A Convergence of Disciplines
Finite Element Analysis is spreading over the land and the developers are working like mad to make sure everybody benefits.
Latest News
June 1, 2004
By Vince Adams
In a recent discussion of the growing use of FEA at the design engineer level, a friend and colleague, Paris Altidis, quoted Dirty Harry: “A man’s gotta know his limitations.”
In theory, making advanced solver capabilities as easy to use and as accessible as CAD is a great thing. Likewise, having design engineers perform first-pass or (as occurs in many companies) all the analysis on a new product or configuration can lead to faster design cycles and more robust products. However, experience has shown that few part-time users, and, let’s face it, not many full-time users, actually know their limitations. Though not exactly criminal, the use of FEA at many companies is better described by another Harry Callahan quote: “Do you feel lucky, punk,well, do ya?”
This is an image of an analysis model of a medical stent made of Nitinol, a special shape-memory alloy. It is being viewed in ABAQUS/Standard, which has libraries of material models and elements that engineers use to accurately model product and to perform real-world simulations of demanding operating environments. Image courtesy of ABAQUS.
The Leading PlayersIf relying on luck makes you nervous, then we would all be well served by a review of where the technology is, where it is going, and how companies that use FEA as a design driver versus a design checker can best implement the technology to minimize misuse and improve efficiency.
Richard Bush
To that end, some leading players in analysis software have agreed to share their views on the state of the technology. We spoke with Dave Branch, Noran Engineering, director of sales; Greg Brown, product manager of Interactive Products for ABAQUS; John Buchowski, PTC’s Simulation Products line manager; Richard Bush, product marketing manager for NX Digital Simulation at UGS PLM Solutions; Todd Evans, MSC. Software spokesperson; Suchit Jain, vice president of Analysis Products at COSMOS/SolidWorks; Hans Kraus, the senior application engineer at IBM’s Product Lifecycle Management division; Ravi Kumar, manager of New Business Development at ANSYS; and Bob Williams, product manager at ALGOR.
Suchit Jain
The discussion considers three main categories of users,albeit with fuzzy borders, power users (long-term, well-informed), moderate users (part-time or limited), and new users. Each participant commented on how their company addresses FEA’s moderate-user base primarily while helping the new user move up to that moderate level, and how they do that while avoiding some of the familiar roadblocks and kinks in the learning curve. DE also asked these visionaries to speculate on the future of the technology and to share what their companies are doing to prepare for the future.
It’s All About Benefits and RelationshipsMost of our commentators felt that a critical challenge for companies entering into or preparing to deepen their commitment to simulation is to get a better handle on its business benefits. And we’re not talking just justifying the software to the boss.
“The challenge for companies is to find better ways of implementing FE tools to improve their bottom line,” says Greg Brown. “Once the strategic value of analysis is recognized in a company’s business and processes, analysis quality is usually better and it becomes more widely deployed.”
ANSYS’s Kumar attests to the impact these technologies can have on how companies develop products. “Simulation makes your design process more flexible, more agile,” he says. “You can keep your design options open for a longer time.” Many vendors have recognized this and are prepared to help their customers. Both COSMOS and MSC have developed ROI calculators that focus more on process than on software seats. “The FEA vendor community needs to demonstrate positive business impact and value for customers,” says Richard Bush of UGS PLM Solutions.
And when it comes to user demands, Kumar notes that users seek three things in a simulation solution: a solution that solves their problem with reasonable approximation; a solution that fits their CAD and user environments; and a solution that fits within their process and workflow. He says ANSYS encourages users to work directly with suppliers for improved products.
All the participants were united in one area: their success is ultimately tied to user success, and they are all taking steps toward developing closer client relationships. Bush takes this a step further: “Vendors have a responsibility for the use of their products.” Noran Engineering’s Branch agrees: “Vendors must understand customer needs and costs to provide tools that can impact the bottom line,” he says, explaining that NE/Nastran is “user-community robust,” reflecting user input and suggestions for the software.
One way to user success is to make analysis tools manageable. “Software vendors need to find ways to make analysis tools and the results more accessible to people who wouldn’t normally use them,” says Bush. MSC.Software’s Evans notes that many manu- facturers are pushing engineering further down the supply chain to reduce internal costs. “These companies are not necessarily equipped to take on this type of work,” he says.
Suchit Jain
According to Brown of ABAQUS, “Customers are looking for a more unified approach to bring various technologies and disciplines together. There will be a general “blurring” of the boundaries between various solution algorithms and physics as more unification takes place.” MSC.Software, ANSYS, and ABAQUS say they are approaching this problem by partnering with providers of specialized tools. Kumar says vendors have to “make sure their technology is deep and robust” however they achieve it. The trick is to make all this happen without overwhelming or constraining the user.
MSC.Software’s approach follows its growth path from SimDesigner, a CAD-embedded tool, to SimOffice, which uses the deep MSC.Patran interface. IBM has several products, all with three-letter acronyms, that sequentially add capabilities. COSMOS,a pioneer in mainstream analysis,starts with COSMOSExpress, a limited and inexpensive (free to SolidWorks users) analysis product, and then provides a growth path to COSMOSWorks, DesignSTAR, and finally COSMOSM, its full-featured analysis product that bundles multiple algorithms for varying physics.
Image courtesy of PTC
SolidWorks,s VP of Analysis Products, Suchit Jain, says, “New users would find COSMOSM difficult to use and we don,t recommend it for them.” Noran, the maker of NE/Nastran, has entered this arena with its recent release of NEiCAD, its contender for the CAD-embedded analysis market. Branch insists that “introductory interfaces can only assist in the long-term FE goals of a company, if they provide a seamless interface to higher end analysis.”
Broad Capabilities, Access Control
The opposite approach is to use the honor system, if you will, and provide all the capabilities of the solver technology in a single interface. According to Williams, “At ALGOR, we decided it was better to have one user interface that is appropriate for users of all levels. A user, regardless of level, should be able to spend time thinking through a model,s approximations and simplifications and then evaluate the results rather than spending time pushing the buttons.”
Pro/Mechanica from PTC, ALGOR, NX MasterFEM and FEMAP from UGS, and ABAQUS CAE are examples of the all-levels-of-users approach. Brown at ABAQUS cautions that full-featured tools still present a danger to new users who may be tempted to stray from their comfort-zone after some initial success. “We don,t feel that general-purpose, full-featured FEA is always the best solution for new users; we,d rather see power users mentor new users, if they need general-purpose FEA.” He adds, “people new to analysis typically don,t look to ABAQUS.”
“It is an art to find the proper balance between making software easy to use and offering the advanced tools that power users want,” says Williams. A company embracing an analysis solution developed on this platform must be ready to police the tool,s use.
A few vendors provide tools to control access to capabilities. CATIA V5 offers “skill-level based customization of the GUI by a system administrator.” ANSYS also uses tools within FlexLM, its licensing tool, to provide user-specific functionality. This, of course, relies on system administrators qualified to judge a user,s competence.
Another solution is to handle most of the analysis in the background through customized applications or templates based on design requirements. These can be as simple as record-and-play macros or “deep customization” as Kumar puts it. Brown believes that these “focused applications defined by company standards and processes” are the way to go for FEA in the design process. ANSYS and UGS also have strong tools for this type of customization.
“The current state of customizatiom requires dependency on a developer and big dollars for startup and maintenance,” warns Bush, adding that UGS addresses this in upcoming releases of NX. Jain also sees this trend affecting users: “Perhaps in the future we,ll see predefined features for such hard-to-understand areas as boundary conditions where users can create their own frequently used palettes of loads and constraints.”
While the vendors are working to provide functionality in FEA to a market with wide variations in user skill levels, they say users must shoulder a share of the responsibility. These three snapshots show the different capabilities of the ANSYS Workbench environment. (Top) CAD integration and design modeling; (center) robust meshing; (bottom) advanced simulation.
This is a cyclic symmetry modal analysis of a turbine blade sector model being studied using ANSYS. The above images courtesy of ANSYS.
The key to the usability of PTC,s Mechanica is its technology based on the P method combined with the integration of,simulation into the user interface and workflow of Pro/Engineer. This image shows how Mechanica looks as a module of Pro/E as well as its P mesh.
“There is currently a large gap between what the technology can do and what the engineers actually do,” says Evans. “Only through education and an open dialogue with vendors can engineers and organizations get more value and functionality from their technology investments.”
And, says Williams, “While it may be increasingly easy for new users to set up models and get results, FEA is not a magic box and engineers still have a responsibility to realize the limitations of the tools they are using and critically assess their results. The impact of FEA will be proportional to the investment the company is willing to make to fully integrate FEA into their design process. Companies that are not willing to make that investment may be better off designing by experience.”
Brown says that ABAQUS feels that in some cases it is better “to use an analysis consulting firm for ]the] first analysis projects than simply going off and buying ... inexpensive software ... The consultant can guide a firm through the right questions about their analysis , ]and] can develop the methodologies that they can then follow.”
“Product knowledge,” says Kumar, “is a better indicator of success than software acumen.”
One clear solution is deeper and more focused training. Branch feels that most companies don,t budget nearly enough for training, and Williams advises that “training is a wise investment and should not have negative connotations. By sending multiple users to training, they can discuss what they have learned and help each other when applying the concepts.”
All of the participants support education, going so far as to direct sales people to mention and encourage training at the point of sale. ALGOR, COSMOS, IBM, and PTC actively support open web-based training as well as other means of disseminating product and FE methods information. And UGS recently partnered with NAFEMS (nafems. org), an international nonprofit association dedicated to FEA quality and education. This relationship may give NAFEMS the hand it needs to make an impact in North America, a goal it has yet to achieve.
Access Is CriticalAs analysis becomes more prevalent in design engineering, our visionaries report a sense that some analysis pros fear obsolescence looms on their horizon. But evolution defeats extinction.
According to Williams, “The analyst,s role is not being eliminated but is often transformed into team leader or internal consultant.” He encourages users to “conduct a peer review with a resident expert. Better products result from collaborations that bring more than one point of view to the table.” Both Bush and Brown stated that access to mentors is critical to new or part-time users.
And it might be argued that such access grows more critical as FEA becomes more accessible. The combination of rapidly dropping hardware prices and the popularity of Windows may be the biggest factor driving FEA to evolve from a specialist tool to a generalist one. All the participants have one or more offerings that run under Windows and three of the companies,ALGOR, COSMOS, and Noran,only run under Windows.
It wasn,t too long ago that the limitations of IGES or meshing algorithms capped the level of complexity that was practical in an analysis. Today, with improved IGES and STEP translators, ACIS and Parasolids kernel-based meshers, and CAD-embedded modelers, engineers can analyze the most complicated (often overly complicated) CAD models. Still, Williams has seen that “it is challenging to teach users how to best use their CAD models for FEA,there are still valid reasons for simplifying models.” Kumar feels that “users are challenged to ensure that the quality of their CAD data is good from a parametric nature.”

But IBM,s Kraus cautions that the use of any translator may limit the effectiveness of the greater product database. “Better translators for CAD geometry still break the link to associativity. Better integration of advanced analysis tools in CAD is the better solution,” he says. “Over 80 percent of a user,s time is spent on geometry and mesh manipulation due to integration limitations.” Conversely, however, with the current state of the technology, Brown thinks that many users are missing out on cutting-edge technology because of their dependence on these limited tools.
Is It a Culture Change?PTC’s Buchowski notes that “while many organizations see FE trickle down to the design group from specialists, others see simulation pushed up from the bottom out of frustration with the responsiveness of internal organizations.” He thinks the design culture is changing: “old ways are being displaced by new ways.
John Buchowski
In general, our participants expressed great optimism for the technology and the growing ranks of new users. These experts feel that the user base is rising to the challenge of increased functionality and more unified physics with diligence and perseverance, embracing a culture change.
“The timing is right to get involved with simulation technology,” says Kumar, adding that “an important area of growth will be in the engineer,s ability to account for design variations and decreasing the sensitivity of designs to inputs.”
“FEA is not a mature industry in terms of technology, materials, computing, and new mathematical approaches,” says Brown. “This makes FEA an exciting and challenging place to be. Optimization technologies will be a big area of growth in the coming years. Due to the fragmented nature of this market and disjointed tools, unification of disciplines will continue.”
Elaborating on the industry, Bush says: “The commitment to CAE and simulation is significant with immense capabilities and a strong history. Put all this together and good things happen.”
Good things are happening to companies embracing FEA technology, but a carefully considered plan for making it successful is critical. Where companies once relied on specialists immersed in the technology, today we must acknowledge that simulation tools, despite the easy interfaces, embody advanced engineering, physics, and failure theory. Companies looking to gain a competitive advantage with FEA must look to partner with vendors as well as internal and external experts to guide them past potholes and roadblocks. Vendors have provided software that enables engineers, who, if they outrun their headlights, might blow past the “bridge out” sign wind up in the river.
Vince Adams is director of Analysis Services at IMPACT Engineering Solutions, an engineering support firm. A lecturer, he is co-author of Building Better Products with Finite Element Analysis. Contact him via e-mail at Desktop Engineering Feedback.
Companies Mentioned in the ArticleSubscribe to our FREE magazine,
FREE email newsletters or both!Latest News
About the Author

DE’s editors contribute news and new product announcements to Digital Engineering.
Press releases may be sent to them via [email protected].
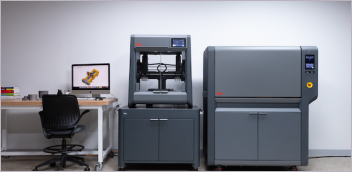
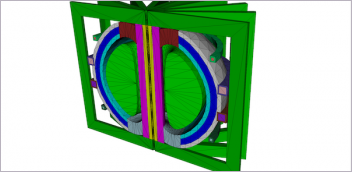
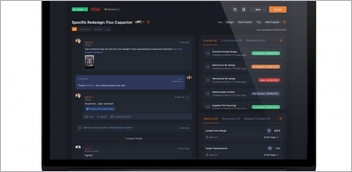
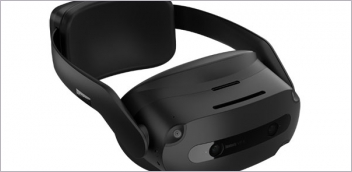