Latest News
May 13, 2015
Over the past few decades, the traditional manufacturing process is substantially transforming to be more digitized with an increase in growing technologies such as virtual simulation, 3D printing, intelligent robots, drones and sensors.
The widespread adoption of information and communications technology by the manufacturing sector is causing a major disruption in product development, production and the entire logistics chain. This change is likely to transform the future of manufacturing sector and as such, it has become mandatory now for manufacturers to adapt to this change, if they are not willing to be left behind by their competitors.
The term Industry 4.0 is widely used across the Europe to describe this industrial revolution, while in countries like the US, it is also being termed as the Internet of Things or more precisely, Industrial Internet.
However, all these terms have a singular meaning, which is related to transforming traditional manufacturing into more advanced, intelligent and collaborative manufacturing through a digital approach.
From a broader perspective, this revolution can be considered to possess four main characteristics as defined by a recent report from Deloitte:
- Vertical Networking, which refers to the networking of smart production systems, smart logistics and smart marketing services. All these are focused specifically based on individualized, customer-specific needs.
- Horizontal Integration using global collaboration of partners and customers, with new business partnering models across various countries.
- Through-Engineering refers to applying engineering into the entire manufacturing operations right from development to end product and its entire lifecycle.
- Acceleration through Exponential Technologies such as advanced robotics and sensor technology to develop highly cognitive autonomous solutions.
Impact of Digital Industrial Revolution
Increasing opportunities for new entrants
The dramatic increase in computing power and capabilities has made it possible to utilize CAD, CAE and CAM tools extensively. This fast-moving digital design culture is allowing new entrants an opportunity to compete with traditional manufacturers, since cost of developing infrastructure has reduced significantly following the Moore’s law. Such easy entry of new manufacturers is putting pressure on existing ones to ramp up their capabilities and stay ahead in the competition.
Decoupling research, engineering and manufacturing capabilities
The use of advanced modeling and simulation techniques has made it possible to decouple the product development stages such as research, engineering and manufacturing from each other. The use of computers and the Internet enables engineers to perform these three activities at different geographic locations. This allows better collaboration of supply chain vendors, design consultants and manufacturing processes.
The Boeing 787 Dreamliner is an excellent example of how a plane is built using parts developed from all regions of the world. Apparently, the Dreamliner is manufactured with components from 287 suppliers across 22 countries. Using such a complex global network to accomplish manufacturing could not be imagined decade ago.
Access to advanced manufacturing technology around the globe
During early days, CAM was exclusively restricted to aerospace and automotive companies in a few developed countries. Today, this technology has not remained exclusive and is widely available to manufacturers around the globe. Countries from around the globe are increasingly adopting digital modeling approach for their manufacturing requirements. In fact, the APAC region has overtaken America as the fastest growing market for digital modeling products.
Allows easy, exact replication of manufacturing processes
With digital transformation, it is possible for organizations to replicate their production capabilities at any location. Manufacturers can easily relocate their production facility to emerging countries, since identical information can be produced digitally. A decade ago, such transformation could not be even imagined.
Impact of Exponential Technologies
Exponential technologies are expected to play a major role in the digital transformation process. Additive manufacturing, or 3D printing, is one such example that boosts productivity and integrates customer feedback and customization in manufacturing. 3D printing involves adding the material to develop objects rather than the conventional subtractive technique where the object is produced by removing the material either by milling, drilling or machining.
However, the major concern, like every new technology, is its investment. With conventional manufacturing techniques, the cost of developing the product will be high initially and later decrease with mass production.
Similarly, with additive manufacturing, the cost can be reduced significantly. At present, conventional manufacturing is more attractive for mass production; 3D printing on the contrary is even cost-effective for smaller volumes. Also, no special tooling is required to develop products that are customized as per customer needs.
The digital transformation — or the fourth industrial revolution — is about to bring a profound change in a way products are designed, manufactured and supplied to the market. The revolution is likely to increase competitiveness and provide opportunities for manufacturers to develop products more aligned with individual customer needs.
Manufacturers need to develop required talent and IT infrastructure to make their organizations ready to face the transformation. Major exponential technologies such as 3D printing should be in the agenda of every manufacturer eying the development of world-class products. Companies need to embrace their potential to be ready for such a radical industrial transformation.
Gaurang Trivedi is an engineering consultant at TrueCADD. He has applied his engineering expertise across several highly complex and big scale projects, consequently managing to flawlessly deliver as per the client requirements.
Subscribe to our FREE magazine,
FREE email newsletters or both!Latest News
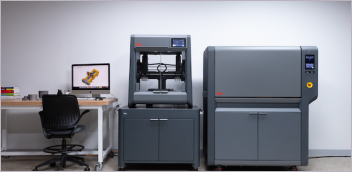
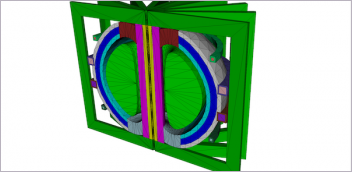
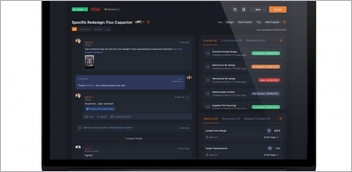
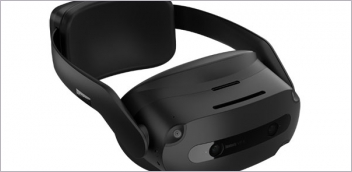