Latest News
February 1, 2007
By Chuck Cimalore, Omnify Software
Editor’s note: This is the extended version of this commentary from the March 2007 DE.
Manufacturers’ business needs have changed significantly over the past several years. In that time, the roles of enterprise resource planning(ERP) and product lifecycle management (PLM) have evolved into key solutions critical to many success stories. Each technology brings unique value to the enterprise, and when combined, ERP and PLM provide a wholly collaborative environment that can have a large impact on successful product development performance and the ability to maintain a competitive advantage.
ERP and PLM address different business needs for manufacturers. Because some confusion remains within industry as to the purpose of each, it is important to clarify their roles. It is important for manufacturers to understand why each is so critical to their success and having this clarification will help manufacturers maximize the functionality of each system and gain the most from their investments.
Synchronization of Information
It is the integration of ERP and PLM systems that allows direct sharing of engineering and manufacturing data through an automated process. It eliminates the tedious and error-prone task of hand-entering information, resulting in improved data integrity across the organization. An integrated environment decreases redundant efforts and guarantees that all departments involved in the product development and manufacturing cycle have access to current and accurate product data.By synchronizing these two systems, engineering teams are able to access business-level data from the ERP system to support better design processes and manufacturing is ensured receipt of the most current design information for more efficient production processes.
ERP, integrated with PLM, reduces data duplication, speeds product development cycles, and improves new product turnaround time, enhancing the overall process in getting products to market and ultimately sustaining a company’s competitive position.
Case in Point
Understanding the importance of creating a cohesive environment between ERP and PLM was quite clear for a leading developer of enterprise servers.
The company was running into data inaccuracies due to manual processes and disparate product information. Engineering, operations, document,and quality control team members were each tracking their design and operations data manually and in separate databases. Synchronization of these databases was a time-consuming task and proved to be a considerable strain on resources. The manufacturer had an ERP system in place to manage all of the operations-centric business activities such as financials, purchasing, planning, and work orders. But the ERP system did not address their engineering design requirements. The manufacturer lacked a system that understood revision control and engineering change processes. In order to gain control of its product design process and eliminate disparate product information, the manufacturer purchased a PLM system.
A PLM system is designed to manage the full gamut of engineering information in a single location through the many stages of product development The enterprise server manufacturer used the PLM system to manage the lifecycle and all revisions of bill of materials (BOM),provide revision control of engineering documents (such as assembly drawings, schematics, and data sheets), electronically route approvals for new part requests (NPRs), manage and automate their engineering change orders (ECOs), and control approved manufacturer’s list (AML)changes. More importantly, the PLM system helped bridge the gap between engineering and manufacturing.

The ability to directly share data between the two environments and pull information from ERP into the PLM database gives engineers visibility into extended information including cost, inventory, vendor status, and lead times. Access to this type of information allowed engineering to perform analysis on cost, product availability, and compliance early in the design and development cycle, helping make better design decisions and eliminate costly late-stage redesign.
Understanding the function of each technology (ERP and PLM) and the value each added, positioned the manufacturer to focus on core competencies, cut new product introduction time in half, and beat its competitors to market.
ERP—Managing the Business Data
An ERP system is a business management tool used to fulfill the needs of many facets of a company including finance and accounting,distribution, human resources, customer service, and manufacturing. ERP supports these various departments by delivering improved processes such as an automated method for order fulfillment, providing a single location for tracking cost information to ensure consistency, and helping human resources to standardize its information.
ERP is used to manage the logistics of getting a product to market once a design is released (from engineering). It is geared toward capturing information at the manufacturing stages of a product; prototypes,production runs, redesigns, etc. This information typically consists of a BOM, manufacturing and test procedures, schedules and timelines, and logistics, which are then used to execute the entire manufacturing process.
Due to the inherent purpose of an ERP system, many are not designed to manage the amount and type of information required for engineering.Most systems do not contain the detailed information that engineers need to drive design. In addition, ERP systems typically do not provide the security or capability to enable external manufacturing partners to directly access product data and participate in development processes.
As mentioned above, the enterprise server manufacturer leveraged its ERP system to manage all of its business-centric information such as inventory management and purchasing processes. When they wanted to achieve control over all of the design and development information, the manufacturer turned to PLM technology.
PLM—Managing the Product Data
PLM was designed to manage product data throughout the product lifecycle. A PLM system is crucial during the design phase, where engineers need instant access to data like specifications, engineering parameters, and documentation. PLM centralizes all of this information for easy access by all team members and tracks and manages component data, BOMs, product documentation, engineering changes and revisions,as well as compliance data. PLM systems also offer the flexibility to support the many iterations of a design before it reaches the prototype and manufacturing phases.
A key component of a PLM system is that it provides an automated change management facility that allows users to electronically propose product changes (redlines) to BOMs, documents, and vendor/supplier information. Leveraging a workflow engine, these changes are then automatically routed to the appropriate resources for electronic signatures. Once all constituents have approved the change, the PLM system automatically updates the affected products with the suggested changes, and then provides the updated information to the ERP system. An electronic change process eliminates manual data entry errors, streamlines routing, and allows all involved resources to view and sign changes simultaneously. All of these factors result in a significant time savings for the engineering change process that also ensures everyone involved in a project has the most current information.
It’s never easy to adopt new enterprise technology, but it is important to understand the value that the technology brings to each department and the enterprise as a whole.
Complementary applications like PLM and ERP play a key role in supporting and improving product development and achieving bottom line operational benefits.
Recognizing their distinctive features as well as the benefits of creating an integrated environment will help manufacturers deliver higher quality products in less time and maintain competitive advantage in the marketplace.
Chuck Cimalore is the chief technology officer for Omnify Software.Send your comments about this article through e-mail by clicking here. Please reference “Collaborating for Success” in your message.
Subscribe to our FREE magazine,
FREE email newsletters or both!Latest News
About the Author

DE’s editors contribute news and new product announcements to Digital Engineering.
Press releases may be sent to them via [email protected].
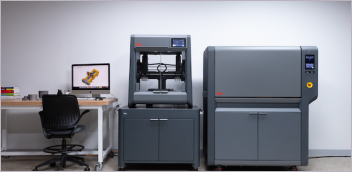
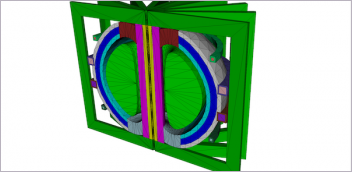
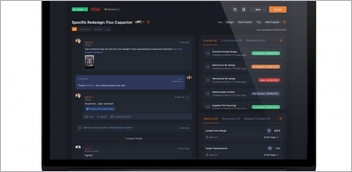
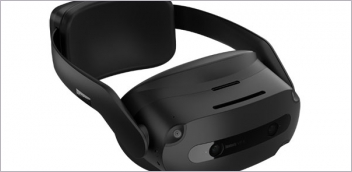