Latest News
July 1, 2013
By Nicholas M. Veikos

Companies use simulation software with mixed results. Some achieve resounding success and serve as exemplars for the industry. Others fail miserably, vowing never to sway from the build-and-test philosophy. In most cases, the differences lie in planning and commitment to execution.
Sometimes planning can be overwhelming when applied to something broad and abstract, so my suggestion is to plan using a well-defined application. If possible, pick a product that is currently in production, but is due for a major redesign. The advantage to this approach is that you will likely be able to answer questions like:
- How many prototypes did we need?
- What design modifications could we not implement because we ran out of time?
- What were the major warranty items in the field?
I recommend against developing your first simulation plan for a high-profile or “bet-the-company” project. The risk is simply too high and the atmosphere too stressful. You must be able to show significant benefits, but look to do it within a relatively stable environment.
With historical information in hand, you can begin to survey how simulation would improve your process. It may be wise to find an experienced engineering consultant to entrust with this step. He or she will be able to work with you to analyze each step in the design process to provide a quantitative and realistic assessment of how simulation can help, what resources it will require, and the expected benefits. He or she will also be able to give an objective opinion of which pieces can be done effectively internally, and which would benefit from expert help from the outside. A good consultant will also be able to identify areas where simulation may not be a practical option.
At the completion of the survey, you may be convinced that simulation is a no-brainer, but don’t fool yourself into thinking you have a plan. You have data, but still need to connect the dots, both for yourself and your management.
Case in Point
Let’s say, for example, that you have identified that your organization will benefit most from a combination of some basic simulation early on to help choose a design direction, followed by more detailed simulation to capture all the physics, minimize prototypes and ensure a robust product. The overall plan for this scenario must consider the following:
- How much simulation will be done internally? If your team has little or no experience, it can probably handle the initial design iterations, but the detailed simulation may be best handled by an expert consultant. As internal skills improve, your team will be able to take on more of the simulation work. A good partner will share what he or she has done to help your engineers learn. Stay away from those who want to keep all they do under wraps, and refuse to share knowledge or models.
- Who will perform the simulation? The latest buzzwords are “democratization of simulation.” While simulation can be used by a wide spectrum of engineers, you want the first adopters in your organization to be the cream of the crop. Train these people first—they will succeed, and so will your plan. Promote geniocracy (a government of geniuses) for now; democracy can come later.
- Which simulation software will you implement? The keys here are to ensure it is easy for non-experts to learn and use; has the functionality that you need today, but is scalable to what you will need in the future; and is supported by engineers who use it to solve real problems. Note that the cost of the software is a small fraction of the implementation cost and the overall benefit, so don’t get hung up on this aspect.
- How much training is required? Customized training, geared to your project, is best. It will make everyone productive immediately. Generic training is better than none at all. No training is OK ... if you don’t mind ruinous failure.
- How much new hardware is required? Work with IT to determine cost and lead time for modern hardware.
Different implementation scenarios will require different plans, but the basics are similar. And like all plans, execution is paramount. But that is a story for another day. DE
Nicholas M. Veikos, Eng.Sc.D. is president of CAE Associates, a Middlebury, CT-based CFD and FEA consulting firm. Send e-mail about this article to [email protected].
More info
Subscribe to our FREE magazine,
FREE email newsletters or both!Latest News
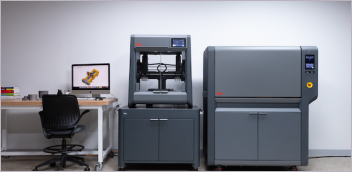
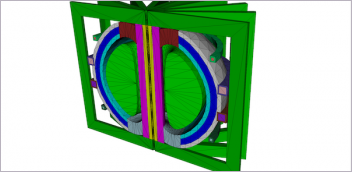
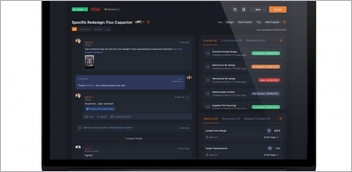
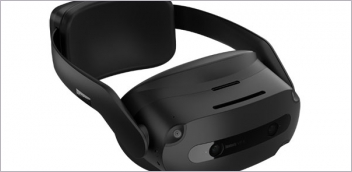