CFdesign UVCalc Module Removes Barriers for Design Engineers to Validate Reactor Performance for UV Light Disinfection
Blue Ridge Numerics and Bolton Photosciences collaborate to provide upfront CFD UV reactor design tool.
Latest News
March 19, 2009
By DE Editors
Blue Ridge Numerics, Inc. has released the new CFdesign UVCalc Module, an upfront CFD solution for simulating and validating ultraviolet (UV) reactor performance to ensure accurate fluence rates (irradiances) for UV light disinfection. The use of germicidal UV light is a rapidly expanding technology that is used to ensure public safety by deactivating the DNA of bacteria, viruses, and other pathogens, removing their ability to multiply and cause disease.
With the new partnership of Blue Ridge Numerics, Inc. and Bolton Photosciences, Inc., design engineers developing UV applications for drinking water disinfection, wastewater treatment, and manufacturing processes for the food and beverage, medical device, pharmaceutical, and semiconductors industries, among others, can now leverage fluid flow and UV calculation capabilities to speed up and optimize their product development process.
For many years, CFdesign, the leading design tool for Upfront CFD, has successfully been used to simulate the hydraulic performance through UV reactors. To build on existing capabilities and address the current needs of its customers, Blue Ridge Numerics realized the importance of a reliable solution for predicting UV fluence rates in CFdesign. The knowledge and experience needed came from a new partnership with Dr. Jim Bolton, a recognized expert in the UV calculation field and developer of UVCalc, a trusted and tested UV calculation tool currently in its 3rd generation.
The combination of CFdesign and the UVCalc Module allows engineers to:
- Determine the distribution of UV dose along various flow paths in the reactors and determine the impact of other factors, such as the flow rate, flow distribution, and axial mixing, all which can affect the fluence or UV dose and the performance of the reactor.
- Run scenarios that include simulating the effect of inlet flow distribution changes (piping), different transmittance of the fluids, changes in flow rate or flow obstructions.
- See side-by-side design comparison and data results of multiple reactor concepts through contour plots, cut planes, iso-surface, particle traces and vectors.
- Explore a broad spectrum of possibilities to achieve an optimal design before proceeding with the certification process
For more information, visit Blue Ridge Numerics.
Sources: Press materials received from the company and additional information gleaned from the company’s website.
Subscribe to our FREE magazine,
FREE email newsletters or both!Latest News
About the Author

DE’s editors contribute news and new product announcements to Digital Engineering.
Press releases may be sent to them via [email protected].
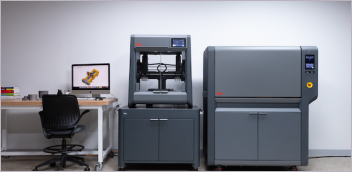
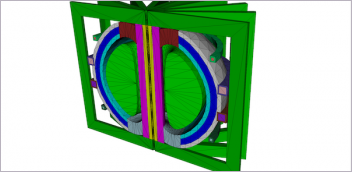
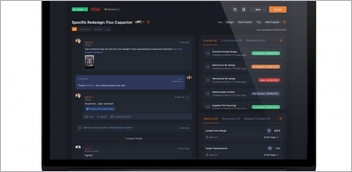
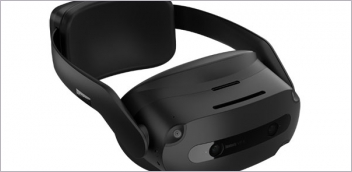