Latest News
December 13, 2007
By 3D Systems
![]() |
Founded in 1980, AdvaTech Manufacturing (Goodland, Ind.) has been transformed from a traditional tool shop into a high-tech Rapid Prototyping and Rapid Manufacturing provider.
Thanks to 3D Systems’ Selective Laser Sintering technology, AdvaTech is now producing big, accurate, tough, production-quality parts from digital data for its customers in various industry segments and with a variety of application needs.
Selective Laser Sintering, or SLS®, an advanced Additive Manufacturing technology, enables the quick production of parts that customers in industries such as automotive, aerospace, architecture, medical and consumer goods rely on.
Parts that had to be built in sections can now be built in one, fully functioning piece with 3D Systems’ (Rock Hill, S.C.) Pro solutions and the Sinterstation® Pro SLS® System, maximum build volume of 21 5/8 inches by 21 5/8 inches by 28 7/8 inches.
It is just one step from 3-D CAD design to finished part with 3D Systems’ solutions, which save time and money. Users can directly manufacture customized short-production runs or prototypes and meet demanding part specifications with advanced process control.
3D Systems helped AdvaTech improve a car dashboard prototype. Previously, the part was produced in numerous pieces, large and small, glued together and finished. But with 3D Systems’ technology, AdvaTech built the center dashboard spanning 28 inches by 20 inches for a customer on its Sinterstation® Pro SLS® System in one piece using DuraForm® PA Plastic. It was a perfect fit and functionally superior with no finishing necessary. AdvaTech’s customer was ecstatic with the quick turnaround time, quality of the dashboard and tight tolerances. There was no expensive tooling or complex change-overs, just digital design to plastic prototype.
With the Sinterstation® Pro SLS® System, users like AdvaTech experience superior throughput and use, virtually no time between builds for maximum part-building and function. It takes days, not months, to produce the final prototype—providing customers with a significant time-to-market advantage over their competitors.
AdvaTech’s customer base has grown as the company has shown the Sinterstation® Pro SLS® System’s capabilities. From a one-person design shop to worldwide corporations, only 3D Systems’ solutions enable users like AdvaTech to provide the diverse, large, durable, accurate parts.
SLS® technology enables AdvaTech to attract new customers and continue to satisfy its existing ones. AdvaTech helped a consumer product company get a single-piece fan blade to market faster. Used for functional testing thanks to the strength of DuraForm® PA Plastic, the company needed to prove the fan provided enough airflow. Built with precision, this nearly two-foot wide by two-foot high fan stood the test of high speeds during form, fit and function testing. Errors were identified early in the design process, prior to manufacturing, with 3D Systems’ SLS® technology.
Powered by the ProScan™ Imaging System, 3D Systems’ Sinterstation® Pro SLS® System delivers big parts with outstanding definition, surface finish and accuracy, built from the toughest available plastics. The DuraForm® family of plastics creates durable, high-quality, fully testable parts.
3D Systems
333 Three D Systems Circle
Rock Hill, SC 29730
800.889.2964
3dsystems.com
Subscribe to our FREE magazine,
FREE email newsletters or both!Latest News
About the Author

DE’s editors contribute news and new product announcements to Digital Engineering.
Press releases may be sent to them via [email protected].
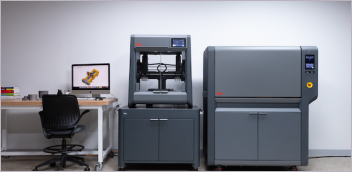
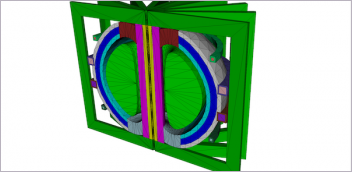
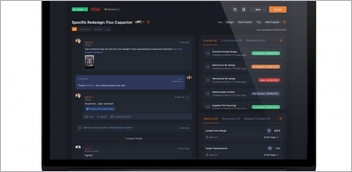
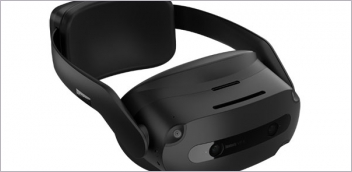