Advanced Design Uses Geomagic to Halve Prototype Time
New FORCE America design emerges from combination of clay, digital shape sampling, and rapid prototyping.
Latest News
July 27, 2009
By Bob Cramblitt
![]() This is an exploded view of the joystick design FORCE America was after. Images courtesy of Advanced Design Concepts |
FORCE America of Burnsville, MN, had a challenge familiar to many companies: To improve on a previous design, yet retain the familiar look and feel that customers love about that product. The answer came from Advanced Design Concepts of Pewaukee, WI. ADC combined clay modeling with digital shape sampling and processing (DSSP) using Geomagic Studio software and rapid prototyping with an Objet 3D printer. The result was a prototype of a new controller handle in half of the scheduled time.
Combining Function and Form
For nearly 50 years, FORCE America has been creating motion and control products for mobile hydraulic systems incorporated into trucks and agricultural equipment used for snow removal, logging, mining, harvesting, and other heavy-duty tasks.
The company contracted with ADC to design a controller handle for municipal snow plows. It had to accommodate three different joysticks for controlling plow blades, three switches for salt distribution, and the electronics to control and light the device. And while reliability is an overriding requirement in FORCE America’s designs, they also need to be ergonomically flexible to accommodate different-sized hands.
David Zech, mechanical project engineer at FORCE America, thought ADC would be perfectly suited to realize these dual design objectives.
“In previous projects, ADC had proven it has the design engineering skills to produce a final product design that is both structurally sound and cost effective,” says Zech. He also pointed to the advantage of ADC having all the tools to do the job in one place.
“Because the design, moldmaking, and part manufacture are located in the same ADC facility, we are able to reduce the time needed from conception to manufacture,” says Zech. “The setup also decreases the cycle time when unforeseen changes arise in new product design.”
![]() ADC used an ATOS GOM white-light scanner to capture geometry from a clay model of the FORCE AMERICA controller. |
TheTools to Make a Leap
The controller handle project epitomizes ADC’s expertise in DSSP, which describes a group of technologies that enable users to move efficiently between physical and digital worlds. At the center of the process is Geomagic Studio software, which ADC has used in design engineering projects for a diverse range of customers, from Harley-Davidson to Fiskars.
“Geomagic Studio fundamentally changes the way you can design,” says Mark Schaefer, ADC president. “It provides the tools that enable you to make a quick leap from a physical model with a shape and feel everyone likes to an accurate CAD model for manufacturing.”
FORCE America started the project by giving ADC the internal components that would be required in the new design and a rough clay model of the shape. Using PTC’s Pro/ENGINEER, Schaefer created CAD models of the buttons and circuit board areas based on existing drawings and 3D scans. He then created a volume model around the components to provide a clearance guideline for the clay work.
Saving a Month in Iterations
ADC used the Objet 3D printing system system to produce a rapid prototype of a volumetric clearance model for the controller’s internal components. Then Chris Mulhall, a senior engineer at ADC, added clay to the prototype to ensure that the final offset (wall thickness) would not interfere with any of the internal components and to sculpt the controller so it met FORCE America’s ergonomic and styling requirements. Changes were made to the clay by hand until the look and feel was right.
![]() Geomagic Studio software was used to smooth out inconsistencies in the scan and to flatten the button area. |
“Making a part that feels and looks good is very difficult,” says Schaefer. “Using clay as the media to get the shape right saved about a month in CAD and physical prototyping iterations.”
Next ADC Reverse Engineering Manager Greg Groth captured the clay model’s geometry with a GOM ATOS white-light scanner. He saved the data as an STL file and imported it into Geomagic Studio software. Within Geomagic, he smoothed out inconsistencies in the clay surface, flattened the button area, and created models for the top and bottom shells of the handle and a safety switch for the back of the controller. The models were turned back over to Schaefer, who generated parting line surfaces and curves in Pro/ENGINEER.
The Pro/ENGINEER models were then brought back into Geomagic Studio, where Groth modified the parts to meet tooling draft requirements. Once the drafts were set, Groth created offset surfaces to maintain the wall thicknesses of the parts. He then used Geomagic Studio to create surfaces of the final parts and define the offset internal geometry.
Structural ribs, holes, and assembly features were finally added in Pro/ENGINEER and the final models were printed on the Objet system.
“Once the clay model was perfected, it was only a matter of days to move from scan data to a final, tool-ready prototype with switches and components ready for installation,” says Schaefer. Much of that speed can be attributed to the interchange between Geomagic Studio and Pro/ENGINEER throughout design stages.
“The combination of Geomagic Studio and Pro/ENGINEER enabled us to quickly capture the clay model, check the draft, and modify the surface geometry to make the controller manufacturable,” says Groth. “This is a perfect example of Geomagic and CAD working together to generate a high-quality design very quickly.”
![]() The final surface model generated in Studio is ready for Pro/E where structural ribs, holes, and assembly features will be added. |
The job, scheduled for six weeks, was completed in just three. While ADC was completing the handle design, engineers at FORCE America were able to work on other parts of the new system assembly. Most importantly to Zech, ADC was able to ensure design quality in the early stages.
“By allowing ADC to design and build the parts and the molds, we were able to use the knowledge they have from many previous projects and make quality an integral part of the initial design,” he says. “ADC allowed us to provide a product that is new and improved from the previous product, yet has the quality look and feel that customers expect from FORCE America.”
More Info:
ADC
Pewaukee, WI
FORCE America
Burnsville, MN
Geomagic
Research Triangle Park, NC
GOM ATOS
Braunschweig, Germany
Objet Geometries
Rehovot, Israel
PTC
Needham, MA
Bob Cramblitt is principal of Cramblitt & Company in Cary, N.C., and writes about design, engineering, and IT technologies. Send e-mail about this article to [email protected].
Subscribe to our FREE magazine,
FREE email newsletters or both!Latest News
About the Author

DE’s editors contribute news and new product announcements to Digital Engineering.
Press releases may be sent to them via [email protected].
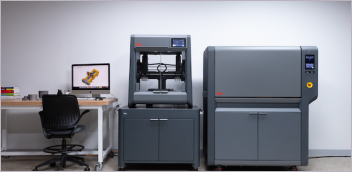
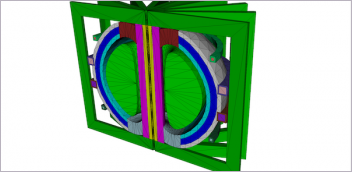
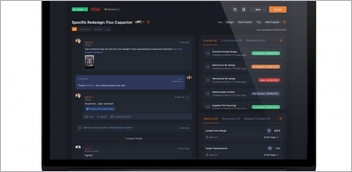
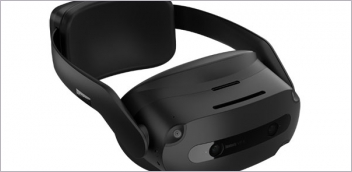