ofthose was to develop a standard library of 3D features (e.g., spheres,cylinders, prisms, cones) defined in a variety of sizes and orientationangles.1 Measured attributes could include flatness of surfaces,roundness of holes and cylinders, minimum thickness of walls and slots,and surface roughness, to help potential users compare and trade offaspects of using different processes and materials for a given part.
More recently, the talk has swung toward creating standards strictlyfor the raw materials. If you’d like to comment about this and otheraspects of potential RP standards, contact SME or Tim Gornet([email protected]).
PJW
1. “Rapid Prototyping’s Second Decade,” Kevin Jurrens, ed.; RapidPrototyping Association of the Society of Manufacturing Engineers, Vol.4, No. 1, First Quarter 1998.
Upcoming Events SME Rapid Prototyping and Manufacturing 2005 Conference and Exposition 6th National Conference on Rapid Design, Prototyping and Manufacturing 2nd International Conference on Advanced Research in Virtual and RapidPrototyping (VRAP) 2005, Leiria, Portugal, September 28-October 1 |
Contributing editor Pamela J. Waterman is an electrical engineer and afreelance technical writer based in Arizona. You can contact her aboutthis article via e-mail c/o [email protected].
Companies Mentioned in this Article:
Align Technology
Santa Clara, CA
ANSI
Washington, DCASTM International
West Conshohocken, PAGeorgia Institute of Technology
Athens, GALoughborough University
Loughborough, Leicestershire, UKUniversity of Louisville
Louisville, KYMet-L-Flo, Inc.Geneva, IL
Milwaukee School of Engineering Rapid Prototyping Center
Milwaukee, WINational Center for Manufacturing Sciences
Ann Arbor, MIOn-Demand Manufacturing
Camarillo, CARapid Prototyping Mailing List
Society of Manufacturing Engineers
Dearborn, MIUniversity of Texas at Austin
Austin, TXWohlers Associates
Ft. Collins, CO
Subscribe to our FREE magazine,
FREE email newsletters or both!Latest News
About the Author

Pamela Waterman worked as Digital Engineering’s contributing editor for two decades. Contact her via .(JavaScript must be enabled to view this email address).
Follow DE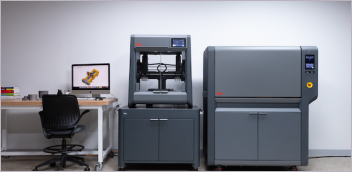
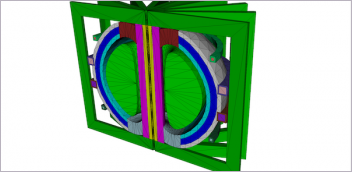
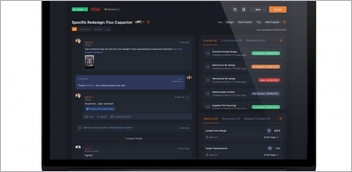
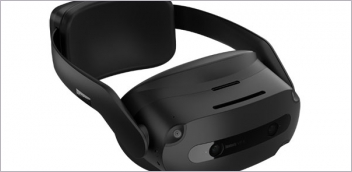