Latest News
May 1, 2012
By Adrian Martin
Nearly 2 million hybrid electric vehicles (HEVs) have been sold in the U.S. since 1999, according to the U.S. Department of Energy. And with soaring gasoline prices and stringent governmental regulations mandating better vehicle fuel efficiency and reduced vehicle emissions, interest in HEVs grows daily. Many characteristics of HEVs—energy efficiency, vehicle performance, distance traveled and total cost, for example—depend on the vehicle’s powertrain system design and its control strategy.
![]() |
Here, a model front panel features code programmed in LabVIEW software. Users can configure the model according to the needs of the test carried out. |
A team of engineers at Robotiker-Tecnalia in Spain, one of the largest research institutes in Europe, developed Dynacar, a parametrized model that can simulate HEV powertrains, as well as powertrains for electric and conventional fossil-fuel vehicles. Dynacar simulates longitudinal and lateral vehicle dynamics—as well as the powertrain system components in real time, for testing in model-in-the-loop (MIL), hardware-in-the-loop (HIL) and dynamometer test applications.
![]() |
This HEV test bench architecture layout shows virtual models of the Dynacar dynamic model and real hardware. |
One key component of the model is that it integrates digital simulations with physical simulations of powertrain components. This combination enables HuIL (human-in-the-loop) testing, which provides an advanced virtual driving simulator for complete vehicle simulation over a test bench. By using HuIL simulation, the team was able to develop analyses of driver requirements and the dynamic response of an entire HEV.
![]() |
The Dynacar engine selection configuration utility. |
The Robotiker-Tecnalia team used NI LabVIEW as the development environment for the vehicle model. They used NI VeriStand real-time testing software for model integration, stimulus generation, and data logging, and the INERTIA add-on for NI VeriStand, created by Wineman Technology, to implement multi-mode control of a dynamometer-based test cell. Additionally, the team used NI’s PXI hardware, and a range of vehicle bus communication cards, and data acquisition (DA) interfaces.
HEV Full Dynamic Model
HEVs have electrical components—such as energy storage systems (batteries or supercapacitors), electric machines, power inverters and control systems—that are key factors in the electrical powertrain design phase. Because these components can be complex, the team used high-fidelity tools for modeling and simulation in the conceptual and preliminary design stages of its HEV to analyze the behavior of all components integrated in the powertrain.
After defining the general powertrain architecture, Robotiker-Tecnalia conducted model-based studies to implement control and optimization strategies to manage the different energy sources. They also considered the differences in the dynamic responses of the components in an electrical powertrain from those in conventional powertrains. Because the electrical powertrain provides greater motor speed, they developed a new drive control strategy to give HEV motorists equal or increased vehicle drivability, comfort and safety.
They considered both longitudinal and lateral vehicle dynamic responses with the powertrain components and dynamic effects, as well as tire data and the modeling approach of road-to-tire contact. The model target was to calculate the vehicle speed and position, in addition to such dynamic variables as force, torque, slip angle, lateral acceleration and vertical axis load.
These variables are part of the differential equations that define the vehicle dynamic response, such as roll stiffness, weight transfer and vehicle model, according to such inputs as acceleration and brake pedal position, steering and wheel position, as well as tire, geometry, roll center, inertia, weight and powertrain parameters. To solve the differential equations, the team used an integration solver based on the Runge-Kutta method in NI LabVIEW.
Architecture of the Integrated HEV Test Bench
The team replaced the powertrain electric component dynamic submodels with a PXI platform populated with real electronic components. They ran two motors with a physical coupling: one working as a load and the other as a traction drive. The load drive and traction drive torque reference commands were calculated using the Dynacar vehicle dynamic model. Drive response feedback signals were sent back to the Dynacar model through the NI PXI platform. This data was used in the vehicle dynamic response calculation.
![]() |
The Dynacar wheel selection configuration utility. |
The PXI platform integrates multiple I/O options. These include data acquisition with the NI PXI-6229 module, as well as communication and data interfaces required by a variety of applications with the NI PXI-8464 two-port, transceiver-selectable CAN interface. The team also developed additional communication and DA interfaces using the NI PXI-7833R multifunction intelligent DA module and the LabVIEW FPGA module.
SCANeR II, a driving simulation software system from OKTAL, completed the test bench architecture. SCANeR conducts driving cycle simulations using a human driver over virtual scenarios with a HuIL approach. To connect SCANeR with the Dynacar dynamic model, the team leveraged an application programming interface (API) for LabVIEW, based in .NET provided by OKTAL. They implemented the connection with the SCANeR II modules through an Ethernet cable.
This approach allowed the developers to play with different parameters while a human drove the components under interest. Similar to a sound jury with noise, vibration and harshness (NVH) research, the driver can identify the user features that please or repel—and the developers can make better decisions that balance safety and efficiency with human subjectivity.
The Robotiker-Tecnalia engineers will continue to use an integrated test bench architecture with real components. The researchers hope that detailed analysis of powertrain configurations will further improve the implementation of advanced control and optimization strategies for energy and power management, as well as electric traction advanced control solutions.
Adrian Martín and his teammates, Iñaki Iglesias, Angel Goti, Jose Luis Calvo and Juanjo Valera, work for Robotiker-Tecnalia.
MORE INFO
WinemanTech
NI
SCANeRsimulation
Tecnalia
NI.com/niweek/keynote_videos
Subscribe to our FREE magazine,
FREE email newsletters or both!Latest News
About the Author

DE’s editors contribute news and new product announcements to Digital Engineering.
Press releases may be sent to them via [email protected].
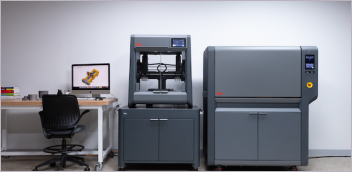
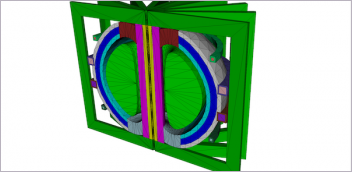
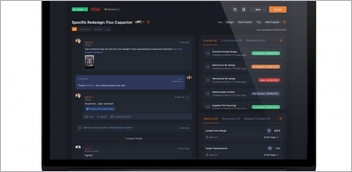
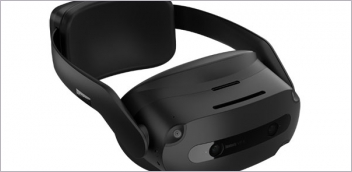